Table of Contents
Rapid prototyping began in 1979 with a Japanese professor’s research. An American company developed the first rapid prototyping equipment in the early 1980s. By 1994, it became widely used. This breakthrough allowed companies to manufacture products directly without traditional tools, giving them a significant advantage over conventional manufacturing companies.
As technology advances, rapid prototyping not only boosts productivity but also shortens product development cycles. Compared to traditional methods, rapid prototyping transforms design concepts into actual products more quickly and at a lower cost. This lets companies optimize designs through trial and error, ensuring quality before market introduction.
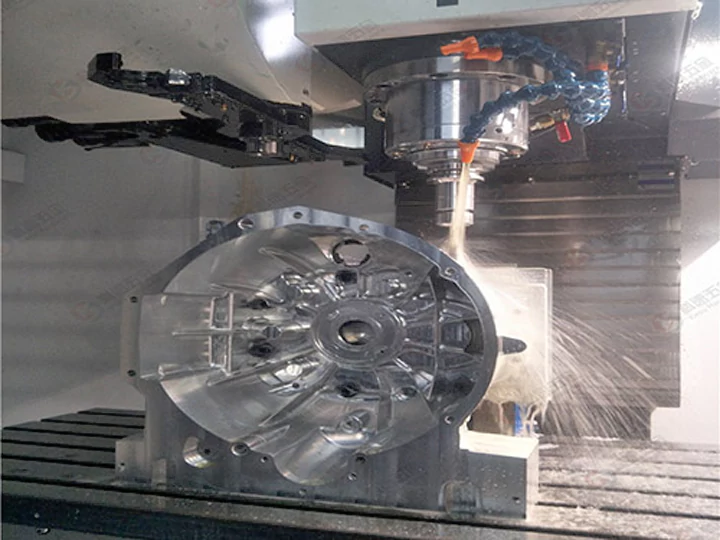
Additive Manufacturing in China
In China, rapid prototyping is widely used, especially for creating parts with complex shapes. For example, it can precisely produce parts with grooves, shoulders, and hollow features. This technology reduces R&D costs and shortens development cycles.
While traditional methods require cumbersome tooling and multiple trials, rapid prototyping speeds up testing. Designers can quickly verify and adjust designs before product release, reducing the risk of substandard products.
Key Features
Rapid prototyping offers several key advantages over traditional manufacturing, particularly in efficiency, precision, and automation. Below are the main features of rapid prototyping technology.

1. Non-contact Processing
Rapid prototyping is a non-contact method. Unlike traditional machining, it avoids direct contact between tools and materials, preventing tool wear. This extends equipment life and maintains high accuracy. It also enables delicate operations to create complex parts.2 Noo Vibration and Low Noise
Traditional machining causes vibration and noise, affecting the work environment and accuracy. Rapid prototyping minimizes vibration since it doesn’t use cutting tools. Many machines operate quietly, improving the work environment. This reduces maintenance needs and increases safety and comfort.
3.No Cutting Waste
Traditional methods create significant waste, especially with complex parts. Rapid prototyping, however, uses a layer-by-layer approach, minimizing waste. This additive manufacturing method boosts resource efficiency and reduces environmental impact.
4. Highly Automated and Continuous Production
Modern machines are highly automated, supporting fully automated production from design to finished product. This reduces manual intervention and increases efficiency. Many machines can operate unattended, enabling 24-hour production, particularly for nighttime or mass production. Automation improves flexibility and responsiveness to market demand.
5 . Flexible Design and Customization
Rapid prototyping offers greater design flexibility than traditional methods. It allows the direct production of complex geometries from CAD files, making it ideal for custom and low-volume production. For example, in healthcare, it can create personalized prosthetics and medical devices, and in aerospace, it can produce lightweight, complex components. Designers can achieve shapes impossible with traditional methods, without extra costs.
6.Rapid Prototyping and Iteration
Rapid prototyping significantly shortens development cycles. Traditional development takes months or years for molding, prototyping, and testing. With rapid prototyping, designers can create prototypes in days and make multiple iterations. This accelerates testing, evaluation, and optimization, speeding up time-to-market.
7.Adaptable Material Selection
Rapid prototyping supports various materials, including plastics, metals, and ceramics, each suited to different industries. Plastic is ideal for lightweight prototypes, while metals are used for strong mechanical parts. The growing variety of materials expands rapid prototyping’s flexibility. As material technology improves, new materials will further enhance its applications.
8.Lower Equipment Maintenance Requirements
The non-contact nature of rapid prototyping reduces equipment wear and tear. Traditional machining requires frequent maintenance due to tool wear, affecting performance. Rapid prototyping uses lasers and precision devices, reducing wear. This lowers maintenance costs and extends equipment lifespan.
These features make rapid prototyping crucial in modern manufacturing. It enhances productivity, reduces costs, and offers the potential for better product quality, faster development, and personalized customization. As technology advances, rapid prototyping will become a key competitive advantage for many industries.
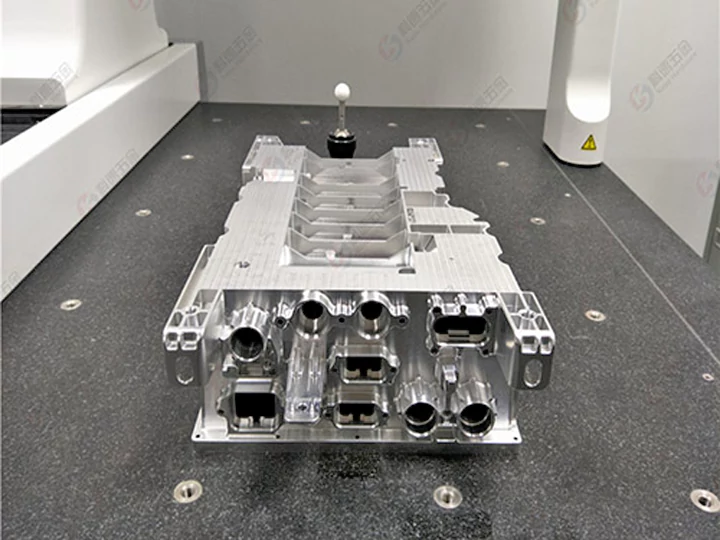
Application Fields
Rapid prototyping is widely used in automotive, medical, aerospace, and other industries. In automotive manufacturing, it quickly produces prototype parts, crash tests, and assembly tests. In the medical field, rapid prototyping creates customized prosthetics, medical device prototypes, and personalized surgical plans.
Globally, over a dozen rapid prototyping technologies show great potential. While still in the early stages, these technologies will expand as they mature.
Outlook for the Future
As rapid prototyping continues to evolve, its advantages will become even more prominent. Companies mastering these technologies will dominate future markets. We believe that rapid prototyping will soon become a mainstream manufacturing technology, driving the industry toward greater intelligence and efficiency.
By continuously optimizing and expanding its applications, rapid prototyping will not only change how products are made but also revolutionize the entire industrial chain, bringing innovation and new possibilities to the manufacturing industry.