Rapid prototyping technology (RP technology) combines materials, laser, mechanical engineering, CNC, and CAD technologies.
It allows for the accurate, automatic, and quick manufacturing of molds or parts directly from CAD models, bypassing the need for costly machining, tool design, and mold creation.
This technology significantly shortens product development cycles, enhancing manufacturing flexibility and production efficiency.
In the machinery industry, manufacturers commonly use machining methods to produce presses, molds, core boxes, and templates.
Skilled fitters often trim parts, especially complex, thin-walled castings like automobile cylinder blocks, aircraft engine blades, cylinder heads, and marine propellers.
The integration of rapid prototyping and casting technologies offers great potential for quickly producing small batches and single-piece molds or parts.
This article explores the combined use of rapid prototyping and casting technologies for integrated manufacturing.
Typical rapid prototyping technologies
At present, 3DP, SL, SLS, FDM, LOM, and other technologies are rapid prototyping processes with relatively mature applications in the world.
We can divide these processes into two categories: the digital jet-forming process based on microdroplets and the rapid prototyping process based on lasers.
The digital jet-forming process using microdroplets involves creating adhesive or material droplets through microdroplet technology.
In contrast, the laser-based rapid prototyping process employs laser technology to bond, separate, solidify, and melt formable materials.
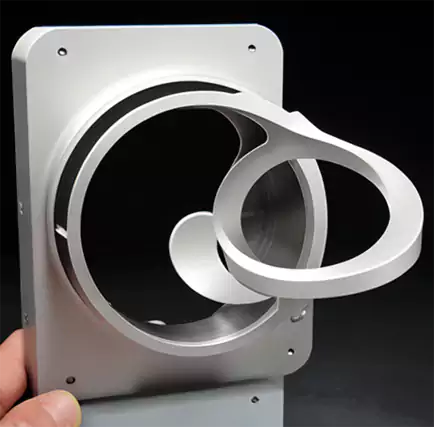
1. Typical laser rapid prototyping processes
(1)DLF process: The DLF process forms metal by selectively sintering powder with a high-energy laser.
(2)SL process: The SL process uses ultraviolet light or laser to cure resin and stack it into shape.
(3)SGC process: The SGC process cures resin with an ultraviolet laser, using mask technology to shape it.
(4)LENS process: The LENS process sinters metal powder layer by layer using a high-energy laser for sintering.
(5)LOM process: The LOM process cuts and sinters metal sheets or paper layers to form a shape.
(6)SLS process: The SLS process uses a CO2 laser to sinter various powders layer by layer into shape.
2. Typical micro-droplet digital jet-forming processes
(1)3DP process: The 3DP process sprays binder to bond powder, forming a shape layer by layer.
(2)EFF process: The EFF process adjusts material ratios and uses micro-droplet technology to form gradient parts.
(3)SDM process: The SDM process combines molten metal droplets with cutting to form metal molds directly.
(4)PCM process: The PCM process sprays binder on sand to bond mold sand and create a shape.
(5)3DW process: The 3DW process uses surfacing principles to stack metal wires.
(6)MJS process: The MJS process extrudes molten material to form a wire pile with continuous droplets.
(7)BPM process: The BPM process sprays molten material from a nozzle to form a pile with five-axis freedom.
(8)UDS process: The UDS process uses electromagnetic control to form a pile of molten materials.
(9)FDM process: The FDM process heats materials in a nozzle and sprays droplets to form a wire pile.
(10)CC process: The CC process combines molten casting and contour accumulation to form a pile.
RP and Casting Process Integration
The integration of Rapid Prototyping (RP) technology and the casting process enables the rapid production of parts and molds.
This integration combines casting technology, CAD technology, RP technology, CAE technology, CAM technology, and others.
It enables CAD models to convert into physical models quickly, effectively reducing production costs and manufacturing cycles.
One significant factor influencing the dimensional accuracy of the molds and parts produced by this process is the shrinkage rate of the metal during casting.
To achieve greater accuracy in the formed metal mold or part, it is crucial to precisely determine the shrinkage rate of the metal.
This paper conducts a numerical analysis of the casting solidification process and optimizes the casting process parameters to ensure that the dimensional accuracy of the parts or molds meets technical requirements.
Current Research and Challenges
In China, most of the numerical simulation work on the casting solidification process primarily focuses on analyzing the casting stress field, casting temperature field, and predicting defects such as hot cracking, shrinkage, and shrinkage cavities during the solidification process.
However, researchers have limited their studies on the numerical simulation of the dimensional accuracy of castings during solidification.
During casting solidification, the casting stress field and casting temperature field interact. The analysis of the casting solidification process is a typical example of thermal coupling.
Previous studies have often simplified thermal coupling by neglecting the temperature changes caused by stress deformation work, shortening the calculation time for coupling analysis.
While this simplification does not affect the analysis of casting stress, temperature fields, or the prediction of defects, it can impact the accuracy of the mold dimensions.
Optimizing Dimensional Accuracy
By integrating finite element simulation technology with CAD data, we can simulate the solidification process of the mold or part to predict dimensional changes during solidification.
This method enables us to optimize the CAD model, compensating for dimensional errors that may occur during processes like precision casting and RP prototyping.
Furthermore, the technology facilitates error compensation and feedback during the 3D CAD modeling process.
This approach can also integrate material technology, laser technology, finite element simulation, RP, and CAD technologies to quickly manufacture metal molds and parts.
Real-Time CAD Model Modification
Since prototype forming is computer-controlled, computer technology manages both the design and production processes, enabling the rapid manufacturing of high-quality prototype parts.
Unlike traditional manufacturing processes, the integration of rapid prototyping and casting technology allows for real-time adjustments to the CAD model.
This helps address issues like dimensional shrinkage, accuracy control, and geometric deformation.This ensures that the parts and molds produced are of the highest quality.
Direct Manufacturing of Metal Parts/Molds from CAD Models
CAD can directly drive the manufacturing of metal molds without the need for traditional core boxes or patterns.
The casting workshops of various manufacturing companies commonly use shell molding materials. The part model can convert directly into a mold within the CAD environment.
Non-part components may require bonding or sintering during the forming process, while parts stay in powder form throughout.
After forming, we remove the powder, and then directly manufacture the sand mold and core.
This approach eliminates the need for large quantities of foam plastic molds or wax molds used in traditional precision casting. It significantly saves time and costs, especially for producing complex parts in small batches. The main processes currently include:
Direct Shell Casting (DSPC)
SLS Sand Mold Sintering
PCM Woodless Mold Forming Process
These methods enable the integrated manufacturing of sand cores and molds, with no assembly required between sand cores and molds. This is particularly beneficial for producing complex parts in small batches.
Manufacturing Metal Parts/Molds Indirectly Driven by CAD Models
1.Process Flow for Indirect Manufacturing
The indirect manufacturing process starts with the design of a 3D CAD model for the metal mold or part, including the design of risers and gates. This helps simulate the metal solidification process and shrinkage.
We use MARC software to simulate the solidification process, optimize process parameters, and determine the metal shrinkage. This approach ensures that we track dimensional accuracy in real time during solidification.
After optimizing the CAD model, we use it to drive the production of the necessary casting pattern and rapid prototype.
2.Integration of RP and Casting for Low-Cost Manufacturing
By combining casting technology and rapid prototyping technology, low-cost and rapid manufacturing of small batches of metal parts becomes possible.
We can use processes such as BMP, FDM, SGC, and SLS to manufacture wax mold prototypes, which can then be applied to investment casting. For example:
We can use FDM prototypes to quickly produce metal molds or parts.
In traditional investment casting, we substitute wax molds with FDM prototypes.
We apply a refractory slurry to the FDM mold, and once it solidifies, we remove the FDM prototype, leaving behind only the casting shell for the process.
This approach is especially useful for producing small to medium-sized metal parts of moderate complexity.
Combining RP and Casting for High-Strength Metal Parts
We can also integrate RP technology with other casting processes such as ceramic mold casting, gypsum mold casting, and sand mold casting.
This combination results in metal parts with high mechanical strength, high hardness, low deformation, and low internal stress. The resulting prototypes exhibit high durability, making them suitable for various industrial applications.

Conclusion
In short, the integrated forming and manufacturing of rapid prototyping and casting technology can maximize the advantages of casting technology and rapid prototyping technology, can pre-eliminate defects, has low cost and fast manufacturing speed, and can quickly manufacture complex parts, which is worthy of promotion and application.