Table of Contents
CNC (Computer Numerical Control) turning machining is widely used across many industries due to its high precision, excellent efficiency, and adaptability. It is particularly advantageous for producing small-lot, diversified, and complex structural parts. Below are the main features of CNC turning machining services.

Strong Adaptability
Adaptability, also known as flexibility, refers to the ability of CNC machine tools to respond to different production requirements and part characteristics. In traditional machining, changing parts or processes often requires adjusting the mechanical structure or reconfiguring the equipment. However, in CNC turning, when the part or process changes, the operator simply rewrites and enters a new CNC program. There’s no need for hardware changes, and the machine can continue processing the new parts.
This ability makes CNC turning particularly advantageous for small, diverse, and complex part production. CNC turning can achieve single-piece customization and efficiently complete small-batch production. It provides quick responses for trial production, sample manufacturing, and product improvements. Its adaptability is the core reason for CNC turning’s rapid growth in the global manufacturing industry.
High Precision and Stable Processing Quality
CNC turning is known for its high precision and stability. The CNC lathe controls all processing actions with digital commands, minimizing operator intervention and reducing human error. Modern CNC lathes incorporate technologies such as precision guideways, rigid machine structures, and high-performance servo motor systems to improve accuracy and rigidity.
CNC lathes can move the table with accuracy as fine as 0.01mm or better. Many high-end lathes use scales to control tiny table displacements, enhancing machining accuracy. The CNC system automatically adjusts feed transmission chain gaps and pitch errors, maintaining optimal machining accuracy.
By the 1990s, CNC lathes reached positioning accuracy of ±0.002mm to ±0.005mm, improving product consistency and batch production stability. The drive system’s high rigidity and thermal stability ensure steady machining accuracy, even under long operating times and heavy loads. Thus, CNC turning guarantees both part consistency and high qualification rates while enhancing production reliability and stability.
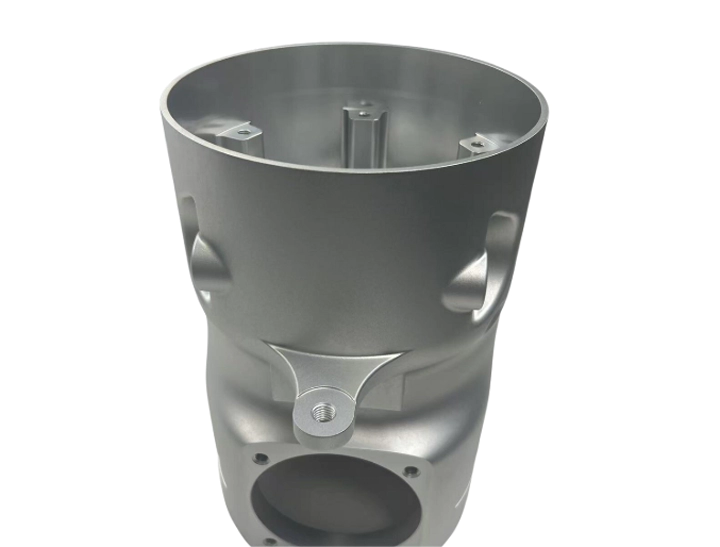
Improved Production Efficiency
CNC turning improves both precision and production efficiency. Traditional machine tools’ processing time consists of manipulation and auxiliary time. CNC lathes offer a wide range of spindle and feed speeds, enabling each machining process to use the best cutting parameters, increasing cutting efficiency and reducing processing time.
Thanks to CNC machine tools’ high rigidity, they can perform powerful cutting with large cutting volumes, further boosting cutting efficiency. Compared to traditional machines, CNC lathes cut faster, respond quicker, and reduce clamping time. Automatic tool changes minimize manual intervention and save additional time.
Furthermore, the high automation level of CNC lathes eliminates the need for machine re-adjustment during part replacement, saving installation and adjustment time. CNC lathes also ensure high consistency in machining quality during part checks and critical dimensional sampling, reducing downtime for inspections.
Modern CNC lathes use machining center technology, allowing one machine to perform multiple machining processes simultaneously. A CNC lathe can complete turning, milling, drilling, tapping, and more, significantly improving productivity while reducing tool changeover time and labor costs.
Reduced Manual Operation and Improved Safety
CNC turning has a high degree of automation, with most operations controlled by computers, minimizing the need for manual intervention. Traditional machine tool operations often lead to errors or accidents, but CNC lathe’s high-precision control and automation help prevent these problems.
CNC lathes also improve safety during machining. The operator only needs to set up and monitor the machine, reducing the need for long, intense operations. This lowers labor intensity and minimizes safety risks.
Summary
CNC turning machining has become an indispensable technology in modern manufacturing. Its excellent adaptability, high precision, stability, and efficiency make it ideal for high-precision machining of complex parts. CNC turning also enables quick responses to changing production environments, boosts productivity, and ensures stable processing quality.