Precision molds have the advantages of high manufacturing accuracy and high efficiency, and are widely used in many fields.
With the continuous development of manufacturing technology, the demand for precision molds is also expanding and upgrading.
Precision mold research began in the early 20th century, so far there has been great progress and development.
Many scholars for precision mold manufacturing technology and application direction have different research and exploration.
Japan, Germany and other countries in the manufacture and application of precision molds in the leading level.
Japanese manufacturing enterprises introduced foreign CNC processing technology. This led to the development of a series of high-precision, high-efficiency precision mold products.
These molds were successfully applied in automotive, electronic products, aerospace, and other fields.
Germany’s precision mold enterprises are focusing on researching new materials and new processing technologies, and have made important progress in high-speed cutting, optical imaging and other aspects.
Overview of precision mold
Definition of precision mold
Precision mold is to manufacture products for the purpose of CNC processing and other ways of processing out for forming, punching or other processing processes directly on the raw material (usually metal or plastic) tools.
Precision molds have characteristics like high accuracy, high repeatability, and long life. Their manufacturing process relies on advanced cutting technology.
It also involves traditional heat treatment, EDM, ultra-precision machining, and other process methods.
Composition structure of precision mold
The composition of precision mold mainly includes mold frame, mold base, upper template, lower template, positioning pins, guide columns, slider, feeder and switch and other parts.
Among them, the mold frame supports all other parts; the mold seat is related to the disassembly, installation and debugging of the mold;
The upper and lower mold plates are responsible for die casting or pressure forming, which is often carried out in different ways using self-release patterns and with lifting mechanisms, respectively;
Positioning pins and guide columns provide functions such as precise positioning, stable guidance and reliable separation; the functions of sliders and dropouts are related to specific mold applications and requirements;
And the switches are related to the processing environment and operation mode. The large nozzle mold base (also known as single parting surface mold holder) is shown in Figure 1.
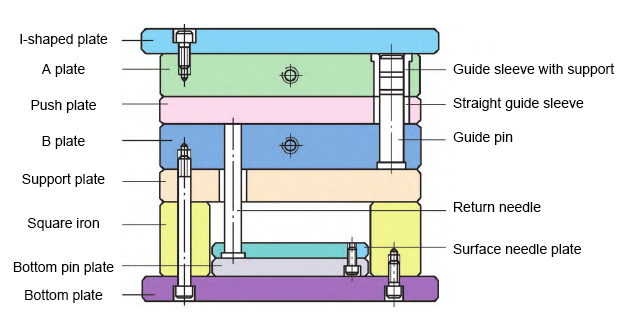
Classification of precision mold
According to the use of classification
Mainly divided into die-casting molds, stamping molds, injection molds, rubber molds, foam molds, casting molds and shear molds and other types.
According to the processing mode classification
Mainly divided into clamp machining, CNC machining, EDM, general-purpose machining and ultra-precision machining and other types.
Classified by manufacturing materials
Mainly divided into imported steel, high-quality carbon steel, alloy steel, special steel, seamless steel pipe, aluminum alloy, cemented carbide, ceramic or non-metallic and other types.
The characteristics of precision mold
High precision
Precision mold manufacturing accuracy can reach submicron level or higher.
This is because the level of manufacturing accuracy depends largely on factors such as processing technology and the physical properties of the material.
High Repeatability
Precision molds have good sustainability. After the same process, to ensure that the accuracy and quality of each finished product is the same.
Long life
After reasonable design and manufacture, precision molds can often be used for many years or even decades without obvious loss or damage.
Application scope of precision mold
Precision molds are widely used in automobiles, electronic products, aerospace, medical devices, home appliances, machinery manufacturing and steel and other fields.
In these fields, precision molds can be used in various processing techniques.
These include die-casting molding, injection molding, stretch molding, precision cutting, die-cutting, and casting molding. These methods produce a variety of complex shapes and high-quality products.
Examples include automotive engine blocks, guide rails, chip packages, consumer electronics shells, medical equipment parts, and high-speed train brake discs.
Precision mold manufacturing problems and solutions
Processing accuracy and stability to be improved
At present, precision mold manufacturing there are some technical bottlenecks and difficulties, processing accuracy and stability to be further improved.
In order to solve this problem, we can further combine hardware and software, improve the precision and accuracy of processing and testing equipment, improve the control of the entire manufacturing process and quality inspection links.
Lack of systematic management
Due to the complexity of precision mold production, the process often involves design, processing, testing, and other aspects.
As a result, issues such as information disconnection and poor communication can easily arise during production.
To solve these problems, we can try to introduce advanced ERP, MES and other information management systems to achieve systematic management of the whole process to ensure smooth collaboration between the various links.
Talent gap
Precision mold industry involves a number of disciplines, requires a high level of innovative talent support.
The current talent gap is large, there is an urgent need to cultivate high-quality professionals.
Enterprises should strengthen cooperation with institutions of higher learning and research institutions, and increase the training of talents.
Insufficient communication between design and process
There is a big difference between design and manufacturing, and designers lack the understanding of customer needs when communicating with customers, and cannot provide the necessary support when customers need it.
To avoid these issues, the design team should regularly assess the information exchange between technical and non-technical groups.
They should strengthen communication management and develop project progress plans.
Additionally, it is important to enhance the relevance of effective communication, responsibilities, and goals.
In summary, the precision mold manufacturing industry still faces many challenges during its development. It should address issues from various aspects, such as technology, management, and human resources.
The industry needs to explore solutions that fit its specific situation. By doing so, it can continuously improve core competitiveness and promote healthy, rapid development.
Development direction of precision mold manufacturing
The application of digital technology
Precision mold manufacturing process is gradually transforming to digital, digital modeling, visual simulation and intelligent manufacturing and other new technologies are widely used, can realize the design and processing of complex precision structure, improve production efficiency and product quality.
Intelligent manufacturing
With the rapid development of information technology, precision mold manufacturing has gradually realized intelligent production.
Through the introduction of Internet of Things, artificial intelligence, robotics and cloud computing and other technologies, it can realize the interconnection between equipment, real-time data collection and analysis, reduce the intermediate links in the transmission of information, accelerate the pace of production, improve production efficiency and product quality.
Application of new composite materials
In the future, new materials such as high-strength steel, aluminum alloy, magnesium alloy, ultra-high molecular weight polyethylene and carbon fiber will be widely used in the manufacture of precision molds to meet the growing customer demand.
Composite materials compared to traditional materials with higher strength, lightweight, corrosion and other advantages, and gradually become a popular material in the field of precision mold manufacturing.
In the future, with the development of composite materials technology, will give rise to more new precision mold materials, thus further promoting the development of the entire industry.
Accuracy and surface quality improvement
With the upgrading of market demand, precision is becoming an increasingly important indicator. At the same time, surface quality and antioxidant properties are also key competitive factors.
More and more manufacturers are requiring precision molds to be not only accurate and reliable but also visually appealing.
Application of lightweight technology
Since the quality of precision manufactured parts is less restricted, the application of lightweighting technology can be rapidly promoted to reduce manufacturing costs, while reducing quality and improving product performance.
Application of rapid prototyping technology
Traditional manufacturing methods often require a lot of time for design, processing and testing, etc., and the high cost limits the speed and efficiency of product development.
The emergence of rapid prototyping technology to effectively solve this problem, can achieve rapid, efficient and low-cost manufacturing of precision molds.
Specialized customization
With continuous changes in market demand, the design and manufacture of precision molds is gradually shifting toward personalization and specialization.
More companies are focusing on the research and development of customized precision molds. This helps them cope with the diversification of market demand.
High reliability and durability
In the automotive, electronic products and aerospace and other fields, for precision molds of high reliability and high durability requirements are increasing.
In the future, the precision mold manufacturing industry needs to pay more attention to the innovation of materials, processes and other aspects, to further improve product quality and competitiveness.
Precision mold manufacturing technology
In the advanced manufacturing industry, the technological development in the field of mold manufacturing affects product quality and production efficiency.
With the continuous development of manufacturing technology, precision mold manufacturing technology is also gradually improved and upgraded.
CNC processing technology
CNC machining technology is a digital high-precision processing method, which is widely used in the mold manufacturing process.
The advantage is that the virtual model on the computer can be directly converted into a real physical model, the size of the product produced is highly accurate and repeatable, which can reduce the occurrence of human error.
Currently common CNC machining equipment include CNC milling machines, CNC lathes and CNC EDM machines.
They use computer programs to operate. The data from the design drawings corresponds one-to-one with the motion trajectory values.
The tool head rotates at high speed for cutting. This process produces high-precision parts and molds.
Laser Processing Technology
Laser processing technology is a fast, efficient and flexible parts processing method that can process various complex shapes of molds.
The advantages of laser processing are high precision, high speed, and it is not easy to damage the structure of the surface of the parts during processing.
Laser processing technology mainly includes laser cutting, laser marking and laser welding.
Among them, laser cutting and laser marking are commonly used in the processing of metal plates, and laser welding is mainly used in mold repair and the manufacture of complex shaped parts.
Electrical Discharge Machining (EDM) Technology
Electrical Discharge Machining (EDM) is a processing technology. It uses continuously moving fine metal wires, known as electrode wires, as electrodes.
These wires carry out pulsed spark discharges on the workpiece. The discharges etch away metal, cutting and shaping the material.
EDM is widely used in the manufacture of high-precision molds and tool parts.
The advantage of EDM machining is that it is more advantageous for milling materials with higher hardness and brittle materials, such as reinforced steel and carbide.
In EDM, the distance between the electrode and the workpiece is controlled. A liquid medium is injected into the discharge hole, generating an electric spark.
This spark melts and evaporates the workpiece material locally, resulting in superb machining results.
Several precision mold manufacturing technologies introduced above have their own advantages and scope of application.
It is usually necessary to determine the most suitable processing method based on the requirements of the processing object. Additionally, the characteristics of the equipment, cost, and other factors should be considered comprehensively.
When analyzing and comparing these technologies, factors like processing time, precision requirements, applicable materials, and costs must be considered.
In actual production, the technology should be selected based on specific needs to achieve the best production results.
Automobile field
Precision molds are widely used in the field of automobile manufacturing, mainly including automobile interior and exterior parts forming, engine, transmission and other key components manufacturing.
In terms of automobile appearance, molds are used to produce body parts, door handles, side skirts, and more.
For key automotive components, molds are used to produce engine pistons, crankshafts, camshafts, transmission gears, clutch discs, and other core parts. Automotive structural parts molds are shown in Figure 2.

Currently, automobiles use more and more types of molds, and the difficulty of manufacturing continues to increase.
In order to avoid mistakes and reduce manufacturing difficulties, more manufacturers have begun to use mold manufacturing processes to ensure overall production efficiency.
Electronic products field
Precision molds play a crucial role in electronics manufacturing.
For example, they are used to produce key components like panels, chassis, and batteries for smartphones, tablet PCs, and other electronic products.
In addition, precision molds are also used in semiconductor component manufacturing and many other fields. Structural parts molds for electronic products are shown in Figure 3.
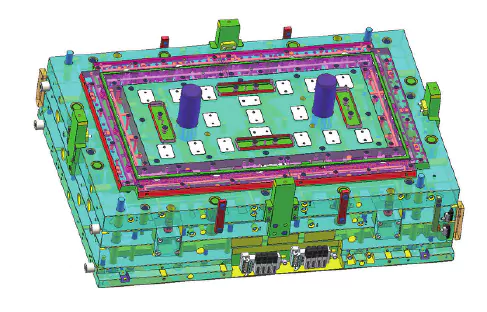
Medical equipment field
Precision molds are widely used in the field of medical devices, mainly used in artificial joints, dental equipment and surgical instruments.
This field has high requirements for the manufacturing quality and precision of the mold.
Through the use of precision molds, production efficiency can be improved, while ensuring the stability and consistency of medical product quality. Medical product molds are shown in Figure 4.

Other fields
In addition to the above fields, precision molds are widely used in many other fields.
For example, in the aerospace field, molds are used to process precision carbon fiber parts, aiding the smooth operation of aircraft.
In the construction field, molds are used to produce waterproof isolation materials for buildings, which enhances product quality. The product molds in the construction field are shown in Figure 5.

Precision mold manufacturing technology plays an important role in various fields.
With the continuous development of technology, the application fields and processing methods of precision molds will be more diversified, flexible and efficient.
Future development trend
Intellectualization
By using advanced intelligent control technology, the mold can automatically adjust and detect. It also supports remote control.
This greatly improves the efficiency and quality of precision mold manufacturing while reducing manual intervention in the manufacturing process.
Generalization and high efficiency
Traditional precision mold manufacturing cycle is long, and personalized production has a certain degree of difficulty.
Generalization and high-performance mold manufacturing has become the future development trend.
Generalization of the mold is able to provide technical support for the production of a variety of types of products, molds, can achieve a variety of types of products, improve the utilization rate of the mold.
High-performance molds have faster, more stable and more energy-saving performance, can achieve efficient operation of the production process, thereby improving manufacturing efficiency and cost-effectiveness.
Mass Customization
In many fields, products from different brands, models, and specifications have varying requirements for mold precision, shape, and size.
Therefore, it is necessary to study and develop large-scale customization of precision molds.
Mass customization mold refers to the individualized design according to the customer’s needs on the basis of scale, integration of precision manufacturing technology, and rational planning of the production process.
Mold manufacturing focuses on deep customization to achieve continuous process optimization. Intelligent assistance helps accelerate production and reduce manpower consumption.
This also ensures product quality while enhancing market competitiveness.
Transformation and upgrading
Currently, the precision mold manufacturing industry is undergoing transformation and upgrading.
This is due to intensified market competition and the application of intelligent technology, which promotes industrial upgrading.
In the development process, the focus is on building experiential and quality characteristics of the “new plant.”
Through collaborative innovation, intelligent manufacturing and industrial change are achieved.
This leads the precision mold manufacturing industry toward high-tech, high value-added, and high-quality economic growth. The industry continues to upgrade in this direction.
Precision mold manufacturing industry in the future will be driven by both technology and market, showing more intelligent, generalized, customized and environmentally friendly development trend.
Only by actively catering to the new development model, and constantly promote reform and innovation, in order to be invincible in the fierce market competition.
Conclusion
This paper provides an in-depth discussion on the knowledge related to precision mold manufacturing.
It draws conclusions based on relevant literature research and case studies.
Importance
The processing accuracy and manufacturing cycle of precision molds are crucial for many industries.
Development trend
Precision mold manufacturing technology will develop rapidly in terms of intelligence, generalization, high efficiency, mass customization and environmental protection.
Collaboration
By cooperating with enterprises and research institutes in many fields, we can accelerate the progress of technical research and development, improve precision, reduce costs and realize faster technical upgrading.
The future development of precision mold manufacturing industry pay more attention to the following aspects of research and application.
Intelligent technology
Increase research and investment in automation, digitalization, Internet of Things and intelligent control, etc., to promote intelligent mold manufacturing technology.
Green manufacturing
The use of environmentally friendly materials, green design, and in the manufacturing process to reduce the impact on the environment, to achieve the environmental protection of precision mold manufacturing.
Collaborative Innovation
Various research institutions and enterprises are collaborating on the concept, technology, and resources.
They aim for in-depth cooperation and joint development of advanced precision mold manufacturing technology.
The goal is to achieve improvements in quality, efficiency, innovation, and development.
The future of precision mold manufacturing industry is full of opportunities and challenges.
Through continuous and in-depth research and innovation, we can improve existing technology. Additionally, we will conduct research on cutting-edge technology.
These efforts will help make a greater contribution to the sustainable development of the precision mold industry.