Table of Contents
Hole opening technology is an important part of sheet metal processing to ensure the quality of processed parts. Especially in sheet metal bending, the reasonable design and use of process holes can not only reduce the problems of material stretching and deformation but also improve the precision and welding quality after bending. This article will detail the role of sheet metal process holes, design principles, and how to choose the right type of hole according to different sheet metal thicknesses and shapes.
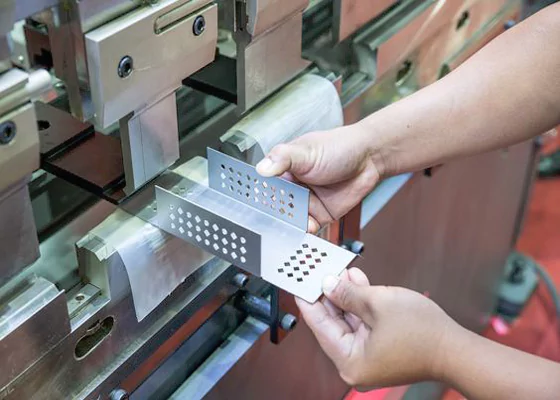
The Role of Sheet Metal Process Hole
Sheet metal processes open holes at specific locations to improve or assist subsequent steps, especially in bending.In the sheet metal bending process, opening holes mainly play the following roles:
1. Prevent material stretching and deformation
During bending, the sheet metal edges experience significant tensile forces, especially near the bending line or edges. Without a suitable process hole, bending causes tensile deformation, thinning the material at the edge and potentially causing tears.
Process holes help to disperse the stress and avoid this stretching phenomenon by opening holes near the bending line.
2. Improvement of bending quality
Process holes make sheet metal bend more smoothly, especially at the bending portion. The correct location and size of the hole can reduce the uneven deformation of the material due to the stress generated during the bending process, and ensure accurate angles and neat edges after bending.
3. Reduce welding difficulty
Without a process hole in the bending of certain sheet metal parts, the bent edges can thin out. This requires more welding material, increasing waste and causing potential welding deformation. Reasonable design of process holes to maintain the original thickness of the material can reduce the need for filler when welding, thus improving welding quality.

Analysis of the advantages and disadvantages of opening and not opening holes
1. Disadvantages of not opening the process hole:
(1) Material Loss
During the bending process of sheet metal parts without open holes, the material will suffer greater stretching and deformation near the bending line, resulting in a reduction of the material thickness in the corner part, which affects the strength and stability of the final product.
(2) Welding Defects
The thin edge material requires more filler material for welding. Excess filler material can cause deformation, uneven welds, and affect the product’s appearance.
2. The benefits of opening process holes:
(1) Ensure the precision of bending
The process hole helps the uniform distribution of stress in the bending process, reduces the overstretching of the material, and ensures precision after bending, especially in the bending of complex shapes or large angles.
(2) Reduce welding pressure
After opening the hole, the thickness of the material in the bending part remains unchanged, reducing the need for filling when welding, making the welding process more stable, avoiding welding deformation, and improving welding quality.
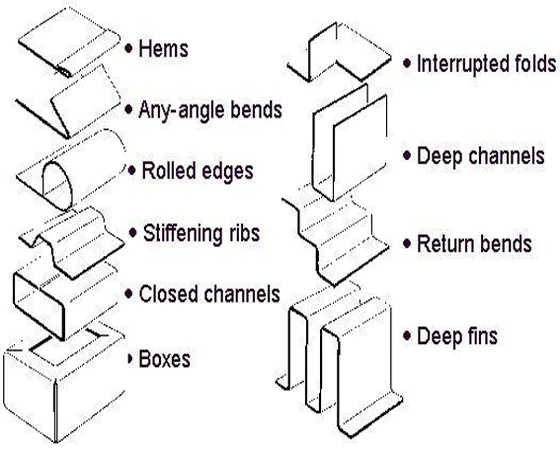
Shape and size selection of process holes
In sheet metal processing, the shape and size design of process holes is crucial. Choosing the right hole shape and size not only improves processing efficiency but also ensures bending quality.
1. Common Hole Shapes
(1) Round Hole
Round holes are the most common type of process holes. Its advantages are less material removal, better appearance after molding, and easier processing. For most sheet metal parts, round process holes provide more desirable results.
(2) Square or Long Holes
Special process requirements or larger punching tools typically require square or long holes to accommodate bigger sizes. However, square holes are relatively difficult to process and remove more material than round holes, making them less economical.
2. Selection of process hole size
(1) cold rolled sheet
For common cold rolled sheet metal, design the hole diameter to be 1.5 to 2 times the plate thickness.
For example, with a 2mm thick plate, choose a hole diameter of 3mm to 4mm to prevent deformation during bending and avoid weakening the plate.
(2) Thin plate
For plates thinner than 1.0 mm, it is usually not recommended to open the process hole due to limitations. This is because thin plates are susceptible to large deformations during bending and process holes will further weaken the plate.
(3) Distance between the hole and bending line
The distance between the process hole and the bending line must be large enough. Generally speaking, the distance between the edge of the hole and the bending line should be at least 3 times the thickness of the material, to effectively avoid deformation of the hole in the bending.
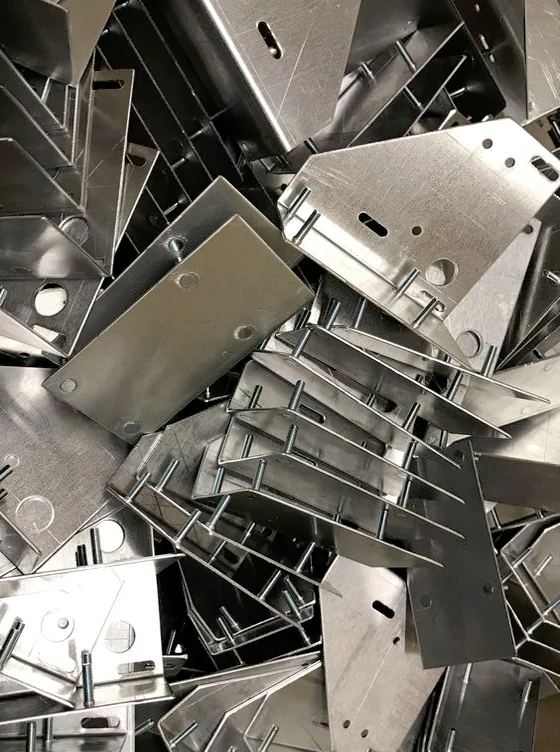
Special circumstances and design considerations
1. Hole location and bending angle
In some special cases, the design of the process hole needs to consider the bending angle and the specific shape of the sheet metal. When the process hole intersects two bending lines, increase the hole diameter, typically twice the sheet metal thickness.This ensures that when bending, the hole will not affect the strength of the material and bending accuracy.
2. Bending sheet metal thick plate process hole design
When the sheet metal part is thick (e.g. thick plate or steel plate), the design of the process hole must take into account the effect of rounding of the material during the bending process. In this case, you may need to increase the process hole size to accommodate pressure and bending angles during bending.
Experience Sharing by Rui-Yi Sheet Metal Processing Factory
RuiYi Sheet Metal Processing Factory is a leading sheet metal processing company in the industry, specializing in providing high-precision sheet metal processing, CNC processing, 3D printing, and other services. With more than 10 years of industry experience, Ruiyi Sheet Metal Processing Factory has accumulated rich experience in process design, especially in bending and welding, through the rational design of process holes, which significantly improves production efficiency, reduces material waste, and provides customers with stable, high-quality sheet metal processing solutions.

Summary and Recommendations
Designing process holes in sheet metal is a crucial part of sheet metal processing that must not be overlooked.Through reasonable design of process holes, not only can we improve the quality of bending and welding, but also effectively reduce production costs. The design needs to give full consideration to the thickness of the sheet, the location of the holes, the size of the holes, and the distance between the holes and the bending line to ensure the quality and stability of the final product. In the sheet metal processing industry, only by mastering these key technologies can we produce sheet metal parts that meet high standards.
Why is hole opening technology important in sheet metal bending?
It helps reduce material stretching and deformation, ensuring better dimensional accuracy and maintaining the structural integrity of the part during bending.
What are process holes, and how are they used in sheet metal processing?
Process holes are deliberately designed openings that aid in manufacturing by relieving material stress, guiding alignment, and improving welding quality.
How do process holes improve the welding quality of sheet metal parts?
They allow for better alignment, reduce warping, and provide access points for consistent welding, resulting in stronger and more accurate welds.
What are the common methods for creating holes in sheet metal?
Techniques include punching, laser cutting, drilling, and waterjet cutting, depending on the material and precision requirements.
What materials can be used in hole opening technology?
Hole opening can be performed on various materials like aluminum, stainless steel, carbon steel, and other alloys commonly used in sheet metal processing.
How does hole placement affect the bending process?
Properly placed holes relieve stress during bending, prevent cracking or tearing, and ensure uniform bends without material distortion.
What factors should be considered in designing process holes?
Factors include hole size, shape, placement, material type, bending angle, and overall part design to ensure functionality and manufacturability.