Table of Contents
Digital additive manufacturing technology
Digital additive manufacturing, or 3D printing, is an emerging rapid solid free-form technology that combines advanced technologies like computer graphics, digital control, laser, electromechanics, and material science. At present, there are many different descriptions of this technology in academia. Some experts refer to it as digital additive manufacturing, incremental manufacturing, or 3D printing. Developed since the 1980s, rapid mold manufacturing is also a key part of rapid prototyping.
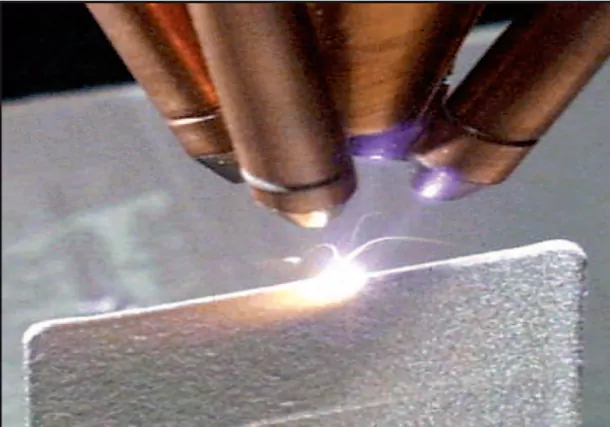
Fig1. Many rapid mold manufacturing methods are derived from printing technology
In the 1980s, market demand changed from a seller’s market to a buyer’s market and gradually globalized. Intense market competition forced manufacturers to design and produce high-performance, affordable products more quickly, making product development speed a core competitive factor. To stay competitive globally, manufacturers relied on rapid development capabilities, while the industry also needed to improve flexibility and control costs through small-batch or even single-piece production.
Therefore, the speed of product development and the flexibility of manufacturing technology have become the key to competition. Technology that converts design data into 3D models allows for quick, intuitive design verification and showcases future product models, helping companies quickly enter the market. Advances in computer technology, material science, CNC, and laser technology have paved the way for new manufacturing methods.
Advantages and selection of rapid prototyping technology
Rapid prototyping technology integrates computer, laser, CNC, and precision transmission technologies. By creating a 3D model, technicians can quickly manufacture product samples without traditional tools or molds, shortening the development cycle, accelerating product updates, and reducing investment risks.
In rapid tooling, there are currently six main rapid prototyping technologies to choose from. Each technology has its characteristics, and companies must weigh their pros and cons when choosing a rapid tooling method. The advantage of these technologies is that they can quickly transform prototypes into products. When manufacturing die-cast products, producing molds is usually the most time-consuming link. Traditional mold manufacturing takes 5 to 20 weeks, while rapid methods reduce it to 1 to 5 weeks. In addition, the cost of rapid mold manufacturing technology is often lower than that of traditional mold manufacturing processes.
Table 1. Comparison between rapid mold manufacturing technology and traditional mold manufacturing process
Complex design advantages of rapid mold manufacturing
Another significant advantage of rapid mold manufacturing is its ability to achieve more complex designs. Rapid mold-making, based on printing methods, allows reshaping models that other manufacturing methods can’t. For example, designers can place cooling channels at precisely designated locations in the mold. Engineers can directly create cooling channels in sheet-shaped molds, improving thermal management and mold quality.
Traditionally, it was thought that these advantages were compromised by rapid mold manufacturing methods resulting in a shorter mold life. However, some rapid prototyping methods today have enabled tool life of up to 100,000 pieces, greatly increasing their value.
Even for molds with a short service life, rapid mold manufacturing still shows significant advantages in production. Advances in geometry and CAD can speed up the conversion of initial molds into production molds, shortening manufacturing times.
Manufacturers are increasingly interested in rapid tooling to quickly obtain market feedback, test new products, and respond to competition. For example, a mold manufacturer needs to produce 500 high-brightness headlight housings for testing on tractors and construction equipment. As more farmers and construction workers work at night, the demand for brighter lamps grows. However, previous plastic headlight shells can’t withstand the heat from high-intensity lights and melt, failing to meet the requirements.
Die-casting headlight housings allow manufacturers to test products under real-world conditions, gather useful data, and improve headlight applicability, meeting user needs and boosting market promotion. Rapid mold manufacturing helps OEMs access new markets and creates more opportunities for mold manufacturers to use castings instead of plastic parts.
Factors to consider when choosing a rapid mold manufacturing method
1. Delivery time
Rapid mold manufacturing can cut delivery times to as little as five weeks, compared to traditional methods. In addition, some manufacturing methods have greater advantages when manufacturing multi-cavity molds. A rapid curing method may take ten days for the first cavity, but each additional one takes only half a day.
2. Quality
Rapid tooling offers flexibility for small batch production and die casting, but many methods can’t achieve H13 steel hardness or full durability, making it unsuitable for large-scale production.
3. Size
Some methods, like direct metal deposition, can create molds up to 41 x 78 x 24 inches, but most rapid mold-making methods are limited to 10 inches.
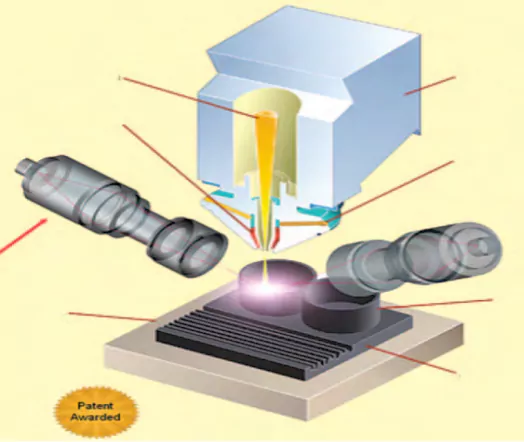
Fig2.Direct metal deposition can be used for larger molds
4. Complexity
Layering materials in rapid mold manufacturing complicates adding complex features like cooling fins or metal units. However, printing technology allows these methods to replicate small surface details easily.
5. Cost
Rapid mold manufacturing is more cost-effective than traditional tooling, but tooling size and material choice affect costs. Using substrates and high-performance materials, like high-thermal conductivity materials in critical areas, can reduce mold insert costs.
The main methods used in rapid mold manufacturing
1. Direct Metal Deposition (DMD)
Direct Metal Deposition (DMD) is an advanced manufacturing technology that uses a CO₂ laser to melt metal powder and create inserts. It typically has a lead time of about a week and can use various metal materials. While mold life is usually estimated at 1,000-10,000 pieces, recent research suggests it may be longer.
DMD technology can produce larger inserts (up to 41 x 78 x 24 inches) with a tolerance of 0.003 inches per 39 inches. Costs range from $2,500 for inserts with base plates to $60,000 for fully DMD-made inserts. The technology’s rapid delivery and wide applicability make it an important part of mold making.
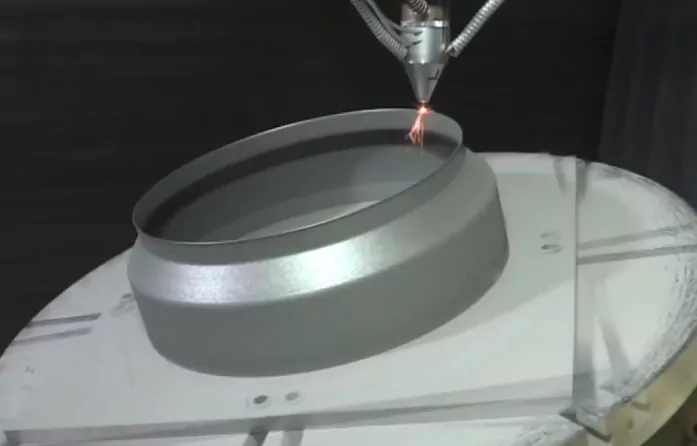
Fig3.Direct metal deposition forming process diagram
2. Selective Laser Sintering (SLS)
Selective Laser Sintering (SLS) is a fast method for rapid mold manufacturing, with delivery in 2 to 3 days. Like Direct Metal Deposition (DMD), it uses CO2 lasers to fuse metal powders but operates differently by layering powder rather than injecting individual particles. This layer-by-layer process accurately manufactures the mold, and the diameter of the metal particles is typically 0.05 mm.
The SLS method supports most metal powders, with mold durability of around 1,000 pieces and a size limit of 8×10×5 inches. In addition, SLS technology can achieve tolerances up to 0.002 inches, making it excellent in high-precision mold manufacturing. The cost of a standard mold insert is typically $6,000 to $8,000, offering manufacturers an efficient and cost-effective solution.
3. Direct Metal Laser Sintering (DMLS)
Direct Metal Laser Sintering (DMLS) is an efficient mold manufacturing method that reduces lead times to 1–3 weeks. The technology relies on 3D CAD-driven automated machines to first create mold inserts by cyclically spreading metal powder layers. Subsequently, the laser sinters the desired cross-section, and these two steps are repeated until the entire insert is completed.
DMLS can manufacture steel and bronze workpieces with durability of 1,000-10,000 pieces, meeting diverse needs. Its maximum size is 9.75×9.75×7.75 inches, with a tolerance of 0.001-0.002 inches per inch for high-precision mold production.
DMLS prices range from $2,000 to $25,000, offering flexible and economical mold-making for various project needs.
4. Rapid Solidification Process (RSP)
Rapid Solidification Processing (RSP) is an efficient, flexible method for rapid mold manufacturing using a rapid or machined prototype. From this prototype, the manufacturing team creates a “female mold” of ceramic material in the shape of the desired mold. Molten H13 or similar tool steel is then sprayed over the ceramic “female mold” to form the final mold. The entire manufacturing process takes approximately 2 weeks.
Once completed, the mold durability is estimated at 1,000 to 10,000 pieces, and some cases may exceed this range. Currently, the largest mold size RSP can manufacture is 7×7×4 inches, with a tolerance of 0.003 inches.
The RSP method is typically $1,500 cheaper than a standard production insert, making it a cost-effective solution for rapid production projects.
5. Laser Engineered NetShaping (LENS)
Laser Engineered NetShaping(LENS) is an innovative mold manufacturing method. This method uses a laser to create a molten pool on a metal substrate, adding metal powder layer by layer. The workpiece moves in the XY plane, while the laser head and powder feeder move in the Z direction to form cross-sectional layers for mold manufacturing.
LENS enables the use of prefabricated substrates as blanks for molds, ideal for complex functional parts. LENS molds typically last 10,000-100,000 pieces, with a size limit of 36×36×60 inches and a tolerance of ±0.005 inches.
Laser-engineered NetShaping (LENS) costs about $250 per cubic inch, with delivery in 2 to 4 weeks, making it an efficient and cost-effective mold production solution for fast market response.
Fig4. Schematic diagram of Laser Engineered NetShaping process
6. Electron beam melting (EBM)
Electron beam melting (EBM) is an advanced mold manufacturing technology similar to selective laser sintering (SLS) and direct metal laser sintering (DMLS), but it uses an electron beam to melt metal powder. EBM uses an electron beam to melt the powder and build the insert layer by layer.
EBM specializes in using iron powder, and the typical life of the mold is expected to be 10,000-100,000 pieces. The maximum mold size that can be manufactured by this technology is 8×8×7 inches, and the maximum practical tolerance is 0.013 inches. The delivery time is usually 3 to 4 weeks, which makes it advantageous to respond quickly to market needs.
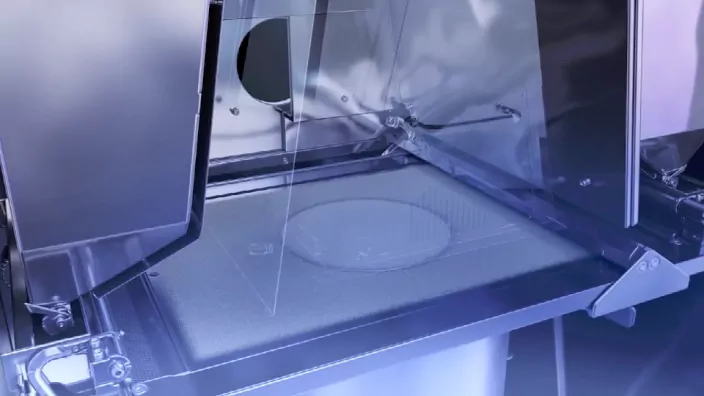
Fig5.Electron beam melting process diagram
In terms of cost, EBM is relatively economical, with manufacturers typically pricing inserts at $2,500-4,500. This makes EBM an efficient and cost-effective metal mold manufacturing solution for a wide range of industrial applications.
Table 2 Comparison of several rapid mold manufacturing technology methods
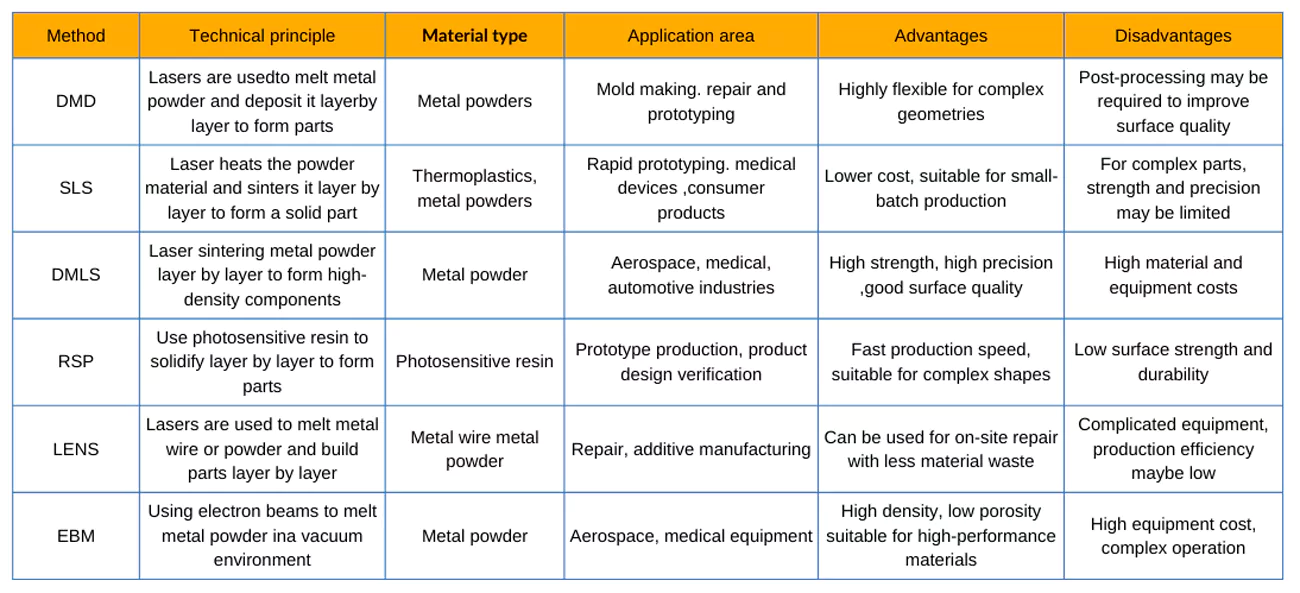
Conclusion
Rapid mold manufacturing technology is crucial in modern manufacturing, offering benefits like shorter delivery times, lower costs, and greater production flexibility. While traditional methods excel in mold durability, rapid manufacturing shines in complex designs and small-batch production, quickly meeting market demands. As technology advances, rapid mold manufacturing will see broader use, driving industry growth.
How does rapid mold manufacturing differ from traditional mold-making?
Unlike traditional methods that are time-intensive and costly, rapid mold manufacturing leverages advanced tools and automation to shorten lead times and reduce costs.
What are the key technologies used in rapid mold manufacturing?
Common technologies include additive manufacturing (3D printing), CNC machining, vacuum casting, and injection molding with rapid tooling.
How does rapid mold manufacturing improve production efficiency?
It reduces the time required for mold design, testing, and production, allowing manufacturers to bring products to market faster.
What industries benefit the most from rapid mold manufacturing?
Industries like automotive, aerospace, consumer electronics, and medical devices benefit from quicker product development and production cycles.
Can rapid mold manufacturing support large-scale production?
Yes, by combining rapid prototyping with traditional production methods, manufacturers can create high-quality molds suitable for both low-volume and high-volume production.
How does rapid mold manufacturing promote process transformation?
It integrates digital design, automation, and advanced materials, enabling manufacturers to adopt smarter, more flexible production workflows.
What are the cost benefits of rapid mold manufacturing?
Reduced material waste, shorter development cycles, and fewer design iterations lead to significant cost savings compared to traditional mold-making methods.
What role does rapid mold manufacturing play in sustainability?
By minimizing waste and enabling the use of lightweight and eco-friendly materials, rapid mold manufacturing contributes to more sustainable production processes.
What are the challenges of adopting rapid mold manufacturing?
Common challenges include high initial investment in technology, the need for skilled personnel, and the integration of new processes into existing workflows.