Table of Contents
The mold industry’s important position in the equipment manufacturing industry is self-evident. Mold technology has become an important symbol to measure the level of development of a country’s manufacturing industry.
Mold technology integrates machinery, electronics, chemistry, materials, computers, precision monitoring, information networks, and other disciplines. Its development represents the continuous progress of high technology.
Mold manufacturing has become one of the industries closely dependent on high-tech industries.
Molds help manufacturers achieve the production advantages of high efficiency, high precision, high complexity, low consumption, and low cost. These advantages are unmatched by other processing methods.
In recent years, China’s automobile and home appliance industries have rapidly developed. The rise of electronic information and other high-tech industries has also contributed. As a result, the mold industry has experienced rapid growth.
This macroeconomic support has promoted the overall development of the mold industry. It has also driven innovation and progress in-mold technology.
The integrated use of CAD/CAM/CAE, high-speed milling for automotive molds, high-pressure injection technology, and networked manufacturing is becoming more popular in the industry.
As the mold industry continues to progress, the technological content of mold products becomes more apparent. This showcases the innovation and technological advances in manufacturing technology.
Mold technology development status
1. CAD/CAM/CAE technology integration
Currently, mold manufacturing enterprises widely use computer-aided design and manufacturing (CAD/CAM) to enhance the efficiency and accuracy of design and production.
By closely integrating design and manufacturing, they can optimize the design. This is the most reasonable approach to mold design and production.
In addition to assisting with modeling, three-dimensional design also generates the necessary NC programs for CNC machining. This improves both machining efficiency and precision.
To further enhance the science and rationality of mold design, many companies now use numerical simulation tools (CAE analysis). They conduct simulation tests on part formability.
Simulation analysis predicts and solves forming process issues like wrinkles, openings, and rebinds, ensuring design feasibility.
Using commercial software like Dynaform, Ansys, MSC, and Modflow, CAD/CAM/CAE technology integrates for three-dimensional, intelligent, and networked development.
So that the design and production of all aspects of the unified platform for collaborative operation.
The integration of CAD, CAM, and CAE technology, along with three-dimensional, intelligent, and network development, allows the design and production aspects to work together on a unified platform. This approach maximizes benefits.
Many mold enterprises in China widely use CAD/CAM technology. However, they still need to strengthen the promotion of CAD/CAM/CAE integration.
2. Automotive mold structure of the complexity and large-scale
The rapid development of the automobile industry has led to the constant launch of new models and styles. This has promoted the design and manufacturing technology level of automobile molds.
The shortened development cycle, high technical content, and strict manufacturing accuracy requirements challenge automotive mold design. As a result, designers use a large number of analog simulation techniques.
Simulation analysis helps identify and solve issues such as wrinkles and springbacks in advance. This analysis optimizes the mold process parameters.
The development of CAE technology focuses on parts springback analysis, automatic optimization of process parameters, and the improvement of the material properties database.
For example, some software lacks complete data on the characteristics of high-strength and ultra-high-strength steel. This makes accurate simulation of the manufacturing process more challenging.
Three-dimensional mold design has become a global standard, especially in the design of large and complex molds, such as automotive cover part molds.
Three-dimensional solid design provides detailed descriptions of mold structures. It also checks for static and dynamic interference to ensure the design’s rationality.
Product lifecycle management (PLM) technology, integrated with the ERP system, manages information throughout the design, production, and service stages. This ensures data accuracy and supports full lifecycle management.
Some large-scale automobile mold enterprises in China have made significant progress. The gap with international technical standards is narrowing.
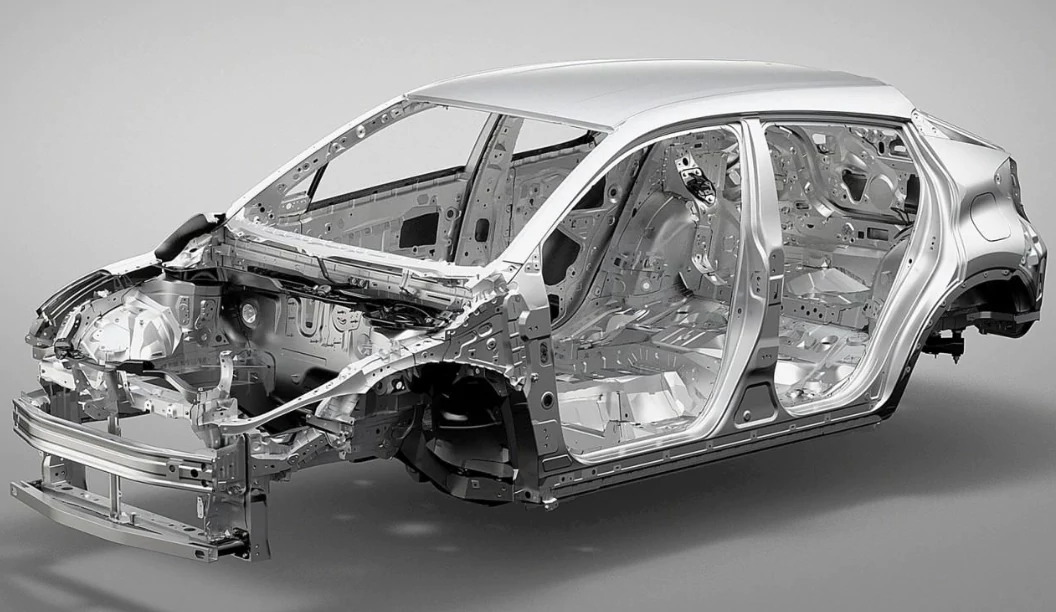
3. High-speed milling technology in the mold processing applications
High-speed milling has become a key technology in mold processing, especially in high-precision, high-quality mold manufacturing.
As spindle speed continues to improve, high-speed milling machines with spindle speeds of up to 100,000 r/min are now available internationally.
In China, high-speed milling machines can reach spindle speeds of up to 60,000 r/min.
High-speed milling processes parts with material hardness above 60 HRC. It works under low temperature, low cutting force, and low thermal deformation.
The surface roughness reaches Ra ≤ 10 µm. Shape accuracy is below 10 µm.
This technology greatly enhances dimensional accuracy and surface quality in mold processing. It is especially beneficial for multi-station dies, precision punching dies, and high-gloss injection molds.
Accuracy reaches 3µm, with super-precision molds achieving 0.3–0.5µm.
4. Application of hot runner, gas-assisted molding, and high-pressure injection technology in injection molds
Hot runner technology uses heating elements. These elements keep mold runners and gates molten. This improves the quality of injection molded parts. It also saves materials and energy.
Companies widely use it in injection molding.
Gas-assisted injection molding uses nitrogen. This improves melt fluidity at lower pressures. It reduces warpage. It also helps mold parts with varying wall thickness.
High-pressure injection molding technology uses gas. The gas creates a hollow structure in plastic. This reduces shrinkage marks. It improves precision and surface quality.
It is widely used in automotive and home appliance molds.
5. Nano-mold technology for microfabrication support
The application of nanotechnology in mold manufacturing, especially the emergence of nano-mold, provides technical support for microfabrication.
The definition of nano-mold includes two types:
(1) Nanoscale precision and size molds include carbon nanotubes and nano-plastic molds. These molds can manufacture extremely small-sized and high-precision parts.
(2) Coating the surface of molds with nanoscale thin-film materials to increase the strength of the molds, reduce wear and tear, and improve the life of the molds.
Nanotechnology can significantly improve the performance and life of molds. It plays an important role in improving the machinability of materials. It also helps reduce friction loss.
6. Reverse Engineering
Reverse engineering (RE) uses high-speed, high-precision instruments to scan a physical object and obtain geometric data.
CAD rebuilds the model, and CAM programming is used for processing.
This technology offers new ideas for mold design and manufacturing, especially for developing complex parts.
Reverse engineering transforms designers’ concepts into actual products, driving mold industry progress.
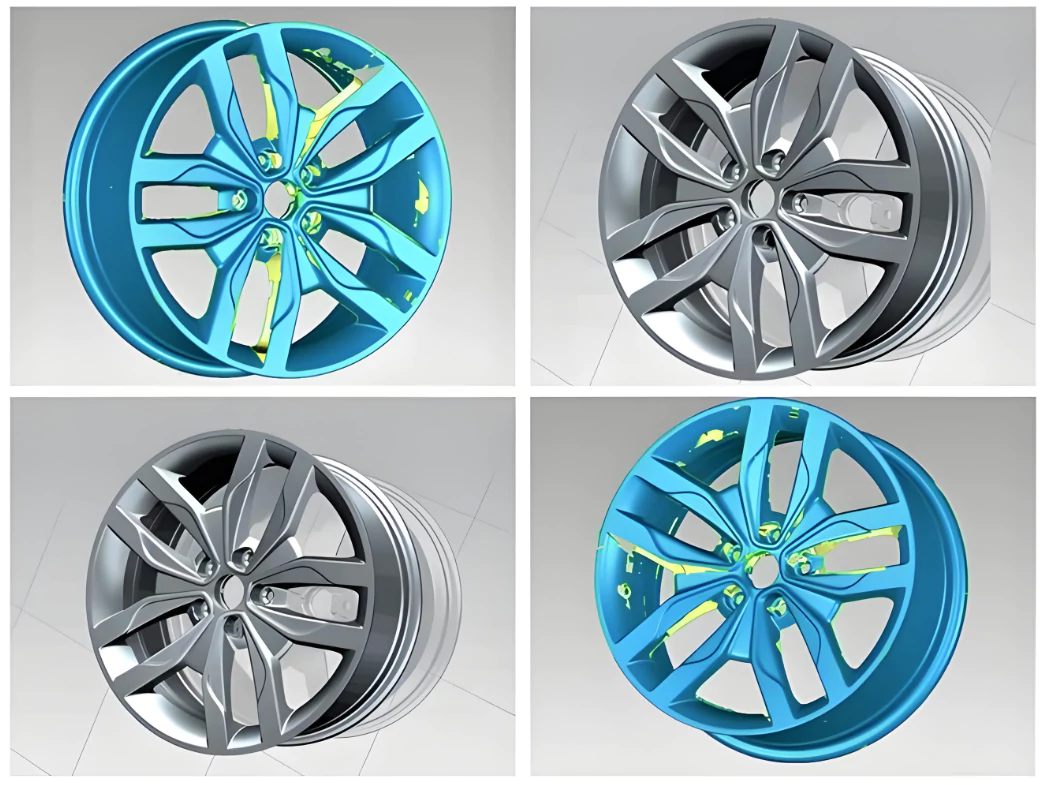
7. Mold heat treatment and surface strengthening technology
Currently, various methods such as common seepage and composite seepage are used for mold heat treatment.
Surface strengthening technologies directly influence the durability and performance of molds.
It uses vacuum heat treatment, CVD, and PVD to enhance wear resistance and hardness.
For example, high-energy beam laser hardening increases hardness in automotive cover mold parts. It reduces deformation and extends the mold life. This process improves product quality.
8. Mold manufacturing industry in the information technology and network technology
Informatization and networking have become the trends in the mold manufacturing industry.
The informatization system allows the mold enterprise to manage everything in real-time. It helps track production progress, control costs, improve efficiency, and enhance competitiveness. It also improves product quality.
The application of informatization management includes project management, resource management, and supply chain management.
As information technology develops, more small and medium-sized mold enterprises build management systems, optimizing processes with modern management ideas.
Networked manufacturing platforms allow small and medium-sized enterprises to compete at low cost.
They enable collaborative design, and manufacturing, and improve production capacity and market response.
Future development focuses on mold technology.
The development focus of China’s mold technology and the industry’s future need to improve the common technology are:
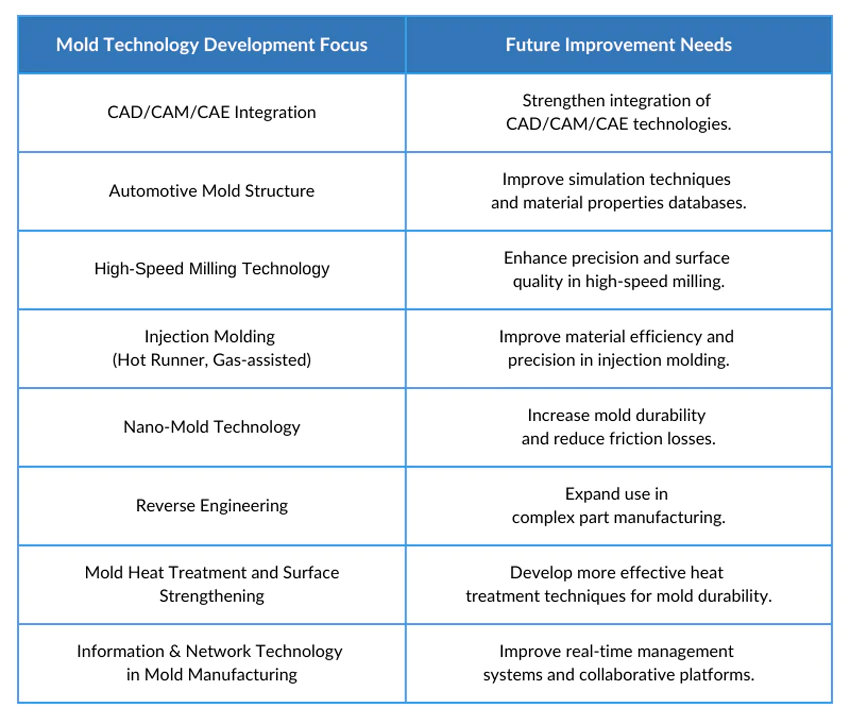
The China Mold Industry Association combined the national pillar industries, key projects, and key engineering needs. It put forward the “Twelfth Five-Year Mold Industry Technology Development Guide and Key Project Proposal.” The proposal mainly includes:
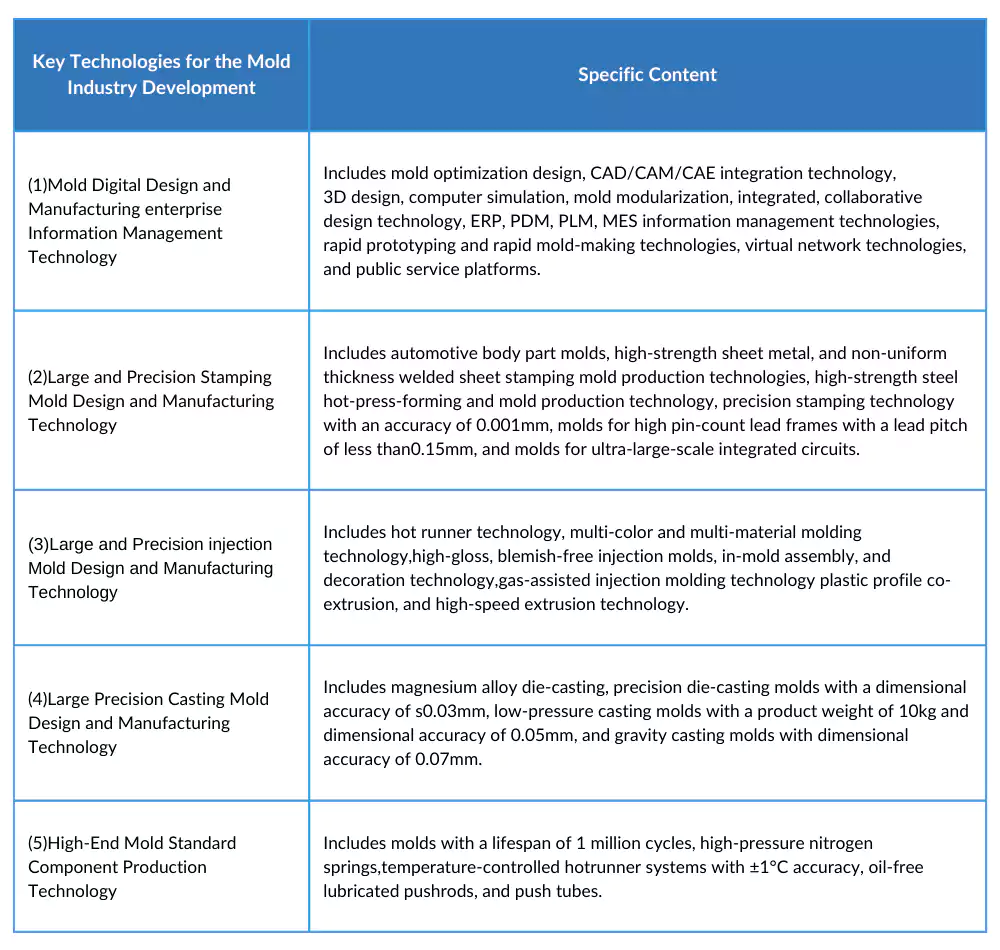
Based on the above key technologies in the mold industry, accordingly put forward 9 key projects:
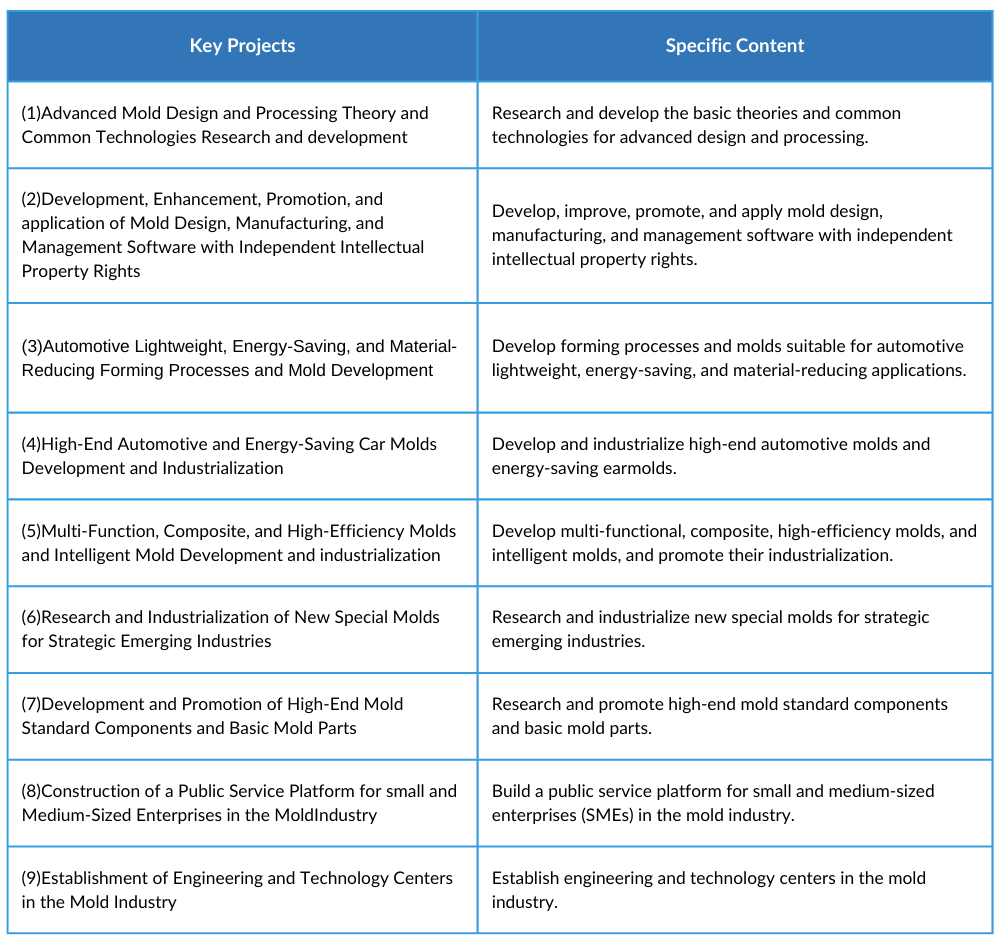
Conclusion
In the past ten years, China’s mold industry and equipment manufacturing industry have made remarkable progress. The level of mold technology continues to improve.
The gap between China and industrially developed countries is gradually narrowing.
Innovation always plays a key role in promoting the development of mold technology. It drives the growth of this high-tech industry.
As the industry continues to develop, the mold industry will focus on innovation. It will also strive to improve its ability for independent innovation.
Information technology leads the way. It promotes the continuous upgrading of mold manufacturing technology. This is a common goal and responsibility for all practitioners in China’s mold industry.