Table of Contents
Prototype injection molding is a common manufacturing method for plastics. As the name says, prototype mold is specially designed for the rapid production of prototypes. This method came into being to produce economic and quick samples, prototypes, and small series. Prototype injection molding services are provided by many companies and you can reach them out easily. The following are all about Prototype Injection Molding.

WHAT IS PROTOTYPE INJECTION MOLDING?
When companies need to produce parts rapidly, they use rapid prototype injection molding. The parts produced in rapid injection molding are used for creating prototype parts for the design analysis. The parts produced with this method are not used as finished products. They serve as a bridge to production, creating parts while the production mold is being made or processed. Instead of being a primary production method, rapid prototype injection molding focuses more on research and development.
Also Read:
How Has CNC Turning And Milling Machining Changed The Manufacturing Industry?
What is CD pattern processing?
WHAT IS PROTOTYPE TOOLING?
Prototype tooling is a common method in injection molding, offering lower-cost tooling. It supports a high number of parts and uses production materials. Typically, it’s built with aluminum cores and cavities. While there are several options for prototype tooling, tools and samples can be completed in a few weeks. This option is ideal for quick prototypes when parts are simple, tolerances are loose, and functions aren’t critical. However, prototype tooling has limited flexibility for design or dimensional changes after the tooling is completed and sampled.
In summary, both Prototype Tooling and Prototype Injection Molding are important, but they serve different purposes. Prototype Tooling focuses on mold manufacturing and rapid prototype generation, while Prototype Injection Molding uses the injection molding process to quickly and accurately produce product prototypes.

HOW DOES INJECTION MOLDING WORK?
Many industries also provide injection molding services, following the same basic procedure. Material granules are fed into a heated barrel via a hopper, melted by heater bands and the friction of a screw barrel. The molten plastic is then injected through a nozzle into a mold cavity, where it cools and hardens to the cavity’s shape. Once the part solidifies, the mold tool, mounted on a movable plate, opens, and ejector pins remove the part. After finalizing the product design, molds are made from metal, steel, or aluminum and precision-machined to match the desired part features.
STEP-BY-STEP INJECTION MOLDING PROCESS:
Various stages in the injection molding process are:
1. Mould closure
Before starting, the injection molding machine’s mold must be fully closed to prevent material leakage during injection. The mold-closing action is controlled by either a hydraulic or electric system to maintain sufficient clamping force.
2. Plastic heating and melting
The raw material, usually plastic pellets, is fed from a hopper into a heated barrel. The barrel heats the plastic granules to their melting point using a heater and the shearing force of the rotating screw, creating a molten material with good flowability.
3. Injection
The molten plastic is rapidly injected into the mold cavity at high pressure using a screw or plunger.
The injection pressure and speed need to be precisely controlled to ensure that the plastic fills the cavity evenly.
Time control is also important to prevent the plastic from cooling prematurely or creating voids.
4. Pressure Holding Stage
After the plastic has been injected into the mold, pressure continues to be applied to compensate for volume changes due to cooling shrinkage.
This stage ensures that the density and dimensions of the product are stabilized and that air bubbles and distortion are reduced.
5. Cooling
The plastic in the mold is gradually cured by a cooling system (e.g. water circulation or air cooling).
Cooling time usually accounts for the majority of the entire injection molding cycle, which directly affects production efficiency and product quality.
6. Mould opening and ejection
After the plastic is cooled and molded, the mold is opened and the finished product is ejected from the mold using an ejector pin or other mechanism.
It must be ensured that the ejection process will not damage the product.
7. Post-processing
The product removed from the mold may require some subsequent operations, for example:
Trimming of excess burrs.
Surface treatment (e.g. painting, polishing).
Quality inspection (e.g. size, hardness test).
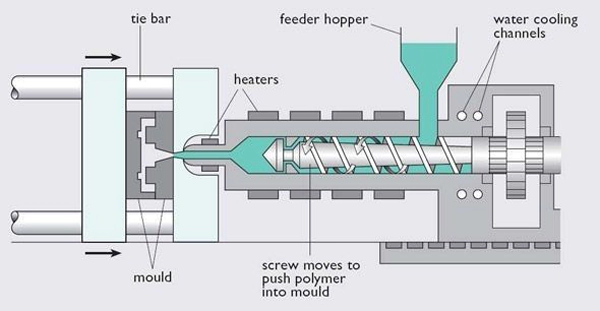
RECOMMENDATIONS FOR OPTIMISING THE INJECTION MOULDING PROCESS
1. Reduce cooling time
The cooling phase usually occupies more than 60% of the injection molding cycle and is the key to improving productivity. To shorten the cooling time, the cooling system of the mold can be optimized, for example, by designing efficient cooling water circuits inside the mold to ensure that the coolant is in full contact with the surface of the mold cavity. In addition, the use of high thermal conductivity materials (e.g. beryllium copper alloy) for key parts of the mold helps to conduct heat quickly. For molds with complex shapes, variable-temperature cooling technology (e.g. rapid heating/cooling cycles) can be used to further improve cooling uniformity and speed.
2. Improve material utilisation
Properly designed gates and runners can significantly reduce scrap waste. For example, by adopting hot runner technology to avoid the problem of residual material in traditional cold runners. In addition, optimizing the mold layout to reduce unnecessary feed positions and runner lengths can also help to reduce material wastage. The selection of high-performance plastics can further enhance product performance, thereby reducing the defective rate and indirectly improving material utilization.
3. Quality stability
Quality stability directly affects the consistency of injection-molded products. By installing sensors to monitor real-time pressure, temperature, and speed changes during the injection molding process, parameters can be quickly adjusted to avoid defects. The use of closed-loop control systems further improves production accuracy, especially for complex products or mass production requiring a high degree of consistency.
4. Automation upgrades
Automation technology can significantly reduce manual intervention and increase efficiency. For example, robots can automate picking and deburring operations while reducing the risk of human damage. Automated inspection equipment (e.g., machine vision) can screen for defective products in real-time, dramatically improving quality control efficiency. The integration of these technologies makes injection molding production smarter and more efficient.
HOW MUCH IS A PLASTIC INJECTION MOLD?
The price of plastic injection molds is affected by a combination of factors, which together determine the final cost of the mold. First, the complexity and design accuracy of the mold are key factors in determining the price. Complex mold structures, such as multi-cavity design, side core pulling mechanism, or hot runner system, not only increase the difficulty of processing but also increase the requirements for materials and processes, thereby pushing up the price of the mold.
Secondly, the size of the mold and the quality of the required materials are also important factors affecting the price. Large molds require more materials to manufacture and have higher requirements for the strength and toughness of the materials, which naturally increases the manufacturing cost. At the same time, high-quality materials are often more expensive, further increasing the total price of the mold.
Furthermore, the production batch will also have an impact on the mold price. Although the initial investment in the mold may be high, as the production batch increases, the mold cost per product will gradually decrease. Therefore, for large-scale production, the relative cost of the mold will be lower.
In addition, the technical level and production efficiency of mold processing are also important factors in determining the price. Advanced processing equipment and processes can improve the precision and durability of the mold but also increase the manufacturing cost. At the same time, an efficient production process can shorten the mold manufacturing cycle and reduce labor costs, thus affecting the mold price to a certain extent.
A small, cavity plastic injection mold usually costs between $1,000 and $5,000. Very large or complex molds may cost between $80,000 and more. So, according to a rough estimate, a typical mold costs $12,000.
WHAT ARE THE TYPES OF INJECTION MOLD?
Injection mold is the core tool in the injection molding process, its structure and function directly affect the product quality and production efficiency. According to different classification standards, injection molds can be divided into the following types:
1. Classification by structure
Injection molds can be divided into two-plate, three-plate, and multi-plate molds:
Two-platen mold: This is the most common type of structure, consisting of a moving mold and a fixed mold, and is suitable for most simple or moderately complex plastic products.
Three-platen molds: a middle plate is added to the two-platen type to separate the pouring system and the product, suitable for products with complex gates.
Multi-plate molds: the design is more complex and is often used for products with complex shapes or multi-point glue feed.
The choice of these structures is usually determined by the complexity of the shape of the product and the production requirements.
2. Classification by function
According to the function, molds can be divided into hot runner molds and cold runner molds:
Hot Runner Moulds: Keeping the plastic in a molten state using a heating system, without the need to cut out the pouring system after cooling, can significantly reduce material wastage and at the same time increase production efficiency. Hot runner mold is more suitable for high precision and mass production, but the cost is higher.
Cold Runner Moulds: The melt is cooled to form the sprue system, which requires additional cut-outs and is suitable for the production of simple products.
3. Classification by cavities
Single-cavity molds: only one product can be molded at a time, suitable for low volume or customized production.
Multi-cavity molds: can form multiple products at a time, are suitable for mass production, can significantly reduce unit costs, and improve production efficiency.
In addition, there are some specially designed molds, such as:
Side core extraction molds: used for molding products with lateral grooves or threads.
Stacked molds: further improve production efficiency by stacking the cavity layout, suitable for mass production scenarios.
The above classification not only demonstrates the diversity of injection molds but also highlights their flexibility in different production scenarios. For example, the choice of mold type usually depends on a combination of product design requirements, production volumes, and budgetary costs.
RUIYI’S INJECTION MOULDING SERVICES IN CHINA
Ruiyi specializes in high-quality injection molding services, providing customers with comprehensive solutions from rapid prototyping to high-volume production, covering a wide range of industries such as automotive, medical devices, smart home, robotics, and automation.

Our 10,000-square-meter factory houses over 200 high-end machines, including injection molding machines, five-axis CNC machining centers, and mill-turn machines. The advanced equipment processes a wide range of plastics like ABS, PP, PC, POM, PA, and engineering plastics (e.g., PEEK, PPS). It also offers various surface treatments, such as spraying, plating, and silk-screen printing, ensuring high-quality functionality and appearance.
Ruiyi holds ISO9001:2015 certification and closely monitors the production process to meet our customers’ precision and durability requirements. We combine efficient production with a strong quality control system to deliver flexible, reliable customized services.
With an international outlook and local support, Ruiyi serves both the Chinese market and expands global cooperation. We aim to become a trusted long-term partner in injection molding.
For high-precision plastic mold injection molding, contact Ruiyi CNC Machining.