Table of Contents
Thin-walled parts present significant challenges in CNC milling. Their lightweight and thin features increase instability in production.
If the process ignores part rigidity or strength, high-speed cutting can cause deformation. Uneven force leads to precision errors, surface unevenness, or burr chamfering, widening the gap between design and production.
To improve accuracy, adjust the CNC machining process for thin-walled parts gradually. Use technical design and planning to enhance production precision.
Analyzing the causes of issues in thin-walled part processing helps identify targeted solutions. Reducing deformation, improving workpiece quality, and shortening processing time are key steps in the process.
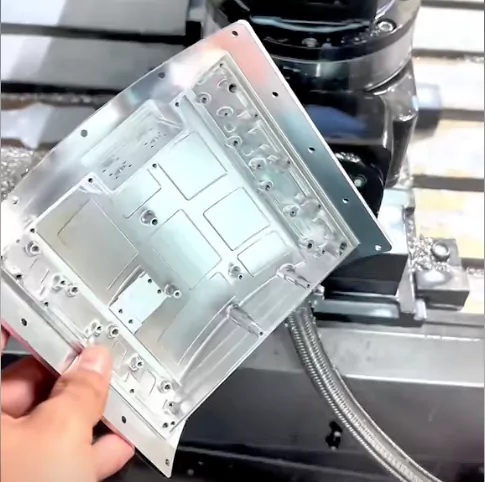
The current situation of thin-walled parts
Thin-walled parts are widely used in various fields, but due to the complexity of their internal structure, a variety of problems arise during the CNC milling process. These challenges not only hinder the development of the thin-walled parts processing industry but also restrict the advancement of related fields where these parts are applied.
1. Challenges in CNC Milling of Thin-Walled Parts
The internal complexity of thin-walled parts leads to various issues during CNC milling, which can affect the overall quality of the parts. These problems are particularly significant in industries that demand high precision, such as aerospace.
In the aerospace industry, the application of thin-walled parts must meet strict standards. The need for continued development and improvement of CNC milling technology is essential to keep up with the high demands of modern aerospace engineering.
Aluminum alloy parts, for example, offer advantages such as thin walls, lightweight design, high strength, and strong corrosion resistance. These characteristics make them ideal for high-speed and high-performance applications in the aerospace sector. Consequently, the use of thin-walled parts in aerospace is increasing.
2 . Issues with CNC Milling in Thin-Walled Part Production
While CNC milling is commonly used for processing thin-walled parts, the complexity of their structure and their relatively low stiffness make them prone to deformation during machining. This results in a range of issues, including:
Uneven thickness of the wall
Inaccurate sizes
Overall quality degradation
These issues can prevent the parts from meeting the precision requirements of industries such as aerospace.
During the CNC milling process, thin-walled parts often experience deformation, which affects their dimensional accuracy. As a result, the final product may not meet the desired specifications, particularly in industries with strict tolerance requirements.
3. Current Solutions and Their Limitations
To ensure accuracy, many processing plants use fine machining techniques in the final stages of manufacturing thin-walled parts. This often involves no-feed light cutting to improve quality. While this method enhances precision, it also has its drawbacks, including:
Increased time consumption
Higher material waste
Reduced overall productivity
Another issue is the potential for rough surfaces due to residual fine slag in the tool gap, which can lead to imperfections in the machined surface of the thin-walled parts.
4 . The Path Forward: Improving Thin-Walled Part Manufacturing
Addressing the challenges of thin-walled part production during CNC milling is critical to improving efficiency and product quality. Research into manufacturing high-quality, efficient thin-walled parts remains a key focus, as the industry continues to seek solutions for minimizing deformation, enhancing accuracy, and reducing waste.
Problems and reasons in the CNC milling machining process of thin-walled parts
1. Problems
(1) Challenges in Achieving High Precision
CNC milling thin-walled parts require fine processing to achieve high-quality results. Thin-walled parts are fragile, so ensure precision. Carefully analyze internal structures and choose cutting tools and forces to avoid damage during manipulation.
(2) Cutting Force and Tool Selection Issues
High error or breakage rates are common challenges. Incorrect cutting force parameters can cause discrepancies between design and actual conditions. If the cutting force exceeds the thin-walled part’s load capacity, it may deform.
(3) Thermal Deformation and Tool Overheating
Overheating milling tools during long processing times is a concern. Thin-walled parts have low thermal load capacity. Excessive thermal stress can cause deformation if it exceeds the blade’s or part’s load limits.
(4) Need for Process Improvement
To reduce these issues, analyze the CNC milling process more thoroughly. Adjust operations improved the production and processing of thin-walled parts.
2. Causes
Due to the complexity of the internal structure of thin-walled parts, various problems can easily occur during processing. CNC milling process, thin-walled parts may produce a relatively large number of problems, the main reason is that there are differences between the machining process and the load-bearing properties of the parts themselves, resulting in parts production during the production of broken or micro deformation. From the point of view of the parts production situation, the following problems may arise during the application of technical processes:
(1)Cutting heat
High-speed rotary tools or cutting, etc. will produce thermal values and will have an impact on the internal material or structure of thin-walled parts, which in turn produces deformation problems. Thin-walled parts of the material structure and special shape, so that thin-walled parts because of the impact of processing heat corresponding deformation.
(2)Stress Load
Wear and tear of the tool over a long period can cause damage to the surface of thin-walled parts. A milling tool is a continuous consumption product, with a long time operation mode, the internal structure may be broken, and once the tool surface gap, the impact on the parts is fatal.
(3)Unstandardized operation
Thin-walled parts clamping process and non-standardized operation will lead to deformation of the parts. Thin-walled parts of the internal material are thin, and high vulnerability, if the fixture clamping process does not follow the physical properties of the parts themselves, it will produce deformation problems.
(4)Improper tool lowering method
Improper tool setting or parameter setting can lead to deformation of the part. If there is an error in the way of cutting, it will destroy the thin-walled parts. For example, in the production process, if the position of the lower cutter is at the end of the part, it is very easy to produce due to the rotational speed or reverse order of the cutting method of the error between the parts of substandard quality problems.
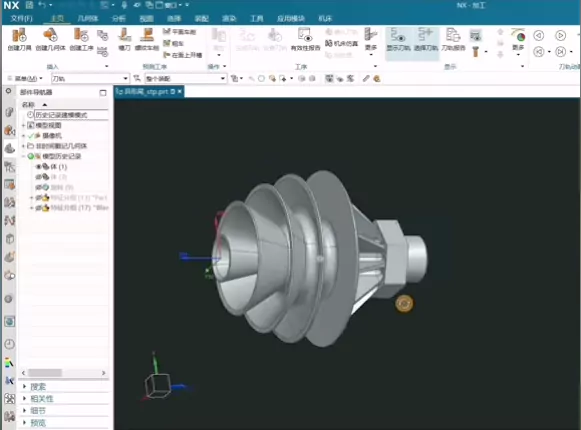
Application of machining processes
1. mechanical characterization of parts
The mechanical properties of parts during machining are crucial for determining final accuracy and quality. Key factors include mechanical stiffness, geometric accuracy, tool vibration, tool wear, and thermal deformation. Understanding these factors is vital, especially when machining thin-walled parts with CNC milling.
(1) Influencing Factors in Part Machining
Several factors affect part machining:
– Mechanical Stiffness: Rigidity of the part during machining.
– Geometric Accuracy: Precision of the part’s shape.
– Tool Vibration: Vibrations during cutting that impact part quality.
– Tool Wear: Rate at which the tool deteriorates.
– Thermal Deformation: Effect of heat on the workpiece.
(2) Thermal Influence and Tool Interaction
In CNC milling, especially for thin-walled parts, thermal effects are significant. The heat from the tool causes thermal deformation, changing part dimensions. This is especially true for materials like aviation aluminum alloys, which are more prone to thermal effects and rebound compared to steel.
(3) Part Rebound and Its Impact on Accuracy
During cutting, the material’s properties may cause the part to rebound, reducing machining accuracy. This is more noticeable with large thin-walled parts. Aviation aluminum, with an elastic modulus of 70–73 MPa, is more likely to rebound than steel.
(4) Managing Rebound and Deformation in Machining
To reduce rebound and deformation, adjust cutting parameters based on material and part type. This includes selecting appropriate CNC milling settings and optimizing the clamping process. These adjustments help maintain accuracy and minimize deformation.
(5) Process Control for Minimizing Deformation
Controlling cutting force and clamping parameters is crucial to reduce deformation. Using auxiliary equipment improves stability during cutting. For large parts, start with roughing processes to handle higher cutting volumes, followed by finishing to meet tolerance requirements.
(6) Heat Treatment After Rough Machining
After rough machining, heat treat thin-walled parts to relieve residual stresses. This ensures part stability before the finishing process, where fine details are added, and final dimensions are achieved.
2. production tooling and machining sequences
When CNC cuts thin-walled parts, several factors influence the process, such as tool choice, material properties, and heat from cutting. Analyzing elastic-plastic changes in the tool and part material helps optimize results and reduce issues like thermal deformation and residual stress.
(1) Tool Selection and Material Considerations
Choosing the right cutting tool reduces friction-induced heat. Heat causes thermal deformation in both the tool and the part. Analyzing material properties and cutting forces helps control residual stress, improving part quality and performance.
(2) Residual Stress in Aluminum Alloy Thin-Walled Parts
For aluminum alloy thin-walled parts, keep residual stress thickness under 0.1 mm. Exceeding this limit causes deformation due to external forces. To avoid this, reduce the part thickness gradually during finishing. If the reduction exceeds 2 mm, carefully analyze residual stress.
(3) Tool Walking and Residual Stress Effects
In CNC milling, residual stress affects tool movement or “tool walking.” This can reduce machining precision and cause polythermal effects, where temperature changes lead to material expansion or contraction, harming part quality.
(4) Process Optimization for Stability
Analyze CNC milling factors like cutting parameters, tool types, and part stress states. Choose processing modes, such as small cutting or hierarchical processing, to stabilize the milling process, eliminate stress, and improve precision.
Example: Large Area Belly Plate Processing
Use a circular knife to process large belly plates in incremental levels. Monitor force changes during machining to keep the process smooth and reliable, maximizing workpiece effectiveness.
Preventing Sharp Turns and Stops
Avoid sharp stops or turns during tool movement. Control feed rate and use smooth arc transitions to reduce stress on the part and improve machining quality.
(5) Addressing Deformation and Process Efficiency
Follow a standardized CNC milling process to address deformation risks. Monitor the process carefully to maintain part quality and efficiency. Gradually refine the process to minimize the gap between design expectations and production results, preventing deformation and improving outcomes.
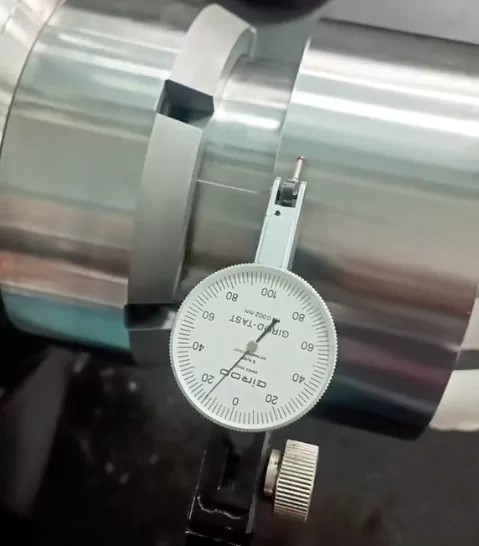
3. milling parameters
In CNC milling, selecting the correct cutting parameters is vital, especially for thin-walled parts. These parameters directly affect part accuracy, so choose them carefully.
(1) Cutting Force and Heat Effects on Thin-Walled Parts
CNC milling generates cutting forces and heat that impact thin-walled parts. Adjust tool material, part material, and CNC settings to manage these factors and prevent processing errors.
(2) Setting CNC Milling Dosage
Set CNC milling dosage based on the processing index. Ensure the design aligns with predicted results, considering factors like productivity, cost, and controllability.
(3) Balancing Programming and Production Conditions
Balance programming code with production conditions to boost efficiency and reduce tool wear. Clarify and optimize key parameters like tool selection, cutting speed, and feed rates.
(4) The Role of Workpiece Clamping
Clamping the workpiece correctly is crucial. Poor clamping can deform thin-walled parts, affecting accuracy.
(5) Clamping Process Considerations
When clamping the workpiece, analyze force changes and thermal deformation. Consider weak points in the part when positioning and clamping to minimize deformation and improve accuracy.
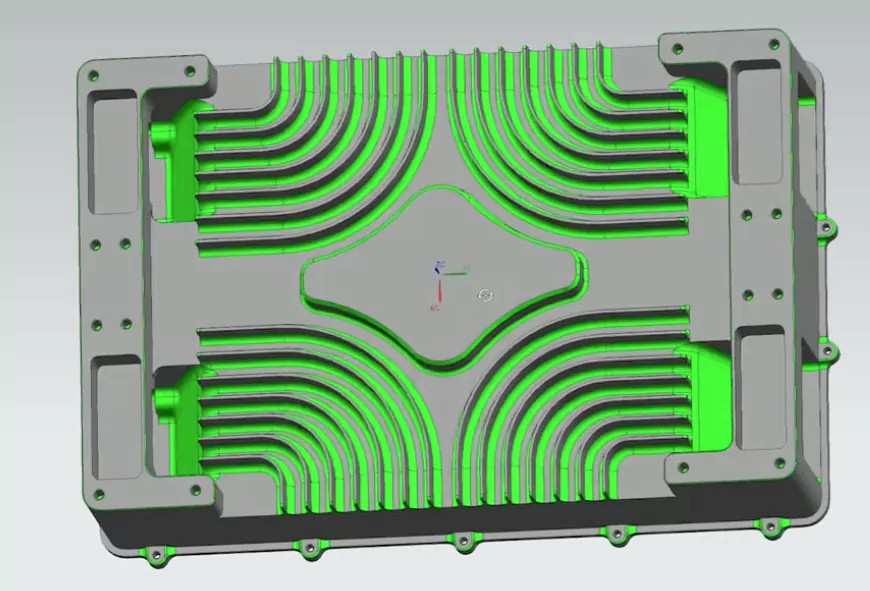
Conclusion
Thin-walled parts are increasingly used in aerospace, where their demanding environment requires high machining accuracy. Researching the cutting process optimization of these parts is both theoretically and practically important.
To ensure smooth processing of thin-walled parts, manage CNC milling deformation, and adjust processing routes. Integrate knife programs, increase rigidity, select CNC milling parameters scientifically, and reduce deformation risk with effective measures. This improves both the specific dimensions and overall processing results of thin-walled parts.
In the future, the industry should focus on technology and policy support, strengthen production refinement, and analyze the gap between domestic and foreign technologies. Detailed control and adjustments will help improve the quality of China’s industrial production.