Table of Contents
The Power of 3D Printing
Imagine chocolate as “ink.” 3D printing transforms ordinary materials into unique, intricate designs. It starts with flat image printing, builds layers, and forms a three-dimensional masterpiece. This simple application highlights the technology’s potential for personalization and innovation.
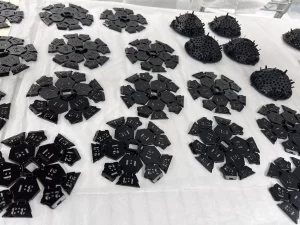
China has developed 3D printing technology for over 30 years. This technology enables manufacturers to create highly complex structures with precision. However, large-scale manufacturing rarely uses 3D printing due to limitations in speed, cost, and material performance. These factors restrict its applications to specific niche fields.
Challenges and Key Materials
Three main issues hinder the large-scale use of 3D printing:
Production Efficiency: Existing printing technologies print too slowly for mass production.
Cost: High material and operational expenses make large-scale use expensive.
Material Performance: The lack of versatile and durable materials limits its scope.
3D printing polymers fall into two categories: thermoplastic and thermosetting materials.
Thermoplastic Materials: These melt when heated and are processed through fused deposition molding (FDM) or selective laser sintering (SLS).
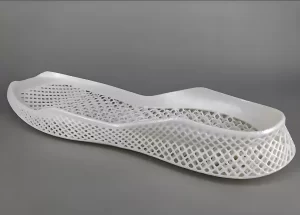
Thermosetting Materials: These harden irreversibly, providing high strength but less versatility in processing.
FDM and SLS Explained
Fused deposition molding (FDM) is the most common 3D printing method. It works by extruding molten thermoplastic material, similar to squeezing toothpaste. The printer solidifies the material layer by layer. While effective for prototypes, its point-by-point process is too slow for low-cost, large-scale manufacturing.
Selective laser sintering (SLS) uses lasers to fuse powdered material into solid structures. This method offers better precision but still struggles with speed and cost limitations.
DLP: A Breakthrough Technology
Digital light processing (DLP) significantly increases printing speed by scanning entire layers at once. Unlike point-forming methods like FDM and SLS, this face-forming technology enhances efficiency.
Manufacturers use low-viscosity liquid monomers for DLP. They leverage material fluidity and surface oxygen inhibition to speed up production. For example, DLP can print molds up to 73 cm high in just one hour. This speed surpasses FDM, SLS, and SLA technologies.
Modern DLP systems can now print thermoplastic polymers at high speeds. This breakthrough expands applications and bridges the gap between thermosetting and thermoplastic material processing.
Applications and Benefits
Key Application Areas
3D printing transforms digital models into physical, highly customized products. It drives innovation across fields such as:
Medical Equipment: Custom prosthetics, implants, and surgical tools.
Aerospace Structures: Lightweight, intricate spacecraft and aircraft components.
Energy Systems: Optimized parts for renewable energy solutions.
Soft Robotics: Flexible and precise robotic components.
Unique Advantages
3D printing offers distinct advantages over traditional manufacturing:
Customization: Manufacturers can create personalized designs on demand without standard templates or machinery.
Faster Iteration: Products update quickly with seamless design adjustments.
Cost Efficiency: Complex structures incur minimal additional costs.
Sustainability: Reduced material waste and energy consumption.
The Future of 3D Printing
Advances in speed, material diversity, and cost efficiency will allow 3D printing to reshape manufacturing. This technology combines customization, precision, and scalability, making it an essential tool for modern industries.
As 3D printing evolves, it will revolutionize production processes. Manufacturers will achieve large-scale, efficient, and highly tailored designs, redefining the possibilities of modern manufacturing.