Table of Contents
Mold production technology has become a country’s manufacturing level indicator. Molds largely determine product quality, efficiency, and new product development.
With China’s entry into the WTO, the mold industry faces new opportunities and challenges.
The development of China’s mold industry has gained more attention. Molds are widely agreed to be essential equipment for industrial production.
In industries like electronics, automobiles, and home appliances, 60% to 80% of parts rely on molds. Mold-made parts offer high precision, complexity, consistency, and productivity, unmatched by other methods.
Molds are also “benefit amplifiers.” The final product’s value is often much higher than the mold’s cost.
Currently, the global mold industry generates about $60 billion annually. In industrially developed countries like Japan and the U.S., mold output surpasses machine tool industry output.
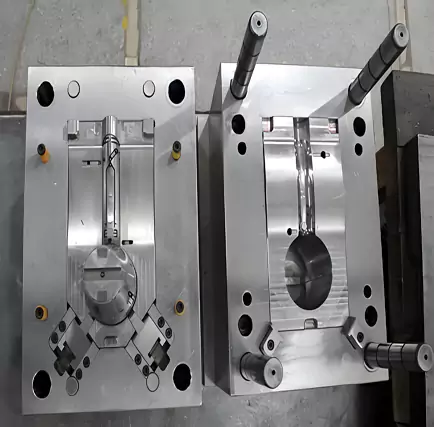
The current status of China’s mold technology
1. Dies
China has produced some car cover dies, with large-scale cover dies as a representative example. Designing and manufacturing car cover dies is challenging due to high quality and precision requirements. This reflects the advanced level of the cover die technology. China’s design and manufacturing methods now align with international standards, and the mold structure and functions are nearly on par with global levels. This marks significant progress in the localization of car molds.
However, gaps remain in manufacturing quality, precision, cycle time, and cost compared to other countries. Multi-position progressive dies and multi-functional molds, which represent advanced die technology, are key areas of focus for China. There is still a gap in manufacturing precision, service life, mold structure, and function compared to foreign multi-position progressive dies and multi-functional molds.
2. Plastic molds
China’s plastic mold industry has made significant strides in recent years.
For large plastic molds, the country now produces 34-inch color TV shell molds, 6kg washing machine molds, automobile bumpers, instrument panels, and more.
In precision plastic molds, China manufactures multi-cavity small-module gear molds, 600-cavity plastic sealing molds, and 1-mold 2-cavity aviation cup molds with a thickness of just 0.08mm. They also produce complex plastic door and window extrusion molds.
Hot runner devices, both internal and external, are used in many molds, with some featuring highly advanced needle valve hot runner systems that eliminate gate marks. Gas-assisted injection technology is also now applied.
Regarding precision, plastic mold cavities reach a manufacturing accuracy of 0.02~0.05mm, with the contact gap of parting surfaces at 0.02mm. The template’s elastic deformation is limited to 0.05mm, and mold surface roughness is Ra0.2~0.25um.
The plastic mold life has reached 1 million cycles (compared to 3 million abroad), though the mold production cycle is still 2~4 times longer than foreign standards. Overall, these parameters show that China still lags behind foreign countries in-mold technology.
3. Die-casting molds.
The rapid growth of the automobile and motorcycle industries has driven advances in die-casting mold technology. China now produces aluminum alloy casting molds for automotive engine cylinder covers, cover plates, transmission housings, motorcycle engine cylinders, gearbox housings, brakes, wheels, and escalator steps. The technology has improved significantly, and most aluminum alloy die-casting molds for these industries are now made domestically.
Designing the mold requires careful attention to thermal balance, pouring systems, and cooling systems. Manufacturers also use hydraulic core pulling and secondary pressurization structures based on specific requirements. As a result, the overall quality has greatly improved. Die-casting molds now achieve manufacturing accuracy of 0.02–0.05mm (compared to 0.01–0.03mm abroad). The cavity surface roughness ranges from Ra 0.4–0.2μm (Ra 0.02–0.01μm abroad).
Mold production cycles are as follows: 3–4 months for small to medium molds, 4–8 months for medium-complex molds, and 8–12 months for large molds, which is about twice the time compared to foreign standards. The typical lifespan of aluminum alloy casting molds is 40,000 to 80,000 cycles, with some molds exceeding 100,000 cycles. In foreign countries, molds can last between 80,000 to 150,000 cycles or more.
4. Mold CAD/CAE/CAM technology
Mold CAD/CAE/CAM technology transforms traditional mold production methods. It shortens design and manufacturing cycles, reduces costs, and improves product quality. Technicians use computers to design and optimize products, mold structures, forming processes, CNC machining, and costs. Household appliance manufacturers have adopted many CAD/CAM systems, integrated CAD/CAM, and used CAE to simulate molding processes. The increased use of CNC machining has led to economic benefits and advanced China’s mold CAD/CAE/CAM technology.
Recently, China developed CAD/CAM systems for punching and cutting dies at Shanghai Jiaotong University, CAXA series software by Beijing Beihang Haier Software Co., and a stamping CAD/CAE/CAM system at Jilin Jinmesh Die Engineering Research Center. These advancements support the wider use of die CAD/CAM technology. However, China’s computer-aided technology development is still in the early stages and requires more knowledge and experience.
5. Standard parts of molds
Standard mold parts shorten manufacturing cycles, improve quality, and reduce costs. As a result, their use is growing. These parts include cold stamping die frames, plastic die frames, push rods, and springs. New elastic components, such as nitrogen springs, have also seen increased use.
6. Mold materials and heat treatment
Mold material quality, performance, variety, and timely supply directly impact the mold’s quality, service life, and economic benefits. Recently, some Chinese mold steel manufacturers have introduced advanced equipment, improving the specifications and quality of domestic mold steels. However, the range of domestic mold steels remains incomplete, with issues such as too many varieties and unfinished products.
Further research is needed on material series for forming molds used in glass, ceramics, refractory bricks, and floor tiles. Mold heat treatment plays a crucial role in ensuring mold steel performance. Many domestic companies still use salt-melting or electric furnaces for quenching. Poor implementation of heat treatment processes leads to unstable quality, affecting the mold’s service life. However, vacuum heat treatment furnaces are becoming more common in mold manufacturing.
Development trend of mold technology
1. Mold CAD/CAE/CAM is developing towards integration, three-dimensionalization, intelligence, and networking
(1)Integration of mold software functions
To integrate mold software functions, the software must have complete functional modules. Each module should adopt the same data model to enable comprehensive management and information sharing. This supports all stages of mold design, manufacturing, assembly, inspection, testing, and production management, helping achieve optimal benefits.
For example, Delcam’s serialized software includes surface solid geometry modeling, complex shape engineering drawing, advanced rendering for industrial design, an expert system for plastic mold design, complex shape CAM, an automatic programming system for artistic modeling and carving, reverse engineering, and an online measurement system for complex shapes. Other highly integrated software includes Pro/E, UG, and CATIA.
(2)Three-dimensional mold design, analysis, and manufacturing
Traditional 2D mold design struggles to meet modern production and tech requirements. Three-dimensional, paperless mold design demands new software to facilitate intuitive design and analysis. These 3D digital models enable CAE analysis, mold manufacturability evaluation, CNC machining, forming simulations, and efficient information sharing. Software like Pro/E, UG, and CATIA supports parameterization, feature-based designs, and full correlation, enabling parallel mold engineering.
Cimatron’s Moldexpert, Delcam’s Ps-mold, and Hitachi Zosen’s Space-E/mold are advanced 3D design tools for mold cavity, core, frame, and structure design. Moldflow Advisers, a 3D flow simulation tool, is highly praised and widely used. Mold software’s knowledge-based intelligence is a key measure of its effectiveness.
Cimatron’s software, for example, automatically generates parting lines, parting surfaces, cores, and cavities. It ensures full mold part correlation, generates NC processing lists, and enables intelligent processing settings and verification.
(3)Networking trend of mold software application
With the globalization and internationalization of molds in enterprise competition, cooperation, production, and management, as well as the rapid development of computer software and hardware technology: the development trend of networked mold software applications is to promote CAD/CAE/
(4)Networking trend of mold software application
As molds globalize and industries face more competition, collaboration, and management challenges, the rapid growth of computer software and hardware drives change. Networked mold software development aims to integrate CAD/CAE/CAM technology across regions, businesses, and research institutes.
This reintegration of technical resources enables virtual design and agile manufacturing. The United States, in its “21st Century Manufacturing Enterprise Strategy,” predicted that by 2006, the automotive industry would achieve agile production and virtual engineering, cutting the vehicle development cycle from 40 months to just 4 months.
2. Mold inspection and processing equipment develops towards precision, efficiency, and multi-function
(1)Molds develop
Molds develop towards precision, complexity, and large scale, and the requirements for inspection equipment are getting higher and higher. At present, domestic manufacturers use more high-precision three-coordinate measuring machines from Italy, the United States, Japan, and other countries, which have digital scanning functions. The whole process from measuring the physical object → establishing the mathematical model → outputting the engineering drawing → mold manufacturing has been realized, and the development and application of reverse engineering technology have been successfully realized.
(2)CNC EDM machine tools
Sodick of Japan uses linear motor servo drive AO325L and AO550LLS-WEDM, which have the advantages of fast drive response, high transmission and positioning accuracy, and small thermal deformation. NCEDM of Charmilles of Switzerland has P-E3 adaptive control, PCE energy control, and an automatic programming expert system. In addition, some EDMs also use mixed powder processing technology, micro-precision processing pulse power supply fuzzy control (FC), and other technologies.
(3)High-speed milling machine tools (HSM)
Milling is an important means of cavity mold processing. High-speed milling has many advantages such as low workpiece temperature rise, small cutting force, stable processing, good processing quality, high processing efficiency (5 to 10 times that of ordinary milling), and the ability to process hard materials (<60HRC). Therefore, it is increasingly valued in mold processing. HSM is mainly used for large and medium-sized mold processing, such as automotive cover molds, die-casting molds, large plastic molds, and other curved surface processing.
(4)Research and development of mold automatic processing system
With the rapid development of various new technologies, mold automatic processing systems have appeared abroad, which is also the long-term development goal of my country. The mold automatic processing system should have the following characteristics: a reasonable combination of multiple machine tools; equipped with accompanying positioning fixtures or positioning plates; a complete CNC library of machines and tools; a complete CNC flexible synchronization system; and a quality monitoring and control system.
3. Wide application of rapid and economical molding technology
Shortening the product development cycle helps companies win in the market. Compared to traditional mold processing, rapid molding technology offers a shorter cycle and lower cost. It also meets production requirements for accuracy and lifespan, delivering strong economic benefits.
Rapid prototyping manufacturing (RPM) technology integrates precision machinery, computer systems, NC technology, laser molding, and materials science. It is one of the most advanced methods for mold and part manufacturing. RPM technology can be used directly or indirectly in mold making. It is cost-effective, quick, and moderately precise. RPM reduces mold design and production time to just one-third of traditional methods and cuts costs by about 75%.
We live in an era of low-volume, high-variety production. By the next century, this model will account for over 75% of industrial output. Product lifespans are short, and varieties change rapidly. This requires fast mold production cycles. Consequently, the demand for rapid, cost-effective molds continues to grow.
Examples include molds made from superplastic materials (epoxy, polyester), metal powder-filled molds, and medium-low melting point alloy molds. Other molds, such as spray molds, electroforming molds, and ceramic precision molds, will also see growth. Quick-change mold bases and punches are also on the rise. Additionally, new mold-changing devices, along with robotic-controlled mold trials, will continue to improve.
4. Research on mold materials and surface treatment technology
Improper material selection and use cause molds to fail prematurely, making up over 45% of mold failures. Materials account for only 20%–30% of total mold costs, but selecting high-quality steel and applying surface treatment technology is crucial to eextendingmold life. Mold steel should undergo electro-slag remelting to improve purity, isotropy, density, and uniformity. Developing higher-performance steels, like powder high-speed steel from powder metallurgy, can also enhance mold longevity.
Powder high-speed steel addresses the issue of coarse and segregated primary carbides in traditional steel. Its fine, uniform carbides eliminate material directionality, offering high toughness, excellent grindability, superior wear resistance, and long-term dimensional stability. This makes it especially advantageous for complex punching parts and high-speed stamping molds. As mold steel varieties diversify, product refinement and shorter delivery times become key trends.
Heat treatment and surface treatment are crucial for maximizing mold steel performance. Trends in mold heat treatment are shifting from single-element infiltration to multi-element co-infiltration, such as the TD method. Plating options have expanded to include TiC, TiN, TiCN, TAIN, CrN, Cr7C3, and W2C. Heat treatment methods are moving from atmospheric to vacuum treatments, and new techniques like laser strengthening, glow ion nitriding, and electroplating are gaining importance for anti-corrosion and strengthening.
5. Mold grinding and polishing will develop towards automation and intelligence
Mold surface finishing remains a key challenge in mold processing. The mold surface quality significantly impacts service life and product appearance. In China, manual grinding and polishing dominate the process. This method is inefficient, accounting for about 1/3 of the total mold manufacturing cycle. It also requires high labor intensity and results in inconsistent quality. These issues hinder the advancement of mold processing in China.
To address this, research on automated and intelligent polishing methods is essential for future development.
Japan has developed CNC grinding machines that automate three-dimensional curved surface grinding and polishing. However, the complex shape of mold cavities limits conventional methods. To improve surface quality, new techniques such as extrusion grinding, electrochemical polishing, ultrasonic polishing, and composite polishing must be explored and developed.
6. The application of mold standard parts will become more and more extensive
Mold standard parts shorten the manufacturing cycle, improve quality, and reduce costs. As a result, their use will expand.
First, establish a unified national standard and enforce strict production standards.
Second, build large-scale production to enhance quality and lower costs.
Third, increase specifications and varieties, and improve the joint sales network for faster supply.
7. The proportion of die-casting dies, extrusion dies and powder forging dies will increase
With the development of lightweight products such as automobiles, vehicles, and motors, the proportion of die-casting dies will continue to increase, and higher and higher requirements will be placed on the life and complexity of die-casting dies. At the same time, the proportion of extrusion dies and powder forging dies will also increase to varying degrees, and the precision requirements will also become higher and higher.
8. New technologies, new concepts, and new models in the mold industry
Here’s a rewritten version with active voice, segmentation, and shorter phrases while retaining the original meaning:
The forming (molding) process involves several technologies. These include multifunctional composite stamping dies, superplastic forming, and plastic precision forming. It also covers plastic mold gas-assisted injection and hot runner technologies. High-pressure injection molding technology is also part of this process.
Meanwhile, advanced manufacturing technologies and improvements in the mold industry have introduced new concepts. These include flexible manufacturing, which suits single-piece mold production. Lean production and team spirit boost management and efficiency.
New production philosophies, such as parallel engineering and virtual manufacturing, enhance rapid response. Global agile manufacturing and network manufacturing improve flexibility. The industry widely adopts the division of labor and cooperative production for standard and general parts. Finally, green design and sustainable manufacturing meet environmental and development goals.
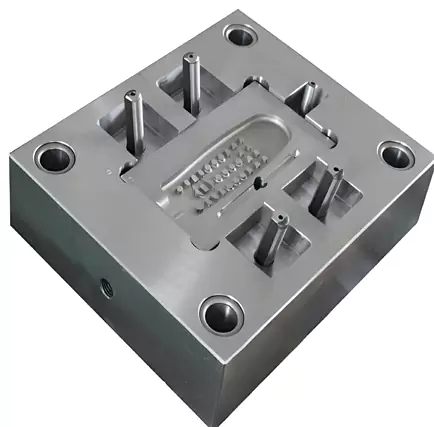
Conclusion
Here’s a rewritten version of your passage with active voice, shorter phrases, proper segmentation, and maintaining the original meaning:
China’s mold industry is rapidly developing. However, its overall mold design, manufacturing, and standardization still lag behind developed countries like Germany, the U.S., and Japan. With economic globalization and the reintegration of capital, technology, and labor markets, China’s equipment manufacturing industry is set to become the global hub after joining the WTO.
In modern manufacturing, industries increasingly rely on products from the mold industry. To meet the growing demand for high precision, short delivery times, and low costs, the mold industry must adopt advanced manufacturing technologies. This will accelerate technological progress and help the mold industry meet the urgent needs of various sectors, driving the leapfrog development of China’s mold industry.