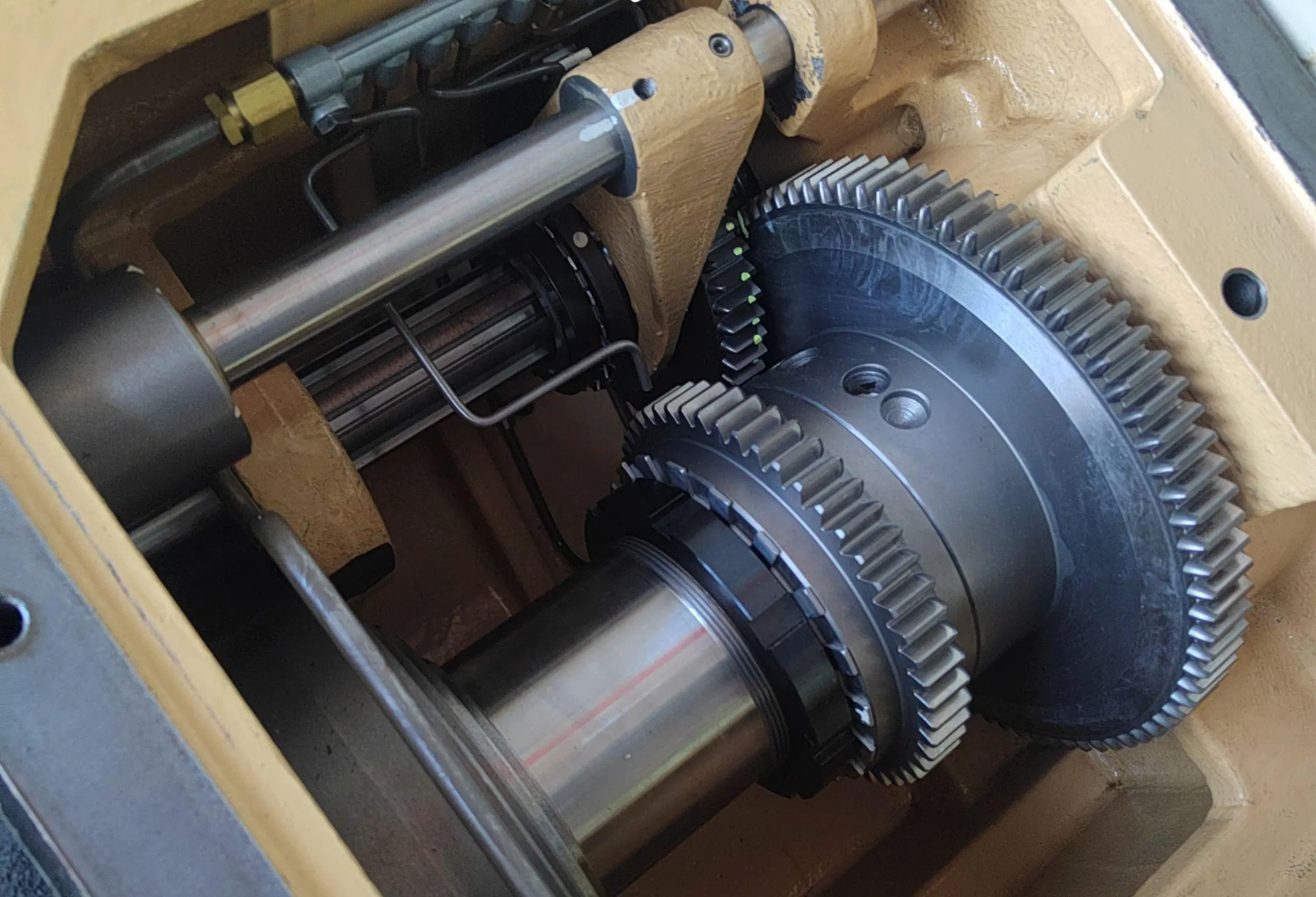
Mold Making Process
Generally speaking, mold production is a complicated process. RY divides mold making into 12 steps.

Drawings Receiving


DFM Check


Materials Preparation


EDM Machining


Wirecut Machining


CNC Machining


Mold Fitting


Core Fitting


Mold Polishing


Mold Fabrication


Mold Trial


Customer Confirm
