Table of Contents
In modern manufacturing, fast and efficient prototyping is key to successful product development. Traditional methods are time-consuming, costly, and struggle to meet rapid market changes and personalized customer demands. Therefore, rapid prototyping technology has emerged. Innovative processes and equipment have shortened the cycle from design to physical objects, enhancing flexibility and precision.
What is rapid prototyping?
Rapid prototyping is a technology that uses computer-aided design (CAD) data to quickly manufacture physical models or prototypes. These technologies allow designers, engineers, and manufacturers to quickly verify concepts, test functionality, and optimize designs early in product development by turning digital designs into physical objects.
Rapid prototyping builds models layer by layer, reducing time and cost compared to traditional methods. It offers flexibility and efficiency in design and development, with applications in aerospace, medical devices, automotive, and consumer products.
What are the technologies for rapid prototyping?
1. Stereolithography (SLA)
Stereolithography (SLA) is an advanced additive manufacturing technology that uses lasers to solidify liquid photosensitive resins, creating complex 3D models and prototypes quickly. Its key advantages include high precision, fine detail display, and fast manufacturing speeds, speeding up product development and design verification.
SLA technology offers material diversity and wide applications across industries like medical, automotive, and consumer products, supporting innovation and production. Despite its high cost and size limitations, it remains a preferred rapid prototyping solution as technology advances.
2. Selective Laser Sintering (SLS)
Selective Laser Sintering (SLS) is an advanced additive manufacturing technology that uses lasers to sinter powder materials layer by layer to create complex 3D objects. Its advantages include material diversity, processing of thermoplastics and metal powders, minimal need for support structures, ability to create complex internal structures, and high-precision capabilities for fine surfaces and complex geometries.
SLS technology is widely used by industries such as aerospace, medical, automotive, and consumer products for rapid prototyping and small-batch production. Despite challenges in cost and speed, it remains a key technology for manufacturing complex parts and driving innovation in modern manufacturing.
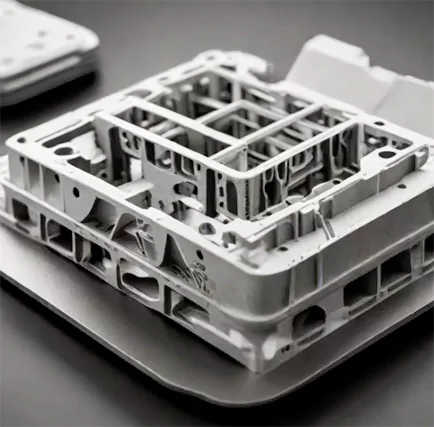
3. Fused Deposition Modeling (FDM)
Fused Deposition Modeling (FDM) is an additive manufacturing technology that creates 3D objects by extruding thermoplastic materials layer by layer. It’s popular for its simplicity, low cost, and suitability for rapid prototyping and small-batch production.
Its main advantages include material diversity, simple operation, strong adaptability, and the ability to produce simple to complex geometries. FDM may not match other high-end technologies in speed and surface quality, but it plays a key role in education, customization, and rapid prototyping, supporting innovation and product development across industries.
4. PolyJet printing
PolyJet printing is an advanced additive manufacturing technology that creates three-dimensional objects by jetting photocurable photopolymers. It features multi-material and multi-color printing for complex designs, high precision for fine surfaces and intricate geometries, and rapid prototyping for quick design verification and development.
PolyJet printing technology is widely used to verify product appearances, manufacture artworks, and create medical models, providing flexible and efficient solutions for design and production. Despite challenges in material selection and cost, it remains a key tool in modern manufacturing, driving innovation in product design.
5. Digital Light Processing (DLP)
Digital Light Processing (DLP) is an efficient light-curing method used in rapid prototyping and additive manufacturing. Unlike traditional light curing (e.g., SLA), DLP uses a digital light processor to cure the entire resin layer at once via a projector, which speeds up and enhances production efficiency. It is ideal for creating complex geometries and fine structures, making it widely used in jewelry design, dental models, artwork, and high-precision prototyping.
6. Direct Metal Laser Sintering (DMLS)
Direct Metal Laser Sintering (DMLS) is an advanced additive manufacturing technology that uses lasers to sinter metal powder layer by layer, creating complex metal parts and prototypes. Its advantages include high precision, complex geometries, fine surfaces, excellent material properties (strength, heat, and corrosion resistance), and adaptability for high-end industries like aerospace, medical, and automotive.
DMLS technology, despite challenges in equipment cost and speed, reduces material waste and post-processing through integrated manufacturing, offering an efficient and accurate solution for rapid prototyping and customized production. As technology advances, DMLS holds broad prospects for modern manufacturing, supporting the production of complex, high-performance parts.
7. Electron Beam Melting (EBM)
Electron Beam Melting (EBM) is an advanced metal additive manufacturing technology that uses high-energy electron beams to melt metal powders and build 3D parts layer by layer . Arcam AB in Sweden developed it, and the aerospace, medical, and automotive industries widely use it.
In the EBM process, an electron beam melts the metal powder in the powder bed. The platform lowers after each layer, and the system adds new powder to form a stacked structure e. This layer-by-layer stacking method can not only create complex geometric shapes but also realize the free design of internal structures.
Rapid CNC Machining
Rapid CNC Machining is an advanced manufacturing technology that uses computer control for efficient, high-precision part production. It is ideal for rapid prototyping and small batch production, with applications in aerospace, automotive, and medical industries. The core advantage of rapid CNC machining lies in its multi-axis linkage capability and adaptability to various materials. The high degree of automation reduces human intervention and improves production efficiency and product consistent y. Rapid CNC machining shortens production cycles, reduces costs, and drives modern manufacturing development.
Rapid Vacuum Casting
Rapid Vacuum Casting quickly produces high-precision prototypes and small-batch production parts. This process involves the use of silicone molds and vacuum pressure to inject materials such as polyurethane and epoxy resin. It offers benefits like high accuracy, excellent quality, fast turnaround, cost-efficiency, and a wide range of materials. This technique particularly suits product development, prototyping, small-scale production, medical devices, and consumer electronics.
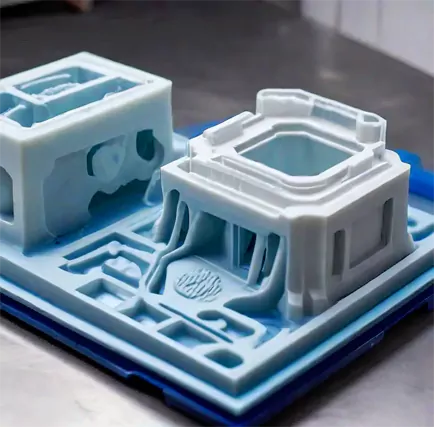
What is the difference between rapid prototyping and 3D printing?
Rapid prototyping and 3D printing are related but distinct. Rapid prototyping encompasses various technologies for quickly creating physical models from digital designs, while 3D printing is a specific technique within this field. Methods like SLA, SLS, and FDM accelerate design validation, testing, and market display by using different processes and materials, which helps reduce development time and costs.
3D printing is a specific rapid prototyping technology that builds three-dimensional objects by adding materials layer by layer. It offers various materials, including plastics, metals, and ceramics, enabling the creation of complex geometries and custom products. Compared with traditional subtractive manufacturing processes, 3D printing provides high design freedom and better material utilization. While 3D printing is ideal for small-batch production and prototyping, traditional rapid prototyping tends to be more cost-effective for large-scale production. Both technologies have unique advantages, and their combination better meets the needs of modern manufacturing.
Conclusion
Rapid prototyping technology has greatly transformed how companies develop products. Technologies like SLA, SLS, FDM, and DLP offer flexible prototyping options, speeding up design, reducing costs, and improving production efficiency. By choosing the most suitable prototyping process, companies can bring innovative products to market faster and maintain a competitive advantage. Rapid prototyping technology supports concept verification, functional testing, and small-batch production in modern manufacturing.