CNC machine tool processing offers high precision and stable quality in the processed parts, and also provides high productivity and adaptability. So CNC machining can significantly reduce workers’ labor intensity.
The program debugging no longer requires personnel intervention. CNC machines feature high automation, which supports modern management.
Therefore, one important sign of a manufacturing enterprise upgrading its equipment is the adoption of CNC technology.
However, the CNC machine tool crash accident lightly caused by the workpiece, tool damage, heavy loss of machine accuracy or machine tool damage.
In the work, operators, programmers and managers often because of small negligence and errors caused by the crash accident.
In this paper, through the case study, explains the CNC machine tool in the operation and other aspects of the prevention of accidental collision measures.
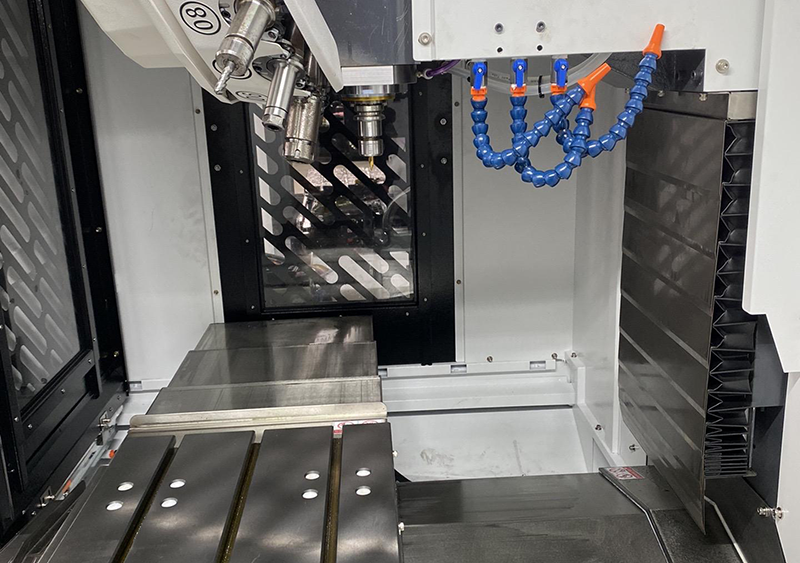
Machine operation management
1. Machine management
Example 1: A manufacturing enterprise produces couplings. One of the CNC milling machines is used for drilling holes on the circumference of the coupling.
During the processing of the first batch, the operator used a G95 feed per minute. However, the machine was not shut down.
In the afternoon, another operator used feed per revolution and did not write G94, but wrote F200 directly.
As a result, when running the programme, the tool’s rapid movement hit the workpiece, causing the drill bit to break.
Example 2: a worker in the CNC milling machine processing external contour, when the feed F = 300mm / min, must be adjusted to the multiplier switch to 10% below the knife, he thought it was a bad machine tool, after checking the original machine tool ‘empty run’ open.
Preventive measures:
CNC equipment should be assigned to trained operators. Only those who are qualified through training are allowed to operate the equipment.
It is strictly prohibited to adjust or modify the machine tool parameters unless properly trained. Non-operators are strictly prohibited from using the equipment.
When more than two people operate the same equipment, they must properly negotiate the handover of the workpiece.
There should be a record of the handover, including machine parameters and coordinate system data. It is strictly prohibited to change the equipment’s state without the operator’s consent.
2. Collision processing
An operator was operating a CNC lathe when the tool holder collided. The lathe turret’s positioning rat tooth disc was slightly misaligned due to the collision.
After resetting the machine, the operator continued processing. However, the operator concealed the issue and did not report it. As a result, the rat tooth disc suffered serious wear and tear and had to be scrapped.
There are operators repeatedly collision led to the formation of ball screw mother seat cracks, cracks gradually cracked and finally caused the ball screw vice scrap.
An operator in CNC turning, in order to facilitate the turning of long shafts, the chuck direction of the software limit cancelled and forgot to restore, resulting in another person in the turning tool impact on the chuck.
Some operators did not move the tailstock to a safe position when the machine was returning to zero, resulting in the bed saddle hitting the tailstock, toppling the tailstock backward and damaging the machine’s side cover.
More seriously, some operators in the machine tool tailstock is located in the middle of the guideway and is clamped under the state of zero operation, resulting in the tool holder hit the tailstock.
Another mistake is that the lathe is zeroed back to the Z direction first, while the X direction has not been returned, resulting in the tool holder hitting the top of the tailstock.
Preventive measures:
The above accidents show that the operator must report the accident and record the cause and result of the accident to the management;
the limit switches must be restored after cancellation and hand-cranked to check whether the limit switches are in the correct position;
the lathe must return to the X direction and then return to the Z direction during zero return operation; the milling machine must return to the Z direction first.
As an enterprise management personnel should not let go of the minor collision accidents, each accident are carefully analysed, and systematically summarized and recorded in the archives.
And organise the workers to study in the morning meeting every day, and assess the workers on a regular basis. Ensure that accidents that have occurred and accidents that may occur no longer occur.
3. Barbaric operation of machine tool
operators in the operation of machine tools, in order to improve efficiency, increase the amount of cutting, resulting in machine tool boring.
A CNC milling machine operator in the tool change, did not wipe the tool shank clean, mounted after strong cutting, resulting in the spindle bore was pulled bad.
A CNC milling machine operator was installing an end milling cutter spigot. However, the operator did not tighten the spigot properly. When mounted on the machine, the milling cutter could not be automatically clamped.
Due to the large cutting force of the end milling cutter, it caused the cutter to spin in the spindle. This led to the spindle taper holes being damaged.
A machining centre, the tool magazine has been a failure, the transposition is not right, but the operator is still repeatedly change the knife, resulting in the bucket type tool magazine is broken.
Preventive measures:
Enterprises should limit the cutting amount for each CNC machine. The operation of machine tools and tools should be standardized.
Barbaric operation of machine tools should be prevented through repeated training. Operators should be organized to learn proper procedures to avoid damaging the machine tools.
Clamping reasons
1. Soft jaw clamping
generally used on CNC lathes three-jaw chuck, but the high precision parts of many soft jaw clamping workpiece.
Soft jaw by many times after the clamping jaws gradually appeared flared, such as not timely repair will make the workpiece in the processing of the force out of the seriousness of the equipment caused by major accidents and safety accidents.
An operator was using soft jaw clamping during the finishing process. Due to wear on the soft jaw, the workpiece flew out of the jaws. The workpiece became clamped between the chuck and the disc, causing damage to two CNC lathes.
One CNC lathe suffered damage to its ball screws, nuts, and slide base, which were scrapped. The other CNC lathe had its ball screws, linear guides, and nuts scrapped. The seat of the turret on both machines was also damaged to varying degrees.
Preventive measures:
When the soft claw is clamped for cutting, attention should be paid to the clamping position and shape of the soft claw.
After the soft claw is shaped, it should be checked to see whether the clamping parts are secure and whether the clamping force is appropriate. It is necessary to carry out frequent inspections to prevent the soft claw from wearing out.
2. Three-jaw or four-jaw clamping
three-jaw or four-jaw chuck in the clamping generally do not have problems, only when the clamping length is less than 8mm or so, and the workpiece is longer, turning is easy to knock down the workpiece, resulting in tool damage.
3. Top clamping
When clamping the workpiece with chuck and top at the same time, attention should be paid to the weight of the workpiece, the shape and size of the centre hole and the top tightening force.
The diameter of the centre hole processed by a worker is 6.3mm, he did not find a suitable centre drill and replaced it with one of 2.5mm diameter.
When increasing the load of cutting, the top was damaged due to the heavy weight of the workpiece and the small centre hole, which caused the workpiece to fly out.
Therefore, special attention should be paid to the size of the top hole, strictly according to the drawing processing.
In addition, a clamping a top clamping, back to ensure that a reasonable distance from the Z back to the best X first back to a safe position and then back a little distance from the Z direction.
Many operators due to Z distance back more, resulting in the tool holder hit the tailstock, or tool change hit the top.
4. CNC turning irregular parts
in the CNC lathe processing irregular parts should pay attention to the problem of counterweight. Some operators think that just processing a few pieces, the accuracy of the machine tool does not have much impact on the weight.
In fact, eccentric parts have a very big impact on the accuracy of spindle bearings of CNC machine tools. In the absence of counterweight, do not easily turn eccentric parts on CNC lathes.
Operator responsibility reasons
1. Programmes in the tool change problem of
a worker in the processing of a roll parts, the use of machine tools for the CK6150, processing workpiece diameter of 400mm, horizontal 6-station tool holder.
When the manual tool change error in estimation, the tool transposition hit the workpiece, resulting in the tool holder can not be set.
A worker installs a long boring tool, because the tool extends longer, in the tool change, although the attention did not hit the tailstock, but the tool transposition hit the sliding door of the machine cover, resulting in deformation and damage to the sliding door.
A worker installed on the lathe cut off the knife, because the cut off the lower part of the knife fish belly out too much, and cut off the knife and long, the lower part of the tool hit the motor guard and motor.
Preventive measures:
long shaft large diameter parts when changing tools, the location of the tool should be carefully measured, not arbitrary.
Long tool installation to prevent the transposition of the machine tool, workpiece, etc., to be repeatedly checked before not transposed.
2. Did not pay attention to the blank size of
An enterprise was processing a wheel using the CK5116 machine tool. The front of the blank could be cut normally, but one of the blanks was too large. The workers did not measure or check the size.
They directly clamped and processed the workpiece. During the rapid positioning stage before cutting, the tool hit the workpiece. As a result, the rotating workpiece fell off and flew out.
A worker was processing a batch of flange parts. The blanks were made of round steel and were cut using a sawing machine.
After the undercutting, the worker clamped the workpiece with a three-jaw chuck for processing. Everything went smoothly at first.
However, one blank had a significantly skewed end face. The cutting had excessively large margins, which caused boring. As a result, the blade was damaged.
Preventive measures:
Blanks in the management, the size of the workers will be classified by the classification of good, the same size blanks together, requiring workers in the clamping blanks must be carefully measured.
In addition to gas cutting, forging blanks may have a larger burr, this time it is more important to measure, modify the procedure before processing.
The operator should measure whether the blank under the sawmill is too long or whether the end face is skewed to prevent hitting the knife or crashing the machine tool.
Additionally, the first piece of machining should be done in a single-stage processing mode. The multiplier switch should be used to control the tool’s feed rate.
If any abnormalities are found, the multiplier switch should be adjusted to 0 immediately. Alternatively, the emergency stop button can be pressed.
After making sure that the programme and parameters are correct, you can choose automatic machining.
3. Tooling error in
In general, the machine tool is not at fault. However, some operators make mistakes during lathe tooling. For example, the value for the tool patch is written inside the No. 1 tool patch, but the adjustment is made on a different tool patch.
If No. 1 tool patch is supposed to be entered as T0101, but the operator writes it in the No. 2 tool patch, a problem will occur.
CNC milling machine programming with the coordinate system is G54, but the value of the tool complement is written in G55, which may appear after the start of the machine tool directly to the workpiece and fixture, resulting in accidents.
Preventive measures:
The operator must be careful and conscientious when setting the tool, and must check whether the value of the tool complement is correct and whether the position of the tool complement is correct before machining.
4. Call program error
program call, to ensure that the call program name is the program to be processed.
Generally, FANUC, Huazhong, and other systems will not have issues when calling the program. However, in the Siemens system, when calling a parts program, the process must include selecting and then opening the program.
The name of the selected program will be displayed in the upper right corner of the screen during processing.
Preventive measures:
call the programme to see carefully whether the programme to be processed.
5. CNC milling machines and machining centres Z-axis value test
A typical issue with CNC milling machines and machining centers is the Z coordinate problem. Most CNC machine tools have a graphical verification function.
However, this function is usually limited to two-dimensional graphical verification. Even if a three-dimensional display is available, it is still impossible to determine the exact value of the Z coordinate.
Therefore, we can not assume that the graphics are correct program correctly, you need to test the Z-axis value to avoid accidents.
Such as an operator in the programme Z value of 100, written as -100, plane graphics verification is correct, but caused the entire tool into the workpiece inside.
For CNC lathes should also be set up to detect a fixed point, so that the tool first run to the point to visually check the approximate distance between the correct or not. If the tool runs to the centre of the workpiece X = diameter +10, Z = 50mm.
Preventive measures:
Pay attention to the values of the workpiece coordinate system and the remaining values on the operating panel when starting machining.
To set a visual safety point in order to check whether the tool position is correct or not.
To develop good operating habits, when starting rapid movement in the Z direction, be sure to turn down the multiplier switch before moving, and increase the multiplier only after confirming that there is no error.
Problems with Input Programmes, etc.
1. Errors in Manual Input of Numerical Values
When manually inputting a programme, an error in inputting a numerical value, e.g., writing 100 as 1000, may result in a major accident.
2. Switching between G00 and G01 during programming
When switching between fast forward and cutting feed, do not omit the G01 instruction so that the tool does not hit the workpiece at the speed of G0 and cause an accident. Beginners are most likely to make this mistake.
3. Cursor position
when processing the cursor must be returned to the beginning of the programme to establish the workpiece coordinate system, if the coordinate system is not established, it is easy to hit the knife phenomenon.
In particular, when executing the “specified line run”, the workpiece coordinate system must be established, otherwise it is very easy to hit the tool.
For the following procedure, if the thread is to be processed again, the cursor will be jumped to line N60 or N70, because there is no adjustment of T0202, it is still the value of the last tool patch, resulting in tool collision.
O001
N10 T0101 M3 S1000 F120
N20 G98 G0 X50 Z3
N30 G1 X42Z-34
N40 G0 X50 Z100
N50 T0202
N60 G0X40 Z3
N70 G92 X29 Z-30 F2
So manual programming is best through the simulation software simulation, such as no simulation software must be verified by the programme on the machine tool.
Of course, it is best to use software simulation to solve the problem, it should be said that as long as the simulation is correct, the tool is correctly aligned with the knife will rarely hit the knife accident.
4. Machine instructions are not familiar with
For example, machine tools can return to the mechanical origin while canceling the tool length compensation procedure with G91 G28 Z0.
This procedure, in its true meaning, involves returning to the mechanical origin through an intermediate point. The intermediate point uses an incremental movement distance to specify the way back.
At this moment, the intermediate point and the spindle of the machine tool are actually located at the same position. In other words, the Z axis directly returns to the home position.
If G90 G28 Z0 is used, the machine can also return to the mechanical origin. However, the intermediate point in this case is the Z origin of the current workpiece coordinate system.
Since the Z origin of the workpiece coordinate system is usually set at a very low position, this method is very likely to cause a crash.
Conclusion
In summary, there are many reasons for machine tool crashes. However, if the operator skillfully understands the machine tool and operates it carefully, crashes can be avoided.
It’s important for the operator to understand the programming instructions and pay attention to simulation and calibration.
With proper enterprise management and a focus on accident prevention, crashes can be minimized. By learning from past incidents, CNC machine tools can avoid crashes.
The most important thing for the enterprise is to analyze any machine crash accidents. A designated person must investigate the cause of the accident.
The equipment management considerations should be filled out, and workers should receive publicity and education. This ensures that the same mistake is not made again in the future.