Two-color molding is a significant technological advancement that balances the needs of the customer with the protection of the environment.
With the continuous development of social civilization and improving people’s taste, product appearance, and visual effects are becoming increasingly important.
Traditional plastic products beautify the appearance of spraying, plating, and other treatment methods, but after a long time of exposure to the air, the appearance of the color is very easily destroyed.
The two-color mold can change the color of the plastic masterbatch according to different market needs, and there is no need for spraying.
The products produced by two-color molds are not only of stable quality but also of high production efficiency.
As the production of two-color molds requires high precision, the good or bad design of the mold structure is crucial.
Two-color injection molding process
The so-called two-color injection molding uses 2 or more 2 injection system injection machines, which will be different varieties and different colors of plastic simultaneously or successively injected into the mold forming method.
The two-color injection molding machine is different from ordinary injection machines in that, in addition to having two injection systems, it also requires a mechanism that enables the mold to rotate either the moving half (multi-mold – turntable type) or the cavity part (single-mold – rotary axis type).
The principle of two-color mold injection (Fig. 1): two-color molds usually have two pairs of molds, half of which are installed on the fixed plate of the two-color molding machine, i.e., the side with injection gates, and the other half is installed on the rotary plate of the moving half, i.e., the side where the mold is ejected.
The two pairs of molds are usually identical, while the primary and secondary fixed halves are different.
When the first material is injected, the fixed and moving half are opened under the tension of the injection molding machine, and the primary moving hale is rotated 180° with the primary product.
At this time, the moving half is not ejected. Then, the mold is closed for the second material to be injected, and after the heat preservation and cooling, the fixed and moving half are opened, and the product on the side of the moving half is ejected.
Each forming cycle will have one mold primary product and one mold secondary product.
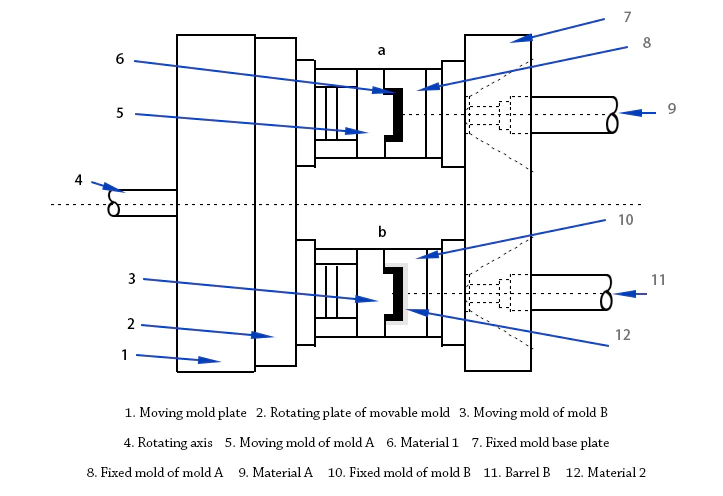
Mold design
Shrinkage Setting
Shrinkage rate is significant for plastic mold design, it is the basis of mold design, related to whether the product size is qualified or not, the shrinkage rate of different materials are different.
Different materials have different shrinkage rates. Only a suitable shrinkage rate can ensure the product reaches the required size after cooling.
The shrinkage rate of a two-color mold mainly depends on the shrinkage rate of the primary material, and the secondary material should be selected with the same shrinkage rate as the primary material.
For example, the primary material for ABS (shrinkage is usually 5 ‰), the secondary material for TPR (shrinkage is usually 18 ‰), in the two-color mold design, shrinkage should be set to all 5 ‰, because the primary material has basically formed the shape of the product’s contour, the secondary material wrapped in a product, and therefore will not have a larger or smaller shrinkage rate. One is the distinction between secondary, as shown in Figure 2.
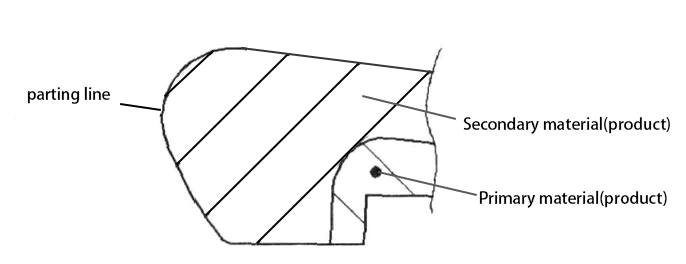
Division of primary and secondary products
When dividing primary and secondary products, several factors must be considered related to the success or failure of the whole mold design.
The first thing to consider is the fluidity of the material (it plays a significant role in choosing the right gate).
The second thing is to choose the right thickness of the product because the secondary product should be formed on the surface of the primary product; if the thickness of the meat is not enough, it will cause lousy fluidity, and it will quickly lead to the lack of material, shrinkage, and other undesirable conditions.
Generally speaking, the thickness of the secondary product should be half or more of the thickness of the whole product.
Selection of gate position
The selection of the gate position for a two-color mold is very important. It is better to use mold flow analysis software to analyze the gate position and check the fluidity in order to reduce the risk of mold failure.
In addition, it is necessary to change the shape of the primary product or increase the auxiliary casting position at appropriate places to improve the direction and speed of the secondary material flow.
When the secondary material adopts the side into the casting, the gate should be angled upwards, and try to increase the width of the gate should increase the fluid speed so that the fluid rushes upwards to the fixed half when feeding so that the primary material can be avoided to wash away, resulting in a product leakage and other phenomena.
Precautions for mold structure design
Inner mold design
The two fixed halves of a two-color mold have different shapes, each forming a different appearance.
In general, the shapes of the two moving halves are exactly the same. For one-time products, we prefer submerged gating so that the product can be cut off from the head automatically, and sometimes, we use a hot runner or three-platen molds.
In the first injection, after the mold is not ejected, then some of the material head will remain in the moving half core, so in the design of the second injection of the fixed-half core, to avoid the fixed-half core by the primary head scratches, the need to design the secondary fixed-half in the primary head of the part of the avoidance space, so that the mold in the second mold forming injection, the material head can be smooth into the avoidance space position.
Sometimes, the design to avoid the second fixed half core inserted (rub) injury to the first already formed product gate location can be designed pas art of the avoidance space, but must carefully consider the strength of each sealing gate location (the distance from the outer wall of the product to avoid space position), at least in 5mm above.
Pay attention to the fixed, moving half core, all inserted through, against the broken surface of the drop slope as significantly as possible, and four corners to do the pipe position, to facilitate the mold can be well coordinated.
The design of the primary fixed half core and the secondary insert broken in the case of ensuring the strength of the appropriate occupy avoidance space.
As shown in Figure 3: D take more than 0.2mm, this method to protect the secondary moving half core from being scratched.
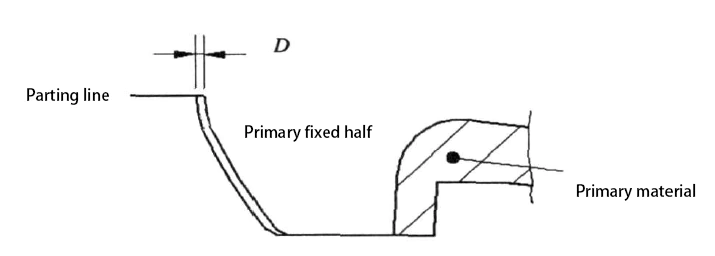
Mold blank design
The two fixed halves and two moving halves of the mold need to match each other completely, so when designing the mold core and the mold base, it should be indicated that the processing of the mold core and the mold base should adopt the number of the four sides to be divided in the middle;
The total thickness of the two fixed half parts should be equal;
4 guide pillar to the centre of symmetry (can not be used as a single color mold as the base angle guide pillar eccentric), and to ensure that the guide pillar and guide sleeve of the single side clearance tolerance in 0.025mm;
mold blank shape perpendicularity, parallelism, and flatness tolerance are guaranteed at 0 ~ +0.03mm.
The plane of the rotary disc of the moving half is shown in Figure 4.
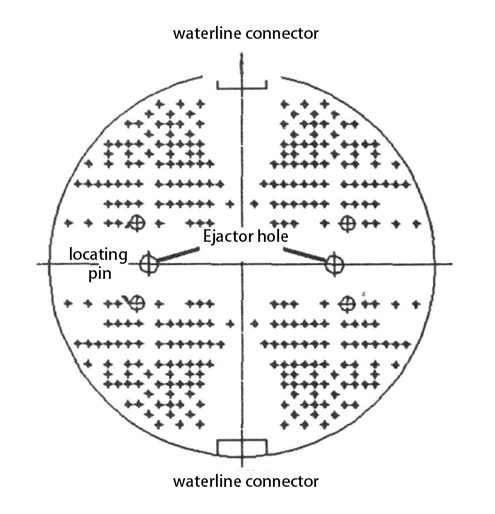
Mold positioning
The moving half must be rotated 180° after one injection to carry out the second injection.
Therefore, it is necessary to check whether the two corners of the moving half near the column on the injection molding machine will interfere with the four columns on the injection molding machine when it is rotated.
The gap between the two should be at least more than 10mm, if it is less than 10mm, it should be considered that the two corners of the mold near the guide column should be cut off.
Pay attention to the location and size of the positioning column of the rotary plate of the moving half, which requires the selection of different injection molding machines according to the size and stroke of the mold and the height of the mold and then according to the parameters of the injection molding machine to determine the location and size of the positioning column, as well as the gate, the positioning ring radius.
It is better to design a set of molds can be used in different types of injection molding machines, so that in the case of tight production tasks, flexible scheduling. The plane of the fixed-half base plate is shown in Fig. 5.
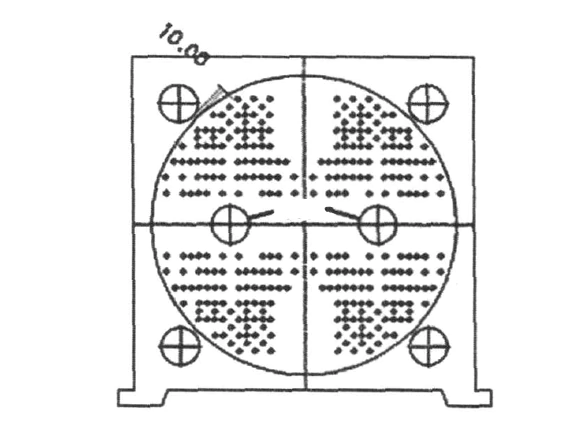
Cooling system
Two fixed half and two moving half-water distributions should be as complete as possible, balanced, and symmetrical.
The inlet and outlet water pipe joints of the mold should be on the upper and lower side as far as possible because if the water pipe joints are designed on the operation and anti-operation sides of the mold, it will be very inconvenient to install and operate the water pipe joints on the inner side.
Reasonable water transport design is very helpful for injection molding operations.
Common two-color mold structures
Teeter-totter structure
The seesaw structure is the two sides around the central axis; one side moves up, the other moves down, and so on.
The seesaw structure is mainly used to design keyboard molds with numbers and letters. Containing closed numbers or letters, such as 0, 4, 6, 8, A, B, D, O, etc., only the seesaw structure can the secondary material flow smoothly into the closed area, forming a beautiful appearance.
The working principle of the seesaw structure is: after one injection, the mold opens, the shutoff needle goes down under the action of the pusher, which makes the seesaw rotate around the rotating axis, and the shutoff ejector plate is ejected upwards under the push of the seesaw, so that the shutoff needle moves upwards, and shuts off a hole at the boundary of the closed area of the primary product.
Then, when the secondary injection mold is closed, the shut-off pin moves down by the action of the shut-off plate return pin to make a circular hole so that the secondary material can be drilled through the shut-off hole into the closed area (Fig. 6).
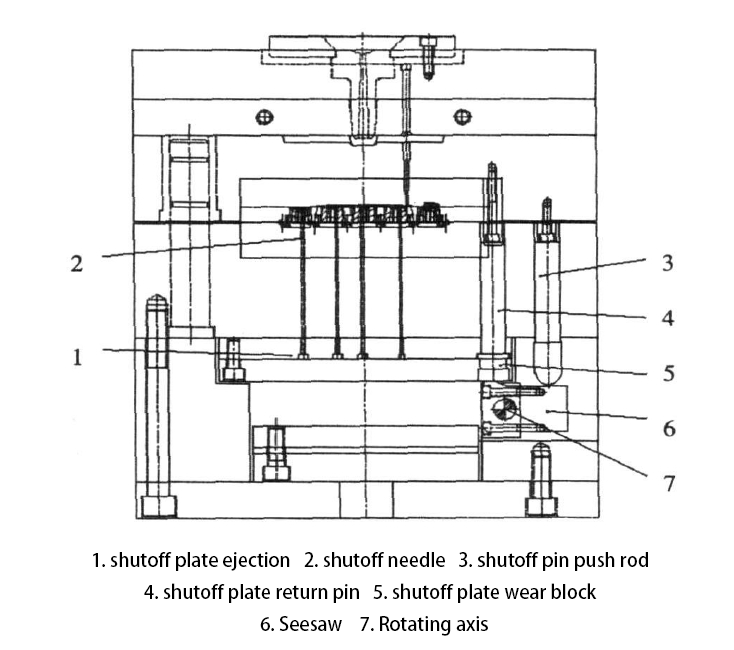
Structure of the center plate mold
In general, the two moving parts of a two-color mold are identical. However, if the product’s structure requires that the two moving halves are different and there is no need to use the side core pulling mechanism, then it is necessary to solve the problem by using the middle plate mold structure.
The working principle of the middle plate mold is: in the process of injection molding, the two pairs of moving halves do not rotate, after the injection machine completes the primary injection, the fixed moving half opens, firstly, the middle plate is ejected, and then the middle plate rotates by 180°, and then the mold is closed, and then the secondary injection is carried out. In this way, the inserts of the first and second parts of the center plate can be made into different shapes to achieve the expected design purpose. The structure is shown in Figure 7.
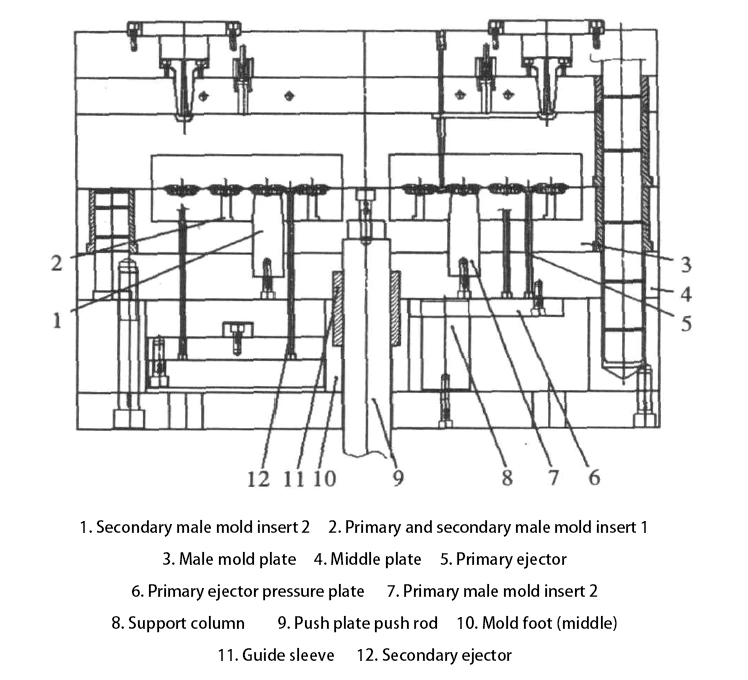
‘Twin’ structure
Two-color molds generally have two pairs of molds and also need two pairs of mold holders. Sometimes, once two similar products (symmetrical relationships or with the upper and lower cover, similar size) are formed in a set of mold frames to do two parts, we must use the ‘twin’ structure.
For ‘twin’ molds, since the same set of molds is designed with two different positions of the sprue location, this needs to be determined according to the position of the cylinder of the fixed plate of the injection molding machine selected.
The working principle of the ‘twin’ structure: the mold is designed as only one set of mold carriers, and according to the position of the barrel of the injection molding machine to determine the two feeding points, the mold carrier is divided into two parts, one for primary molding, and the other for secondary molding.
There are also two identical moving half cores and two different fixed half cores so that the primary and secondary molds are injected simultaneously, and only the part of the secondary molded product is ejected when ejecting.
A similar product is produced in one mold at a time (Fig. 8).
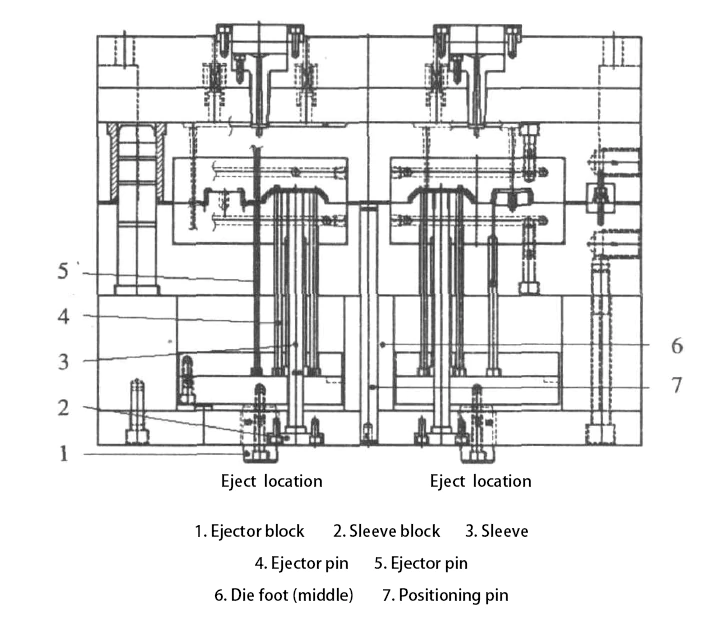
Conclusion
This paper introduces the problems to be paid attention to in the design of two-color molds, with three kinds of mold structure as an example, and briefly explains its forming principle.
The market prospect of two-color mold has a lot of room for development; with the continuous progress of the mold level, further improving the mold processing accuracy and reducing manufacturing costs, two-color mold technology will be widely developed and applied.