Traditional milling process optimization mainly relies on experience and trial and error, this method is not only time-consuming and laborious, but also difficult to achieve the best results.
In this paper, we systematically study the basic theory of CNC milling process, common problems, and put forward a set of comprehensive optimization scheme, in order to provide reference for the optimization of CNC milling process.
CNC milling process basis
The milling process is a method of using a rotating multi-flute tool for cutting and processing a workpiece.
The process mainly involves the rotary movement of the tool and the feed movement of the workpiece. This allows the cutting edge of the tool to contact the surface of the workpiece.
The tool then removes excess material to achieve the desired shape and size. The milling process has the following characteristics.
(1) the use of multi-flute tools, cutting speed, high production efficiency;
(2) milling can process plane, slot, hole, surface and other complex geometric shapes;
(3) milling process cutting force distribution is uniform, is conducive to improving the machining accuracy and surface quality;
(4) the processing effect can be flexibly controlled by adjusting the cutting parameters (such as cutting speed, feed rate, depth of cut, etc.) to adapt to the different materials and processing requirements.
Key factors for optimisation of milling process
1. Tool selection and optimal design
The key factor to improve the efficiency of milling process and machining quality is tool selection and optimal design.
According to the workpiece material and machining requirements such as high-speed steel, carbide or ceramics, choose the appropriate tool material to ensure that the tool hardness is sufficient and wear resistance is good.
To optimise the cutting performance and reduce the cutting force, choose the appropriate tool geometry parameters, including the front angle, back angle, camber angle and helix angle.
Although a larger front angle can reduce the cutting force and cutting heat, the strength of the tool will be reduced; a smaller back angle has a great improvement on the durability of the tool, but the friction will be increased.
The coating process, such as TiN, TiAlN, etc., is used to improve the heat and wear resistance of the tool.
During the cutting process, the tool is optimally designed by finite element analysis and simulation software to simulate the stress and temperature distribution, thus ensuring optimum performance in actual machining.
2. Setting and Adjustment of Cutting Parameters
The setting and adjustment of cutting parameters aim to determine the initial parameters. These include cutting speed, feed rate, and depth of cut. Experimental and empirical data are used for this determination.
The goal is to search for the optimal combinations.
This is done with the help of mathematical models and optimization algorithms. Examples of these algorithms include the Genetic Algorithm and Particle Swarm Optimization Algorithm.
Among them, the cutting speed needs to take into account the matching relationship between the tool and the workpiece material, too high cutting speed will lead to tool overheating, wear and tear, too low cutting speed will reduce productivity;
Feed rate needs to take into account the quality of the surface of the workpiece and productivity, too high a feed rate will increase the surface roughness, too low a feed rate may affect the machining efficiency;
Depth of cut needs to be combined with the rigidity of the machine tool and the strength of the workpiece material to determine the cutting depth, the cutting depth is the most important parameter of the machine tool.
It also depends on the strength of the workpiece material. If the depth of cut is too large, it will increase the cutting force and vibration. If the depth is too small, it may lead to cutting instability.
In addition, cutting force sensors and temperature sensors can be deployed. These sensors allow for real-time monitoring of the milling process.
They track changes in cutting force and temperature data. Based on this data feedback, the parameter settings can be further optimized.
3. Optimization of cooling and lubrication technology
To improve milling process efficiency and machining quality, the appropriate coolant should be selected.
The choice of coolant depends on the workpiece material and machining requirements. Options include water-based emulsion, oil-based coolant, or synthetic coolant.
The coolant supply method should be optimized. High-pressure cooling and internal cooling technology should be adopted.
This ensures that the coolant reaches the cutting zone directly. It also helps to effectively remove heat generated during cutting. As a result, the temperature of both the tool and workpiece will be reduced.
At the same time, suitable lubricants and lubrication methods should be used. Options include oil mist lubrication, spray lubrication, or minimal lubrication.
These methods reduce friction between the tool and the workpiece. As a result, tool life is prolonged, and surface quality and machining accuracy are improved.
Through the monitoring and control of coolant flow and pressure, the cooling and lubrication system is ensured to be stable and effective.
Such as the use of flow meters, pressure sensors for real-time monitoring of the status of the coolant, timely adjustment of the system parameters and so on.
Regular maintenance of the cooling and lubrication system, cleaning of filters, pipelines, etc., to prevent blockage and pollution, to ensure that the system works reliably for a long time.
4. Machining path planning and simulation analysis
Machining path planning and simulation analysis is an important means to improve the efficiency of the milling process and machining quality, the specific method shown in Figure 1.

(1) Initial path design:
Use CAM software (such as MasterCAM, UGNX, etc.) to generate the initial machining path according to the geometry of the workpiece and machining requirements.
In the path design should take into account the continuity and reasonableness of the tool path, and avoid lifting and lowering operations on unnecessary tools.
(2) Optimization path algorithm:
Optimise the initial path to reduce the empty travel of the tool and the machining time by applying optimization algorithms (e.g. genetic algorithm, particle swarm optimization algorithm, etc.).
Optimization objectives include minimising the path length of the tool, reducing the number of tool redirections, and avoiding mutual interference between the tool and the workpiece.
(3) Virtual machining simulation:
For the optimised machining path, simulation software (such as VERICUT, SIMUFACT, etc.) is used to carry out virtual machining simulation to verify the feasibility and reasonableness of the path.
The interaction between the tool and the workpiece can be observed in the simulation process, and potential collision and interference problems can be detected.
(4) Cutting force and cutting temperature simulation:
Finite element analysis software, such as ANSYS or ABAQUS, can be used to simulate the cutting force and temperature during the cutting and machining process.
This helps assess the force and thermal deformation of the tool and workpiece. Based on the results, the cutting parameters and cooling strategy can be optimized.
(5) Surface quality and machining efficiency assessment:
The simulation results of the machined surface quality and machining efficiency are analysed to assess the effect of the optimization path.
According to the simulation results to further adjust the path, parameters, until the processing effect reaches the best.
5. Optimise the dynamic performance and stability
of the machine tool The dynamic performance and stability of the machine tool directly affects the machining accuracy and efficiency of the milling process, which is an important part of improving the overall process level.
To optimize the dynamic performance of the machine tool, dynamic characteristic analysis must be carried out.
Vibration testing and modal analysis are used to determine the machine’s intrinsic frequency, damping characteristics, and weak points in rigidity.
Based on these findings, structural improvements or reinforcement of key parts can be made to enhance vibration resistance.
By optimizing the transmission system and servo control parameters of the machine tool, the dynamic error and transmission inertia can be reduced, and the response speed and accuracy of the motion can be improved.
To suppress vibration during machining, adaptive control technology can be introduced. This technology dynamically adjusts cutting parameters.
The adjustments are based on real-time monitoring of cutting force, vibration signals, and other data. The goal is to achieve vibration control and stable machining.
The eccentric vibration caused by rotational inertia can be reduced by high-precision spindle dynamic balancing technology, which further enhances the operational stability of the machine tool.
In practical applications, finite element analysis can be used to carry out dynamic simulations of the machine tool’s overall structure. This helps identify and improve structural weak points.
Additionally, damping materials, dampers, and other vibration-damping measures can be used. These measures enhance the stability and reliability of the machine tool during the machining process.
Milling Process Optimization Based on Intelligent Technology
1. Data Acquisition and Analysis in CNC Machining
Data acquisition and analysis is a key step in achieving intelligent optimization.
In the data acquisition phase, various sensors need to be deployed. These include cutting force sensors, temperature sensors, vibration sensors, and displacement sensors.
The sensors should be placed in key parts of the machine tool, such as the spindle, tool, and workpiece clamping system.
These sensors enable real-time monitoring of various parameters during the machining process.
The data collected by the sensors is transmitted to the central processing system using data acquisition cards and data loggers.
The data acquisition system ensures that the data is accurate and complete with high sampling rate and high resolution.
The data is transmitted to a central server or cloud platform for centralised management and storage via wired or wireless networks (e.g. Ethernet, Wi-Fi, Industrial Ethernet, etc.).
In the data analysis stage, the collected raw data need to be pre-processed, including data cleaning, filtering and normalisation to remove noise and outliers to ensure reliable and consistent data.
Signal processing techniques (e.g. Fourier Transform, Wavelet Transform) such as cutting force peaks, temperature trends, vibration frequency and amplitude, etc. are used to extract characteristic parameters from the data.
Parameter changes during machining are evaluated, and potential problems and anomalies are identified through statistical analysis methods (e.g. mean, standard deviation, correlation analysis).
2. Artificial Intelligence-based Process Optimization Methods
The efficiency and quality of the milling process is improved through artificial intelligence algorithms and models, and the specific optimization methods are shown in Figure 2.

(1) Data-driven parameter optimization:
Through historical data training and global search, machine learning techniques can be used. Examples include support vector machines, random forests, and neural networks.
Genetic algorithms are also employed to construct and optimize the cutting parameter model. This helps discover the optimal parameter combinations, improving machining quality and efficiency.
(2) Real-time monitoring and adaptive control:
Through adaptive control algorithms (fuzzy logic, neural network), the use of sensors to collect data in real time, and dynamically adjust the cutting parameters to ensure machining stability and optimal performance.
(3) Fault prediction and diagnosis:
Use machine learning techniques, such as isolated forests and self-coders, to detect abnormal data.
Apply fault diagnosis algorithms like Bayesian networks and decision trees. Combine this with expert knowledge and historical data.
This helps determine the cause of the fault. Based on the analysis, solutions can then be proposed.
(4) Optimise path planning:
Use path optimization algorithms, such as the Ant Colony Algorithm and Particle Swarm Optimization Algorithm, to optimize the machining path. This helps reduce empty travel and machining time.
The feasibility and reasonableness of the path are then verified through simulation software. Examples of such software include VERICUT and Simufact.
Experimental analysis
1. Experimental design
To verify the effectiveness of the optimization method, typical workpieces are selected. These include 6061-T6 aluminium alloy, 304 stainless steel, and 45# carbon steel workpieces.
Different combinations of cutting parameters are set up. Cutting force, temperature, and vibration data are collected in real time. Sensors are used to gather this data.
The machining quality and efficiency were evaluated before and after optimization.
The test results were verified by statistical analysis and simulation software to ensure the reliability and effectiveness of the optimization method.
2. Test conditions and evaluation indexes
The test conditions are set in a standard workshop environment, with a temperature of 20-25 ℃ and a humidity of 40%-60%;
The cutting parameters include cutting speed, feed rate and depth of cut, and several different combinations of parameters are set;
The evaluation indexes include surface roughness, machining time, cutting force, tool wear and vibration amplitude;
And the test data before and after the optimization are compared to assess the machining quality and efficiency.
3. Analysis of the test results
The optimised combination of cutting parameters significantly improved the machining quality and efficiency, as shown in Table 1.
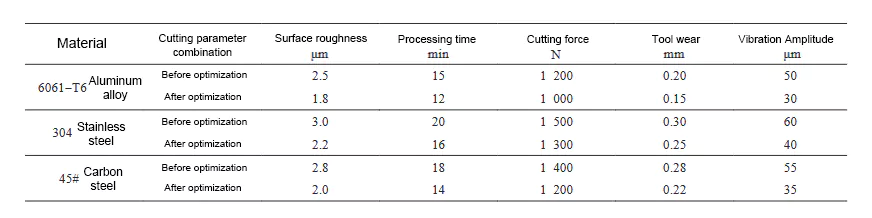
For 6061-T6 aluminium alloy, the surface roughness was reduced. It decreased from 2.5 μm to 1.8 μm. The machining time was also reduced, from 15 minutes to 12 minutes. The cutting force dropped from 1,200 N to 1,000 N.
Tool wear decreased from 0.20 mm to 0.15 mm. The vibration amplitude was reduced, from 50 μm to 30 μm.
Similarly, the surface roughness, machining time, cutting force, and vibration amplitude were reduced in the optimized test data for 304 stainless steel and 45# carbon steel.
The surface roughness decreased from 1.5 μm. The cutting force dropped to 1,000 N. The vibration amplitude was reduced from 50 μm to 30 μm.
Similarly, 304 stainless steel and 45# carbon steel showed significant improvements in surface roughness, machining time, cutting force, tool wear and vibration amplitude after optimization.
These results validate the effectiveness of the optimization method and significantly improve the machining quality and efficiency.
Conclusion
The optimization of milling process in CNC metal machining is the key to improve machining efficiency and quality.
Reasonable selection of tools and optimization of cutting parameters make vibration, overheating, tool wear and other problems effectively improved;
The improvement of cooling and lubrication technology, machining path planning and the application of simulation analysis further improve process stability and accuracy.
In the future, the deep integration of intelligence and automation can be further explored to continuously optimise the machining process.