Table of Contents
Add a header to begin generating the table of contents
Rapid prototyping technology is a new comprehensive manufacturing technology involving multiple disciplines, including arc spraying.
The light-curing molding method (StereoLithography Apparatus, abbreviated as SLA) is the earliest rapid prototyping manufacturing process application.
It has a high level of maturity and, after standing the test of time, can manufacture complex shape structures, prototypes, and molds that are difficult to shape using traditional methods.
Integrating rapid prototyping and arc spraying gives us the arc spraying rapid molding technology.
This rapid molding technology uses the principle of replication. It has the features of simple operation, short mold manufacturing cycle, low molding cost, etc., which makes it very suitable for the development of small batches and new products.
The article focuses on the research of the SLA prototype as a master model, with a low melting point of zinc-aluminum alloy arc spraying and a rapid tooling manufacturing process.
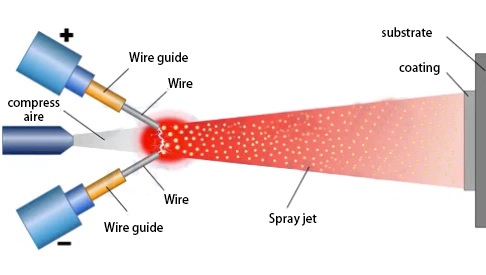
Key technologies
The technology uses an arc spraying gun, connecting two special mold-making wires to the positive and negative poles of the DC power supply as self-consuming electrodes.
The arc discharge melts the end of the wire, and high-speed, high-pressure compressed air atomizes the molten metal into particles, spraying them onto the surface of the mother mold at a very high speed.
Curing layer by layer forms a high-quality metal coating of a certain thickness that is smooth, dense, and low in porosity. This coating serves as the mold’s metal shell.
The inner wall of the metal shell fits perfectly on the surface of the master mold, thus forming the required mold cavity.
The Arc spraying fast mold manufacturing process: the mother mold preparation; mother mold surface pre-treatment; arc spraying manufacturing mold metal shell; backing material filling; demolding, trimming, and polishing; and other post-processing procedures, as shown in Figure 1.
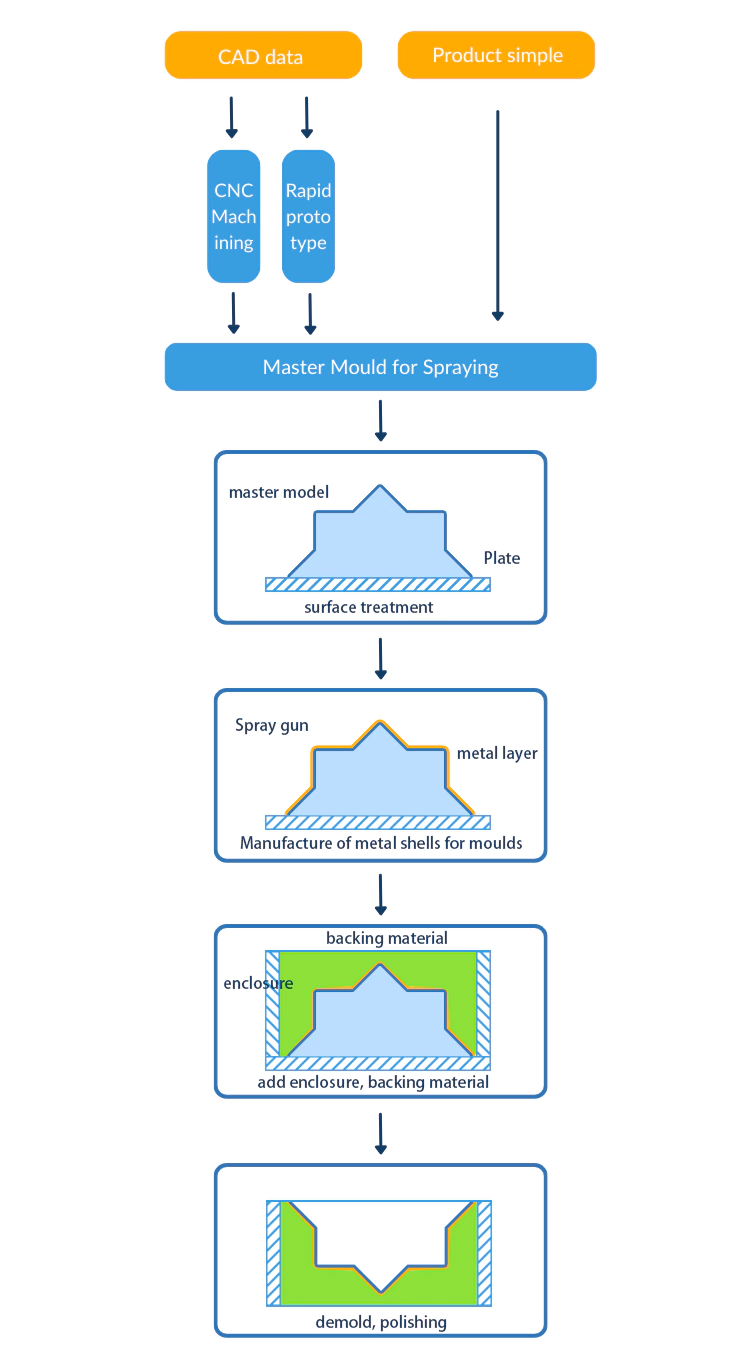
1. Preparation of the mother mold
The system converts the part’s CAD model into STL format files, determines the orientation placement, adds support, and slices the layering process.
In the light-curing rapid prototyping machine for molding, cleaning model, removing and trim support, and post-curing treatment to get the SLA prototype.
The SLA prototype is a thin shell with a wall thickness of 2mm.
Due to its low strength and ease of deformation, the material cannot directly serve as a master mold for spraying and requires strengthening.
It is common to use gypsum with a water-plaster ratio of about 0.5 to fill and strengthen the back of the SLA prototype.
After the plaster solidifies, screws connect the edge of the SLA prototype to the wooden board, increasing deformation resistance and creating the mother mold for spraying.
2. Pre-treatment of the surface of the mother mold
The relationship between the roughness of the surface of the mother mold and the bonding strength of the metal coating is:
If the roughness is too high, it improves the bonding strength between the metal coating and the substrate but reduces its surface quality.
If the roughness is too small, the bonding strength is insufficient, and the metal coating is easy to flake off.
Therefore, to guarantee the bonding strength, you should minimize the roughness to obtain a good shell surface quality.
Experiments have verified that the metal coating surface quality and bonding strength improve when you grind the mother mold surface with sandpaper or an iron brush to achieve a surface roughness of 10 to 15 microns.
3. Arc spraying manufacturing mold metal shells
When preparing the coating, you must strictly control the temperature of the metal coating. If the temperature gets too high, it will deform the surface of the resin master model, ultimately reducing the precision of the mold surface produced.
Optimizing the process parameters, adjusting the scanning process, and intermittent spraying can solve the problem of high metal coating temperature.
The parameters of the arc spraying process are spraying voltage, current, wire feed voltage, spraying air pressure, spraying distance, spraying angle, gun movement speed, and wire feed speed.
To obtain high-quality mold cavities, you need to precisely control all the above parameters.
Through experiments, the best-optimized spraying process parameters for spraying zinc-aluminum alloy on the surface of SLA prototypes (wire diameter φ2mm) are shown in Table 1.
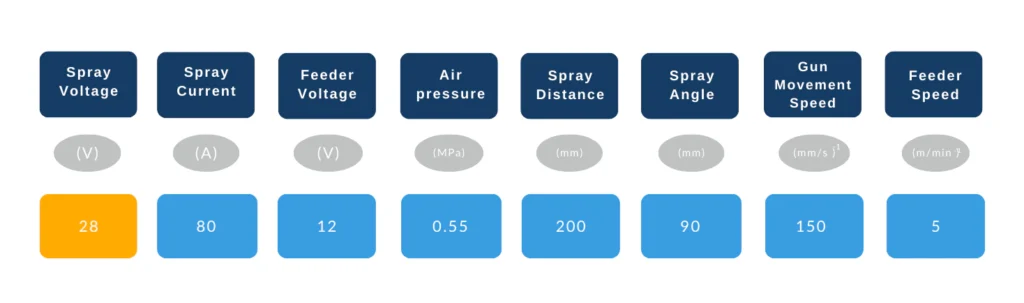
The RT-ARR10 robot coating system automatically completes the arc spraying process, which consists of the robot body MOTOMAN-HP20 and the control cabinet DX100.
The spraying method adopts intermittent spraying.
4. Filling backing material
The metal coating is the mold’s working surface, and the backing material determines its strength.
You position the pre-welded frame with a steel plate on the coated shell, and to avoid the backing material from flowing out when pouring, you apply plaster to seal the gap between the frame and the coating.
Mix epoxy resin and curing agent at a 3:1 ratio, then uniformly cast the mixture into the frame, layering it with glass fiber at intervals for reinforcement.
5. Demolding and post-processing
First, remove the board behind the mother mold to prevent heat from deforming the resin parts easily.
Good demolding performance: just put the mold into the water, heated to 60 ~ 70 ° C, and keep it warm for some time; the SLA prototype is soft, and with a little external force, you can successfully de-mold it.
Then, we post-process the molds by polishing and dating.
Finally, the large mold frame welding installation and transport with the auxiliary structure completed the rapid mold manufacturing.
Conclusion
This paper describes the process’s following characteristics, using SLA prototype technology and metal arc spraying technology to achieve rapid mold making.
Impact of SLA Prototype Quality on Rapid Mold Production
(1) The quality of the SLA prototype directly restricts the quality of the rapid mold and its products. The current SLA technology is mature and guarantees high precision and rapid mold production.
Optimizing Metal Arc Spraying Process to Reduce Internal Stress
(2) The process parameters of the metal arc spraying process on the coating of the internal stress of the complex mechanism should be reasonable to improve the spraying process and reduce the residual internal stress of the metal coating to improve the forming accuracy of the rapid mold.
Reproducibility of Arc Spraying in Reflecting Mother Mold Details
(3) Arc spraying has good reproducibility and can genuinely reflect the details of the mother mold.
Comparison of Manufacturing Cycle and Cost Between Rapid and Traditional Molds
(4) Compared with the traditional machined steel mold, the manufacturing cycle is 1/4~1/5 of the latter, and the cost is about 1/10.
Sources of Error in Rapid Mold Making Using SLA Prototype and Arc Spraying
(5) After experimental analysis, the error in the rapid mold-making process of arc spraying based on the SLA prototype comes from two aspects: first, the error in preparing the SLA prototype, and second, the error due to the deformation of the mother mold during the spraying process.
Due to the constraints of the SLA prototype’s heat resistance and the low melting point of the spraying material, manufacturers mostly use the arc spraying rapid molding process based on the SLA prototype for small batch production.
It provides strong technical support for the rapid development of new products.
In the future, the development direction of arc spraying rapid mold-making technology is to study the molding process of higher hardness materials and improve the service life of molds.
RuiYi has provided rapid prototyping services for many years, delivering high-quality and efficient solutions to meet clients’ diverse needs across various industries.
With extensive experience and a strong commitment to innovation, RuiYi consistently supports businesses in bringing their ideas to life through advanced technologies such as CNC machining, 3D printing, and vacuum casting.