Table of Contents
Since the 1980s, rapid prototyping (RP) has advanced in systems, and materials, and led to the growth of rapid tooling (RT) and rapid manufacturing (RM) technologies. RP has shortened product design and manufacturing cycles, improved first-time yields, and reduced development costs, transforming the manufacturing industry. It combines computer, CNC, laser, and material technologies.
The development and current situation of rapid prototyping technology
Rapid prototyping (RP) refers to the process of quickly creating physical models from digital designs, typically using computer-aided design (CAD) software and additive manufacturing technologies. By building objects layer by layer, RP accelerates product development, reduces costs, and enhances innovation across various industries.
1. The Origins and Early Development
The concept of layered manufacturing dates back to the 1980s. In 1981, Japanese researcher Hideo Kodama first proposed the idea of 3D printing using photocuring technology to construct objects layer by layer. However, it was American inventor Charles W. Hull who brought this concept to fruition. In 1986, Hull developed the first stereolithography (SLA) technology, a process that allowed for the creation of three-dimensional objects by solidifying liquid resin with ultraviolet light. Hull’s invention laid the foundation for modern 3D printing and rapid prototyping.
In 1988, Hull founded 3D Systems and launched the first commercially available 3D printer, which opened up new possibilities for rapid prototyping. This technology significantly reduced the time and costs associated with creating prototypes, leading to rapid advancements in manufacturing and product development.
2 . The Global Expansion and Technological Advancements
The 1990s saw rapid prototyping technology become more widely commercialized, with the emergence of various methods such as SLA, LOM (Laminated Object Manufacturing), SLS (Selective Laser Sintering), and FDM (Fused Deposition Modeling). These technologies allow for faster, more efficient production of prototypes and parts, making them accessible to a broader range of industries.
In China, the adoption of rapid prototyping technology began in the early 1990s. Tsinghua University, a leading research institution, introduced the SLA-250 system from 3D Systems and began conducting research and development on rapid prototyping. The university went on to develop the “M-RPMS-II” multifunctional rapid prototyping manufacturing system, which combines LOM and FDM techniques.
Other Chinese institutions followed suit: Huazhong University of Science and Technology developed an HRP system using paper for LOM, Xi’an Jiaotong University created an LPS system based on SLA and CPS, and Nanjing University of Aeronautics and Astronautics developed an RAP system using SLS.
By the mid-2000s, over a dozen rapid prototyping technologies had emerged, including 3DP (Three-Dimensional Printing), SDM (Selective Deposition Modeling), and SGC (Solid Ground Curing). However, SLA, LOM, SLM (Selective Laser Melting), and FDM remained the most widely adopted methods for industrial use.
3. Modern Applications and Innovations
As rapid prototyping technology has matured, its applications have expanded across various industries. In 2014, Organovo used 3D printing to create biological tissues, advancing medical research and reducing the need for animal testing. In 2016, GE Aviation improved the performance of its LEAP engine nozzle through 3D printing, demonstrating the technology’s potential to enhance the performance of complex aerospace components.
By 2018, Peking Union Medical College Hospital began using 3D printing for personalized surgical models, improving precision and patient safety. In 2019, Geely Auto used rapid prototyping to accelerate vehicle development, streamlining the design and testing phases of car production. In 2021, BGI applied 3D printing in affordable housing construction, showcasing the technology’s ability to revolutionize the construction industry.
These milestones reflect the diverse and transformative impact of rapid prototyping across industries, from healthcare and aerospace to automotive and construction.
The basic prototyping principle of rapid prototyping technology
Rapid prototyping (RP) technology combines 3D CAD, reverse engineering, layered manufacturing (SFF), material removal (MPR), and material addition (MAP) to quickly create physical prototypes by layering materials based on CAD data.
Fig 1. Rapid prototyping system workflow
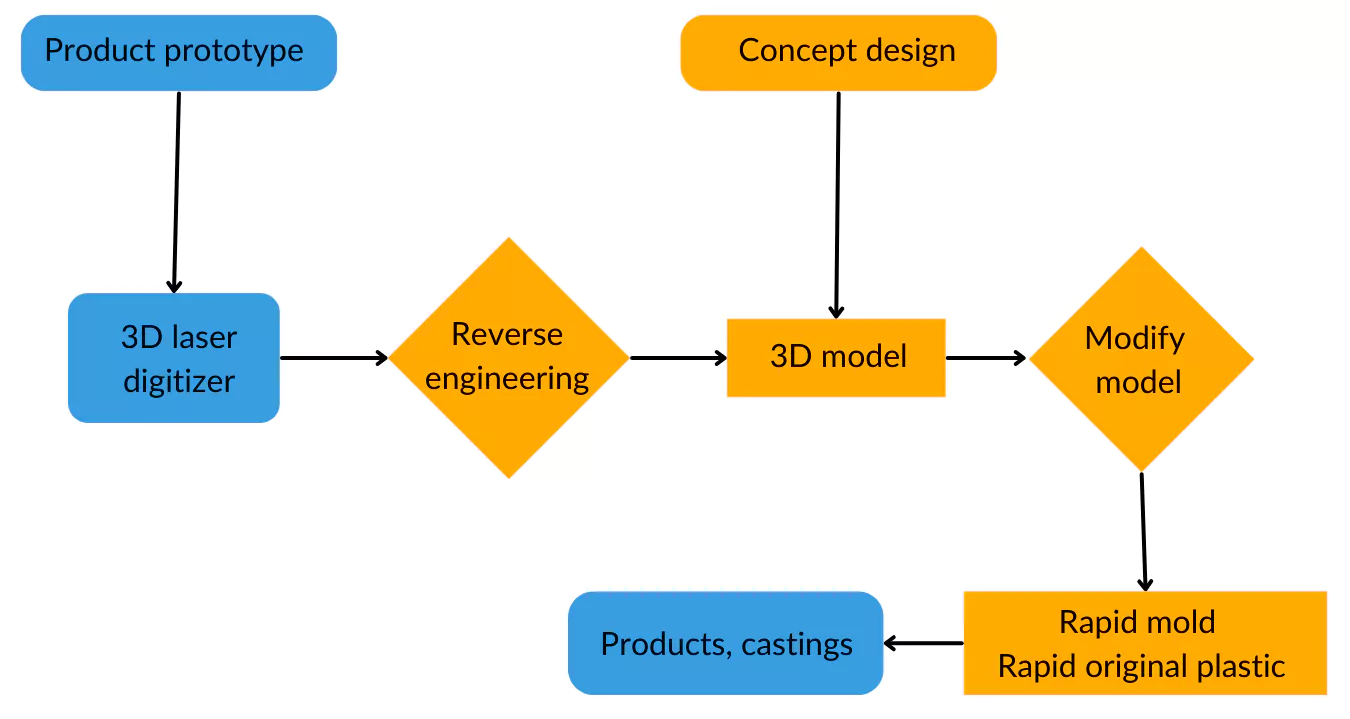
There are over ten rapid prototyping methods, with the most common being SLA, SLS, LOM, and FDM. These methods use additive manufacturing, combining material properties and advanced processes, and are closely linked to developments in other fields.
1. Stereolithography (SLA)
Stereolithography (SLA) technology magically transforms liquid resin into delicate three-dimensional objects. Through precise laser scanning, the resin solidifies in an instant, forming a layered structure with amazing details and smooth surfaces. Every time the laser scans, it is as if an artist is gently drawing on the canvas, eventually presenting complex designs and elegant shapes. This method is currently the most intensively studied, most mature, and most widely used rapid prototyping method in the world.
Companies researching SLA methods include 3D Systems, EOS, F&S, CMET, D-MEC, Teijin Seiki, Mitsui Zosen, and Xi’an Jiaotong University. 3D Systems’ SLA technology dominates the global market, with significant advancements since the 1988 launch of the SLA-250 model, followed by the SLA-250HR, SLA-3500, and SLA-5000 models in 1997.
The SLA-3500 and SLA-5000 use semiconductor-excited solid lasers with scanning speeds of 2.54m/s and 5m/s, respectively, and a minimum molding layer thickness of 0.05mm. The new Zephyer recoating system applies a 0.05-0.1mm cured resin layer using a vacuum adsorption scraper, reducing molding time by 20%. Launched in 1999, the SLA-7000 offers a similar molding volume to the SLA-5000 but with a scanning speed of 9.52m/s, four times faster molding speed, a minimum layer thickness of 0.025mm, and double the accuracy. Extensive research has been conducted on the SLA molding mechanism, part deformation control, and accuracy improvement.
2. Layered Object Manufacturing (LOM)
Layered manufacturing is an advanced additive manufacturing technology that builds complex three-dimensional objects by adding materials layer by layer. This method uses a CAD model, breaks it into thin layers, and stacks them to form the complete object.
This technology’s core lies in its flexibility and efficiency, enabling complex shapes and internal structures that traditional methods can’t achieve. Layered solid manufacturing effectively reduces material waste by adding material only where it is needed.
Companies researching LOM technology include Helisys, Huazhong University of Science and Technology, Tsinghua University, Kira, Sparx, and Kinergy. Helisys launched the LOM-1015 model in 1992 (380mm×250mm×350mm) and the LOM-2030H model in 1996 (815mm×550mm×508mm), reducing molding time by 30%. Helisys expanded material options, adding plastic and composite varieties to its LPH, LPS, and LPF paper series. Kira’s PLT-A4 model uses super-hard knife cutting and selective bonding. Tsinghua University developed the SSM series, while Huazhong University of Science and Technology introduced the HRP series, offering high performance at a good price.
3. Selective Laser Sintering (SLS)
Overview of Selective Laser Sintering (SLS) Technology and Its Advantages
Selective laser sintering (SLS) is an additive manufacturing technology where a laser sinters powdered materials layer by layer into a 3D object. The process spreads powder on the build platform, and the laser sinters it according to the design outline. After each layer, the platform lowers, and new powder is spread to continue sintering until the model is complete.
SLS technology can use various powder materials like nylon, metal, and ceramic, offering strong adaptability. It produces parts with good mechanical properties and complex geometries, ideal for functional prototypes, custom parts, and small-batch production. Since it does not require a support structure, designers have greater design freedom, allowing them to explore more innovative solutions.
Advancements in SLS Technology and Materials by Leading Companies
DTM, EOS, and Beijing Longyuan are researching SLS. DTM launched Sinterstation2000, 2500, and 2500P1us in 1992, 1996, and 1999 respectively. The molding volume of 2500P1us is 10% higher than before. By optimizing the heating system, we reduce the auxiliary time and improve the molding speed. Beijing Longyuan launched an AFS-300 molding machine and several materials. Huazhong University of Science and Technology developed the HRPS-I molding machine.
DTM launches new products annually, including Dura Form GF material for higher precision and smoother surfaces, So-mos 201 elastic polymer with rubber, heat, and chemical resistance, and Rapid Steel 2.0 stainless steel powder for leak-proof flexible parts like pipes and gaskets. Rapid Steel 2.0 molds can produce up to 100,000 injection-molded parts with a shrinkage rate of just 0.20%, ensuring high precision and finish with minimal polishing.
4. Fused Deposition Modeling (FDM)
Fused Deposition Modeling (FDM) is a common 3D printing technology that many industries use for rapid prototyping and small-batch production. Its principle is to heat thermoplastic material to a molten state and extrude it layer by layer through a nozzle to build a 3D object based on a computer model.
In deposition modeling, the printer heats wire to a molten state and deposits it onto the platform in a specific path. After each layer cools, the next layer will adhere closely to it to form a stable structure. This method can achieve complex geometries and fine details with high material utilization.
The main companies researching FDM are Stratasys and MedModeler. Stratasys developed the first FDM-1650 (table of 250mm×250mm×250mm) in 1993 and then launched FDM-2000, FDM-3000, and FDM-8000. Among them, the table of FDM-8000 is 457mm×457mm×610mm. Tsinghua University launched the MEM model. Stratasys launched the FDM-Quantum model in 1998, which features a maximum modeling volume of 600mm×500mm×600mm, making it particularly eye-catching.
The Magna Drive extruder system enables independent control of two extruders, increasing modeling speed by five times. In 1998, Stratasys partnered with Med Modeler to develop the MedModeler for hospitals and research institutions using ABS materials. In 1999, they launched the Genisys Xs, which supports polyester thermoplastics and has a modeling volume of 305mm×203mm×203m m. Table 1 shows several typical rapid prototyping processes.
Table 1 Comparison of several typical rapid prototyping processes
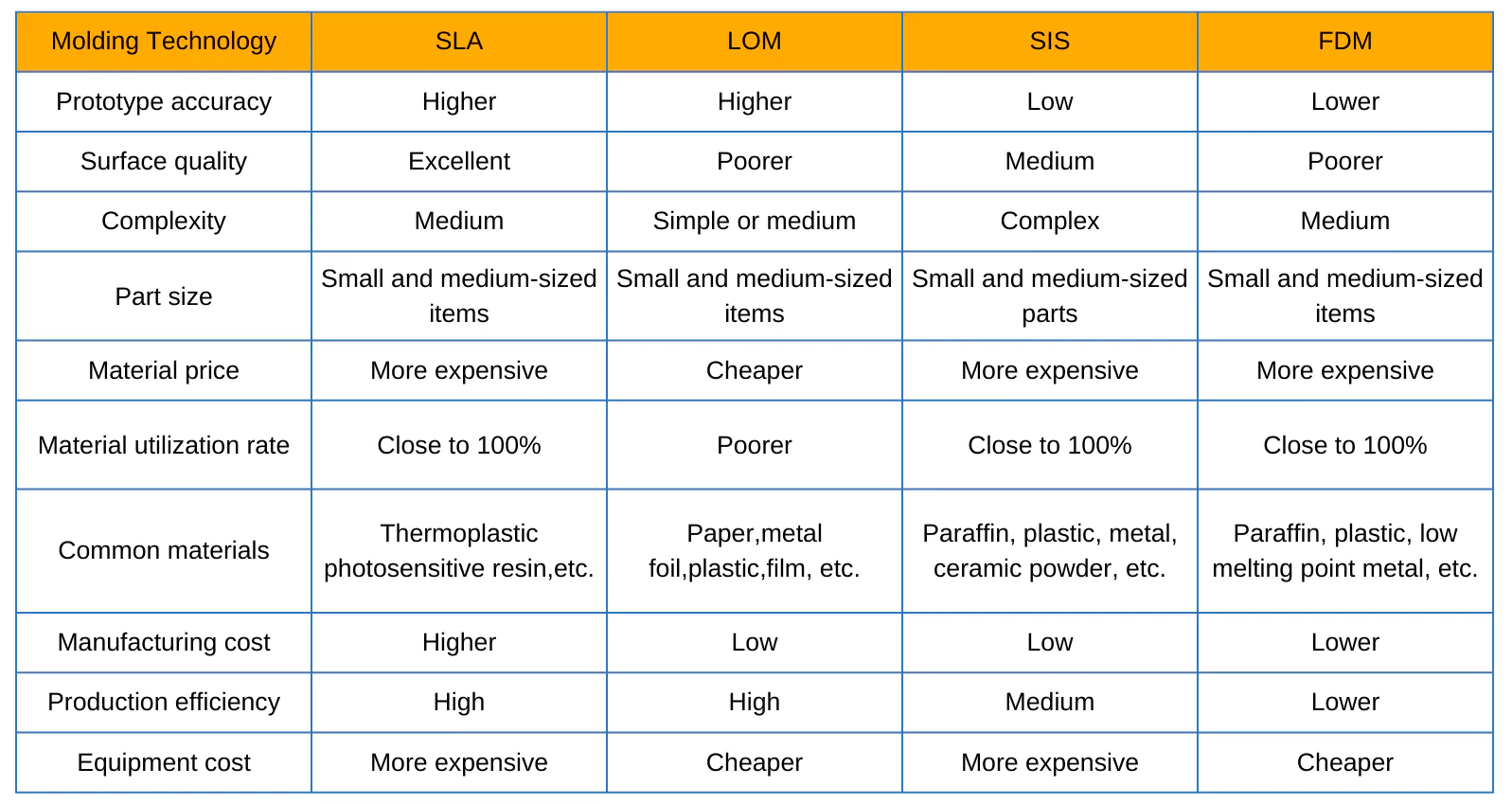
Characteristics of Rapid Prototyping Technology
1. Rapidity
Rapid prototyping technology can produce prototype parts in just a few hours to dozens of hours, much faster than traditional methods, making it ideal for new product development and management.
2. Integration of design and manufacturing
The backward CAPP has always been a difficult obstacle to achieving the integration of design and manufacturing. However, for rapid prototyping, due to the use of discrete stacking processing technology, CAPP is no longer a difficult point. CAD and CAM work well together.
3. Free-form manufacturing
Freedom has two meanings: one is enabling free formation without special tools, shortening trial production time for new products; the other is being unrestricted by the part’s complexity.
4. Highly flexible
You can produce part models with different shapes by simply changing the CAD model and re-adjusting and setting the parameters.
5. Extensiveness of materials
Rapid prototyping technology can produce prototypes in resin, plastic, paper, paraffin, composite materials, as well as metal and ceramic.
6. High degree of technology integration
RP technology is a comprehensive integration of computers, computer technology, numerical control technology, data, lasers, materials, and machinery. Only with advanced laser devices and power control technology can rapid prototyping showcase its unique characteristics today.
7. Processing characteristics
Rapid prototyping technology breaks the traditional “blank → cutting → finished product” process, enabling tool-free part manufacturing through thin layer superposition. Compared with traditional cutting processing methods, rapid prototyping has the following advantages:
(1)It can quickly manufacture complex parts with free-form surfaces, grooves, shoulders, and hollows The complexity of the parts and the production batch have little to do with the manufacturing cost. It greatly reduces the development cost and development cycle of new products.
(2) It is a non-contact process that eliminates the need for tools, fixtures, tool wear, and cutting force.
(3) No vibration, noise, and cutting waste;
(4) The production team can achieve fully automated production at night;
(5) High processing efficiency, capable of quickly producing product solid models and molds.
Application of Rapid Prototyping Manufacturing Technology
Over the past decade, various industries have applied RP technology and demonstrated its superiority. This technology is used in manufacturing sectors like machinery, automobiles, aerospace, and electronics, as well as in medical, art, and architecture industries.
1. Rapid mold manufacturing
Rapid tooling (RT) using rapid prototyping technology is mainly applied to make casting and plastic mol. The molding process can be divided into two methods: indirect molding and direct molding.
(1) Indirect molding
Indirect molding is a molding method that combines RP technology with traditional molding technology to make part prototypes. Compared with CNC machining, RPM technology can design and manufacture various complex prototypes faster and better. Using rapid prototyping samples for traditional mold manufacturing can cut costs and cycles by half. Indirect molding technology has matured and is widely adopted.
(2) Direct molding
Direct molding is to use RPM technology to directly manufacture molds. It does not require the production of prototypes and is a completely different method from traditional molding processes. Using this method to directly manufacture metal molds is a more promising rapid mold manufacturing method. For example, the American DTM company has successfully developed a technology for manufacturing metal injection molds.
This technology uses selective laser sintering (SLS) to sinter resin-coated steel particles into a semi-finished mold, which is then post-processed with copper infiltration to create a steel-copper alloy injection mold. Its dimensional accuracy is ±0.12mm/100mm, Ra<lμm, and its service life can reach 50,000 pieces.
Table 2 Comparison between indirect molding and direct molding
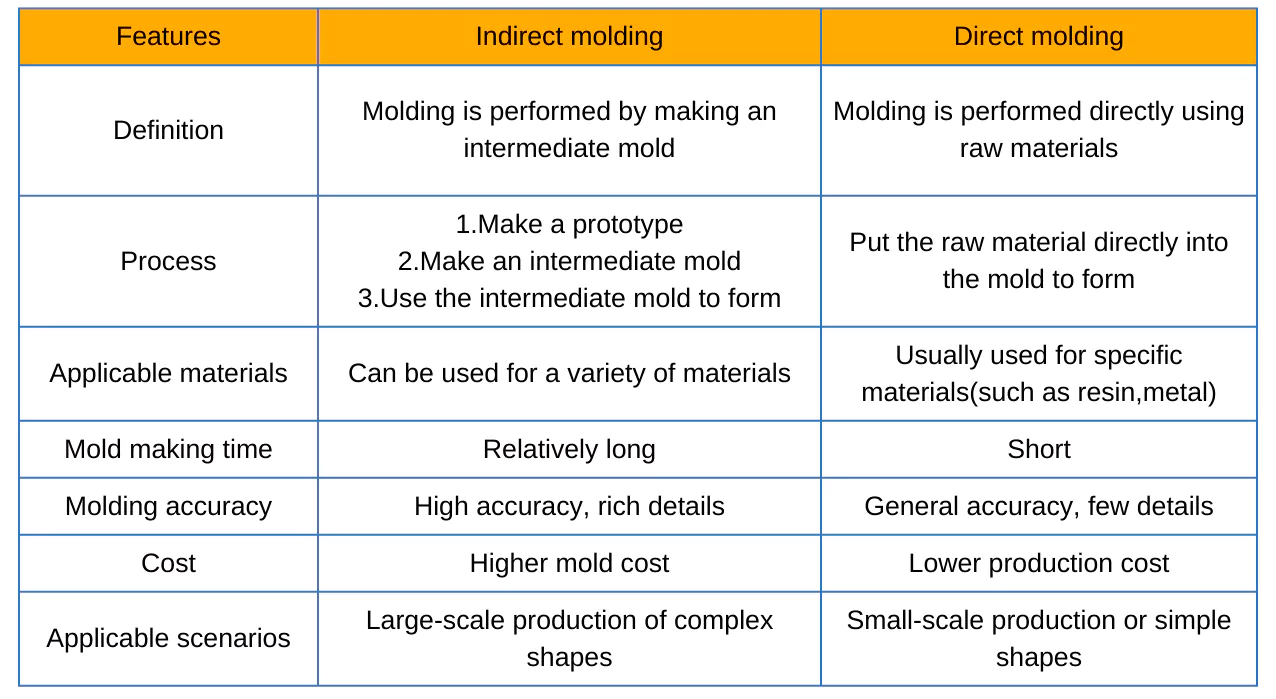
2. Rapidly manufacture metal parts
The combination of RP technology and casting technology is the best way to transform rapid prototyping prototypes into metal parts. The methods include reproducing the mold with RP prototypes, directly copying the mold, using lost-wax casting, or designing the model to directly obtain the shell and core.
Using the RP prototype to obtain the lost mold casting investment pattern is a faster precision casting method. 3D-Systems of the United States has developed Quickcast rapid precision casting technology using this method. YCoat the SLA prototype with refractory materials, bur, and gasify the resin to create a casting shell for metal casting. The key is using light-cured resin with low gas emissions and complete combustion. Ford Motor Company of the United States uses this technology to manufacture automobile molds.
3. Accelerate new product development
In the design stage of new product development, designers rely on design drawings and simulations, but lack prototypes, making quick judgments difficult. RP technology can create 3D prototypes from CAD models within hours or days without other processing methods.
Designers can evaluate, simulate, and test the prototype for appearance, assembly, and production feasibility, while quickly obtaining user feedback. In this way, the design stage can solve possible problems, significantly reducing the cost and time of new product development.
4. Used in medicine to make organ models
Many countries emphasize RP technology in medicine, achieving good results. By combining CT and MRI diagnostic methods with digital imaging, the RP system uses 3D reconstruction data from cross-sectional body scans to create prototypes of organs or body parts. The part’s lesion and entity structure can be displayed, aiding in clinical auxiliary diagnosis, determining complex surgical plans, or teaching.
5. Combined with reverse engineering to form a rapid design and manufacturing closed-loop system
In RP technology, reverse engineering is to find a three-dimensional CAD model based on the existing physical object. For most products, their three-dimensional models can be designed on general CAD software. Due to factors like function, process, and appearance, some parts have complex shapes, making it difficult to design solid models in CAD. We first create a small-scale physical model and then generate a 3D solid model by measuring and processing the data.
Common measurement methods in reverse engineering include three-coordinate measuring, laser triangulation, MRI, CT scanning, grating, and automatic intermittent scanning. Through reverse engineering, RP prototypes can also be measured quickly and accurately, and deficiencies in product design can be found. Redesign, after repeated iterations, can make the product more perfect. The introduction of reverse engineering in RP technology has created a closed-loop system for rapid design, manufacturing, and testing.
Conclusion
Rapid prototyping technology is a high-tech technology in the process of development and improvement. The technology itself and its application fields still need a lot of development and research. The 21st century will be an era characterized by a knowledge economy and information society. The manufacturing industry faces severe challenges in the changing market of small batches and multiple product varieties. As the industry globalizes, shortening product development cycles and reducing new product investment risks are key to enterprise survival. Rapid prototyping, molding, and manufacturing technologies will continue to be further developed.
What technologies do you use for rapid prototyping?
- CNC Machining
- Vacuum Casting
- Sheet Metal Fabrication
- 3D Printing (FDM, SLA, SLS, etc.)
This allows us to cater to a range of material and design requirements.
What industries do you serve?
We provide rapid prototyping services for industries such as:
- Automotive
- Aerospace
- Consumer Electronics
- Medical Devices
- Industrial Equipment
- Product Design and Development
Other fields.
What materials are available for prototyping?
We work with a wide range of materials, including plastics (ABS, PC, Nylon, etc), metals (aluminum, stainless steel, brass, etc), and other specialized materials. Let us know your requirements, and we’ll recommend the best material for your project.
What is the typical turnaround time for a prototype?
Turnaround times depend on the complexity and size of the project. Most prototypes are delivered within 3–7 business days. We also offer expedited services for urgent projects.
Can you provide design assistance or recommendations?
Yes! Our team of experts can help optimize your design for manufacturability, suggest suitable materials, and ensure that your prototype meets functional and aesthetic requirements.
Do you offer small-batch production in addition to prototyping?
Absolutely. We can transition from prototyping to small-batch production seamlessly. This is ideal for market testing or limited runs before full-scale manufacturing.
How do you ensure the quality of prototypes?
We follow strict quality control measures at every stage, from material selection to final inspection. Advanced machinery and skilled technicians ensure precision and high-quality results.