Additive manufacturing technology is a manufacturing method that converts a digital model into an actual object by using computer-aided design (CAD) software and computer-aided manufacturing (CAM) software to convert a digital model into a physical model.
This manufacturing method has the advantages of high efficiency, flexibility, high accuracy, etc., and has been widely used in many fields, including aerospace, automobile manufacturing, and medical devices.
Special Machining Technology for Metal Materials
Special processing technology for metal materials is a branch of rapid manufacturing technology, which is mainly applied to the processing and manufacturing of metal materials.
Traditional metal processing methods such as casting, forging, cutting, etc. have some limitations, such as long production cycle, high cost, low precision, etc..
Application and Significance of Special Machining Technology
The special technology, on the other hand, can quickly and accurately manufacture complex metal parts and workpieces through the use of advanced machining equipment and materials, which has good application prospects.
This special technology can be applied to aerospace, automobile manufacturing, machinery manufacturing, medical equipment and other fields.
For example, in the field of aerospace, special machining technology can be used to manufacture high-strength, lightweight aviation parts.
In the field of medical devices, special machining technology can be used to manufacture high-precision, complex medical devices.
Therefore, the development of special machining technology is of great significance for improving the level of manufacturing, promoting industrial upgrading and economic development.
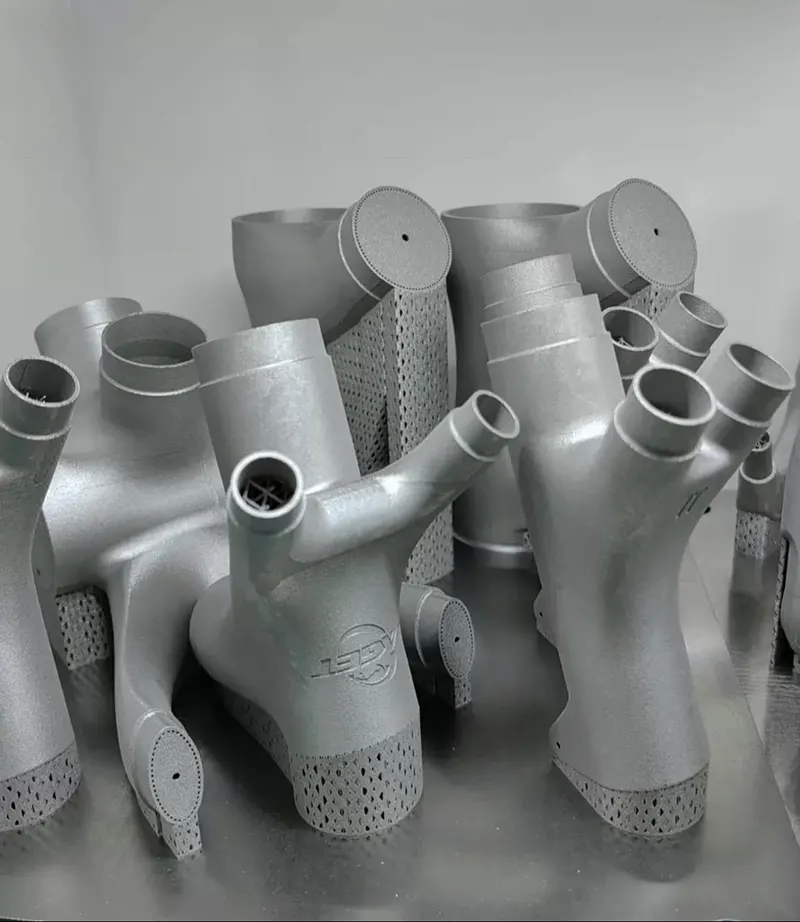
Overview of metal material rapid manufacturing technology
Metal material additive manufacturing technology is a new type of manufacturing technology based on digital design.
It uses lasers, electron beams, and other energy sources. Through layer-by-layer stacking, melting, or solid-state connection, this technology directly manufactures metal parts.
It can manufacture complex metal parts quickly, efficiently, and accurately, with a high degree of flexibility and customizability.
This is achieved through digital design, rapid prototyping, rapid testing, and other technical means.
Based on the manufacturing principle and process characteristics, metal material rapid manufacturing technology can be divided into the following five categories:
First:
Laser melting forming technology uses laser beams or electron beams, along with other high-energy sources.
These energy sources heat metal materials to their melting point or semi-solid state. Through methods like layer-by-layer stacking or scanning molding, the technology directly manufactures metal parts.
Second:
Electron beam forming technology uses an electron beam stream to heat the metal material to its melting point or semi-solid state.
Through methods like layer-by-layer stacking or scanning forming, it directly manufactures metal parts.
Third:
Plasma arc forming technology uses a plasma arc and other high-temperature energy sources.
This process heats the metal material to its melting point or semi-solid state. Through layer-by-layer stacking or scanning molding, it directly manufactures metal parts.
Fourth:
Metal powder sintering molding technology, metal powder pressurized molding, and then sintered at high temperature, so that it becomes an integrated metal parts;
Fifth:
Metal powder spraying molding technology, metal powder sprayed onto the substrate through spraying technology, and then sintered at high temperature, so that it becomes an integrated metal parts.
Advantages and disadvantages of metal material rapid manufacturing technology
1. Advantages
(1) Short manufacturing cycle:
the use of digital design and direct manufacturing can significantly shorten the manufacturing cycle and improve manufacturing efficiency.
(2) Strong customizability:
adopting digital design and direct manufacturing, it can be personalized according to customer needs and improve the added value of products.
(3) High manufacturing precision:
the use of high energy source processing can realize high precision manufacturing and improve product quality and performance.
(4) Can reduce costs:
the way of digital design and direct manufacturing can reduce the waste of raw materials and save human resources, and reduce manufacturing costs.
2. Disadvantages
(1) High manufacturing cost:
metal material additive manufacturing technology requires high energy source and expensive equipment, high manufacturing cost.
(2) Limited choice of materials:
metal material rapid manufacturing technology has some limitations on the choice of materials, and can only manufacture some metal material parts at present.
(3) Manufacturing size is limited:
at present, the metal material additive manufacturing technology can only manufacture smaller-sized parts, and the technology for manufacturing large-sized parts has not yet matured.
(4) Manufacturing accuracy is limited:
metal material rapid manufacturing technology in the manufacturing accuracy is subject to certain limitations, can not meet the manufacturing needs of certain high-precision parts.
Limitations of traditional machining technologies
Traditional metal machining technologies include milling, turning, drilling, casting, etc.
Although these technologies have undergone decades or even centuries of development, they still have some limitations.
Among them, the most prominent problems include long machining time, high cost, and low precision.
Challenges of Traditional Metal Machining
First of all, traditional metal processing technology requires multiple processes.
Each process involves different operations, and several rounds of processing are needed before the final product can be obtained.
This leads to long processing time, which increases the cost. Secondly, the cost of traditional metalworking technology is high.
As multiple processes are required, each process requires different tools and equipment, which leads to an increase in the cost of equipment and materials.
At the same time, as the processing time becomes longer, the wage cost of workers also increases. Finally, traditional metalworking techniques have low precision.
Since multiple processes are required, each process brings a certain amount of error, which ultimately leads to a lower precision of the product.
The Need for New Machining Technologies
In addition, traditional machining techniques are hand operated, and the skills and experience of the workers also affect the accuracy of the products.
As the market demand increases, faster, more accurate and economical machining techniques are needed.
Therefore, people need to look for new processing technologies to meet the market demand.
Some new technologies such as laser cutting, CNC machining, and 3D printing have gradually been widely adopted.
These technologies can reduce processing time, improve accuracy, and enable more economical machining processes.
Overview of special processing technologies
(1) Laser melting deposition technology:
It uses a high energy density laser beam to melt and deposit metal powder onto the surface of the workpiece to form the desired shape.
The technology is characterized by high precision, high efficiency, and low cost, and is suitable for manufacturing parts with complex shapes.
(2) Electron beam melting deposition technology:
It uses a high-speed electron beam to melt and deposit metal powder onto the surface of the workpiece to form the desired shape.
This technology is characterized by high precision, high efficiency and low cost, and is suitable for manufacturing high-temperature, high-strength and high-corrosion-resistant parts.
(3) Selective laser sintering technology:
It utilizes a laser beam to sinter metal powders together to form the desired shape.
SLS is characterized by high precision, high efficiency and low cost, and is suitable for manufacturing small-lot, high-precision parts.
(4) Electrochemical machining technology:
It used an electrochemical reaction to deposit metal powder onto the surface of the workpiece to form the desired shape.
EM is characterized by high precision, high efficiency and low cost, and is suitable for manufacturing complex shaped parts.
(5) Thermal Spraying Technology:
The technology sprays metal powder onto the surface of the workpiece to form the desired shape.
TS is characterized by high efficiency and low cost, and is suitable for manufacturing large parts or repairing the surface of parts.
Different types of special machining methods
1. Specialty Machining Process Modeling
The process of special machining is highly complex. The processing of metal materials in different contexts involves fields such as electrical, thermal, and chemical sciences.
Compared to traditional processing methods, its principles are much more challenging. It cannot be explained or realized through a single principle or formula.
With the continuous development of science and technology, technical researchers have conducted in-depth studies on special machining technology modeling concepts.
They consider different application scenarios and materials in their research.
Supported by various artificial intelligence technologies, they use modeling to describe the entire special machining process in detail and with clarity.
Through the established model, technicians can ensure the accuracy and efficiency of processing conditions.
They use simulation experiments for verification, allowing them to assess actual production results. This helps guide real production and address potential issues that may arise during processing.
2. Intelligent control of special processing
Since the birth of the concept of special machining, technicians have relied on various processing principles.
These include utilizing the chemical properties of metal materials and employing detailed models. Through these methods, they achieve the desired machining of metal materials.
However, from the perspective of control theory, classical control methods alone cannot achieve the desired results.
For a long time, people have used adaptive control strategies to regulate processing conditions.
These strategies have significantly improved product performance and extended service life.
In recent years, researchers have focused on techniques such as fuzzy control, which has a wide range of applications in precision machinery.
These technology can automatically capture the best data to control the entire metal material processing process.
It can also monitor and address any irrationalities or errors that arise during the metal material processing at any time.
At the same time, by combining the principles of artificial intelligence and big data analysis, this technology can predict the possible outcomes of various scenarios.
This helps provide insights for production design and maximizes the quality of production.
3. New special processing technology
Since the beginning of the 20th century, the development of machinery, industry, and other emerging fields has driven the diversification of high-efficiency special processing technology.
This advancement has had a significant impact on the metal materials manufacturing industry, enabling rapid manufacturing processes.
Magnetic grinding technology utilizes the magnetic field to achieve surface grinding and polishing of complex metal parts.
During the process, it strictly controls the distance between parts and instruments to maintain optimal conditions, improving production efficiency.
In practice, it enables automatic polishing while keeping production costs low.
Currently, in the study of technological mechanisms, technicians have analyzed key factors such as magnetic field strength and abrasive strength.
Their goal is to understand the relationship between these factors and production conditions.
By identifying the key elements affecting the production process, they can adjust different parameters. This approach helps improve production efficiency.
Optimization strategy of laser melting deposition technology
1. Selection of appropriate materials
The selection of appropriate materials is crucial when using laser fusion deposition technology.
The selection of materials should take into account factors such as their melting point, thermal conductivity, expansion coefficient and chemical composition.
Materials with high melting points and low thermal conductivity usually require higher laser power and longer processing times.
Differences in chemical composition can result in materials with different coefficients of thermal expansion. This variation may affect the dimensional accuracy and shape stability of the part.
2. Optimizing Laser Parameters
The choice of laser parameters is critical to the quality and efficiency of manufactured parts. Parameters such as laser power, scanning speed, laser beam diameter, and laser pulse frequency all affect heat transfer and melt pool formation during melting and deposition.
Typically, high power and low scan speed laser parameters increase the depth and width of the melt pool, which increases the deposition rate and part density.
However, too high power and too low scanning speed may lead to excessive melting of the melt pool and formation of pores, thus reducing the quality of the parts.
The temperature cycling characteristics during the laser melting deposition process can be altered by adjusting the laser scanning strategy.
The relationship between temperature cycling characteristics, physical phase organization, and mechanical properties can then be explored.
This allows for the regulation of physical phase organization and mechanical properties of the materials through temperature cycling characteristics.
This method can simplify the subsequent heat treatment process, and has the engineering application advantages of improving the production efficiency of components and reducing energy consumption.
3. Optimization of process parameters
The selection of process parameters is also an important factor affecting manufacturing efficiency and quality.
Parameters such as the thickness of the deposition layer, preheating temperature, atmosphere protection and post-treatment all affect the quality and stability of the part.
Typically, larger deposition layer thicknesses increase manufacturing efficiency, but also increase the risk of thermal stress and distortion.
Appropriate preheating temperatures can reduce the risk of thermal stress and distortion, while atmosphere protection can prevent material oxidation and the formation of porosity.
Post-processing can further improve part quality and stability, for example, annealing can reduce residual stresses and increase material toughness.
In summary, laser fusion deposition technology can be optimized to improve manufacturing efficiency and quality by selecting appropriate materials, laser parameters and process parameters.
In practical application, the parameters need to be optimized and adjusted according to specific manufacturing requirements and material properties to obtain the best manufacturing results.
In addition, the molten pool characteristics and solidification conditions can be regulated during the printing process.
This regulation not only optimizes the deposited alloy densities but also contributes to the formation of a unique crystalline lamellar organization.
It also promotes intrinsic thermal deformation and heat treatment during the deposition process. This, in turn, induces higher dislocation densities and grain refinement.
As a result, there is a significant enhancement of the strength and plasticity of the deposited components, without the need for subsequent heat treatment.
Application and outlook
Special machining technology is an efficient and precise machining method that can realize rapid and high quality production in the manufacturing process of metal materials.
The following are the applications and characteristics of special processing technology in the rapid manufacturing of metal materials.
One is laser processing technology, which is a high energy density processing method that can cut, punch, etch and other processing on metal materials.
Laser processing technology has the advantages of fast processing speed, high precision, good processing quality, etc., especially suitable for rapid manufacturing of metal materials.
Secondly, EDM technology, the technology is a method of processing through electric spark discharge, which can carry out precision processing on metal materials.
EDM technology has the advantages of high processing precision, good processing surface quality, etc., especially suitable for tiny processing of metal materials.
Third, ultrasonic processing technology, the ultrasonic processing technology is a method of processing using ultrasonic vibration, can be cut, welded and other processing on metal materials.
Ultrasonic processing technology has the advantages of fast processing speed and good processing quality, especially suitable for rapid manufacturing of metal materials.
The development trend and prospects of special processing technology are as follows.
(1) high efficiency, precision processing.
With the continuous progress of science and technology, special processing technology will become increasingly efficient and precise.
This advancement makes the rapid manufacture of metal materials easier to realize.
(2) automation, intelligent processing.
The technology will become more and more automated, intelligent, making the processing more intelligent and efficient.
(3) multi-functional processing.
The special technology will become increasingly multifunctional.
It can be realized on the same equipment with a variety of processing methods. This will help improve processing efficiency.
(4) environmental protection, energy-saving processing.
The processing technology will become more and more environmentally friendly, energy saving, reduce environmental pollution, reduce energy consumption.
Conclusion
Specialty machining technology for the rapid manufacturing of metal materials provides an efficient, flexible, and precise manufacturing method.
This is achieved through the combination of digital design and high-energy sources, which greatly promotes the development of the metal processing field.
Compared with traditional machining methods, special machining technology offers several advantages.
It can shorten the production cycle and improve product accuracy.
Additionally, it meets the demand for personalized customization and helps reduce production costs.
In the field of aerospace, special machining technology has shown broad application prospects.
This technology is also applicable in automobile manufacturing, medical equipment, and other high-precision and complex workpieces.
Nonetheless, additive manufacturing technology for metallic materials still faces some challenges.
These challenges include material selection, manufacturing cost, precision limitations, and dimensional constraints.
To promote the further application and development of this technology, researchers need to continuously optimize the use of energy sources such as lasers and electron beams.
They must also focus on improving processing accuracy, expanding the range of applicable materials, and exploring more efficient and low-cost manufacturing modes.