Many types of pressure play a role in the manufacture of plastic injection molded parts. We’ve explained the importance of clamping pressure; now, let’s look at injection, holding, and back pressure. To manufacture successfully, product developers must understand how the balance of forces affects part quality, productivity, and product cost.

What is injection pressure?
A reciprocating screw pushes molten resin into a mold cavity that is 95% filled. Mold clamping pressure balances the resin, considering the part size and gating.
Why do I need back pressure?
Back pressure provides extra time for the heavy-duty recesses of the reciprocating screw to thoroughly mix the next batch of resin.
The cutting action of the grooves heats the resin and maintains a consistent density from shot to shot. The groove also helps to thoroughly mix any masterbatch color pigments in the resin.
The process technician controls this pressure, as well as other parameters, to prevent the resin from over-mixing and degrading due to excessive shearing.

What is Pressure Retention?
Holding pressure or holding pressure is necessary to fill the last 5% or so of the mold cavity. The process reduces this pressure from the initial injection pressure and holds it longer for several important reasons.
First, the exhaust port in the mold must allow trapped gases to escape. In addition, holding pressure helps the molecules in the resin align and reach their highest density. Third, thin-walled portions of the part also need time to fill. Finally, pressure retention and good tool design are critical to relieve stresses in the part. However.
another limitation must be balanced against holding pressure. The process must fill the cavity quickly before the gate “freezes” and becomes clogged with cured resin. Therefore, the process engineer needs to carefully calibrate these forces over a period determined by the temperature and chemical properties of the plastic.
What is back pressure?
Back pressure is the resistance within the barrel of an injection molding machine that prevents the screw from returning to its starting position. The operator deliberately creates this resistance by controlling valves on the machine to limit the rate at which hydraulic fluid returns to the reservoir.
Is faster injection always better?
Often, product developers want to produce as many parts as possible because it reduces labor costs, which is an important consideration for large orders. However, some limitations cannot be avoided.
First, when the cavity is empty, there is very little resistance to flow so the cavity can be filled quickly and easily at the beginning of the cycle. However, when the cavity is about 95% full, there is a sudden spike in pressure that can cause overflow or premature mold opening. This can damage your parts and machine. To avoid this, the process must reduce the injection pressure in a controlled manner at the so-called changeover point. At this stage, the cycle switches to holding pressure.

How do these pressures affect your parts?
You want to maximize the number of injected parts per hour in injection molding to reduce production costs and get your parts to market faster. However, responsible process control technicians need to carefully balance multiple parameters within the machine to control quality and ensure consistency from one cycle to the next.
Learning more about how this process works can help you communicate more effectively with your suppliers, while also emphasizing the importance of good mold design. Learn more when you upload a CAD design for a free quote.
The Key to High-Quality Production
Choosing the right aluminum die-casting mold is essential for producing high-quality aluminum alloy castings. A well-designed and properly maintained mold improves the production process. It also ensures the final product meets strict quality standards. Here’s how die-casting molds influence production and why they are so important.
Role in Production
Appearance and Tolerances
The die-casting mold determines the external appearance and dimensional accuracy of castings. Manufacturers depend on precise molds to meet design specifications. If the mold fails, the product may not meet customer expectations, resulting in rework or rejection

Thermal Balance
Die-casting molds regulate and adjust thermal dynamics during the production process. Proper thermal management ensures consistent casting results, reduces defects, and preserves the product’s structural integrity. Without thermal balance, issues such as shrinkage or warping may occur.
Structural Strength
The compressive strength of the mold plays a critical role in the durability and quality of castings. Strong molds withstand high-pressure conditions during die-casting. They ensure defect-free products and reliable performance over extended production cycles.
Maintenance Importance
Die-casting molds require regular cleaning and maintenance to sustain productivity. Upkeep extends the molds’ lifespan, minimizes downtime, and ensurfor improving efficiency and reducing production issues.
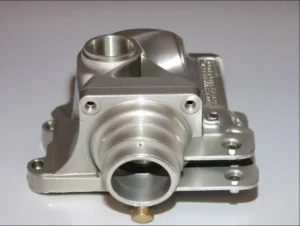
Choosing Reliable Partners
Experienced manufacturers are crucial for aluminum die-casting success. Ruiyi, a leading Chinese aluminum alloy processing company, has extensive experience and collaborates with clients worldwide. Their commitment to innovation and quality has earned them widespread trust.
Ruiyi leverages advanced technology and precision to deliver high-quality molds and products that meet international standards. Partnering with such companies ensures reliable support and superior products, helping businesses stay competitive.
Conclusion
Die-casting molds are foundational to aluminum die-casting production. They define appearance,ensurestructural strength, and regulate thermal dynamics. Investing in high-quality moldsandpropermaintenance is essential for superior results and long-term industry success.