Table of Contents
The CD is the abbreviation of codevision in English. A precision CD texturing machine treats metal surfaces to create an effect similar to that of a CD. CD pattern alias: Sun pattern, smooth surface pattern, colorful pattern; the product effect of CD pattern processing: under the sun, it will emit several rays of light along the center point.
CD pattern is a kind of metal surface treatment technology. Compared with other instrument processing, CD pattern processing is a more complex fine process.
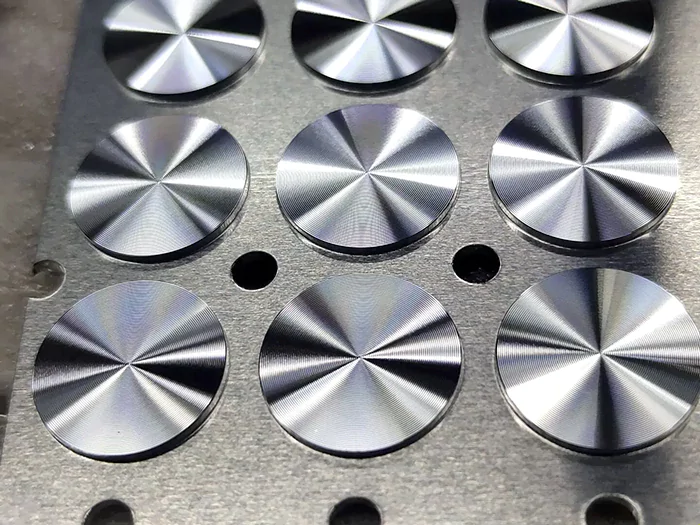
CD pattern
So, where can CD pattern processing be applied?
You can use CD pattern processing on various materials, including hardware, aluminum, copper, mobile phone cases, nameplates, and other surfaces, to create a high-end texture on the metal surface.
Because CD pattern processing is an advanced surface treatment process, there should be a specific processing scheme:
First,use a high-precision CD pattern machine. In the process of CD pattern processing, an advanced machine is the premise to produce qualified and satisfactory products, which can produce successful works.
Second, choose a reasonable, safe, and effective processing method. The CD pattern processing is a high-grade technology, and every step must be executed flawlessly to ensure its success.
Third, the operator should have rich experience. A skilled worker with rich experience is the key to the success of CD pattern processing. In modern society, processing has become the central point of the machinery industry and industry.
There are many processing products. Everything can be used for processing. We encounter the processed products in our daily lives. Equipment and facilities, whether rough, fine, tiny, or huge, can all be processed.

CD texturing machine
So why is there a CD pattern processing?
With the acceleration of people’s life rhythm, the days become richer and richer, in all aspects of life began to pursue a better side, it is in this way that the development of the CD pattern processing industry, which is a high-end metal surface treatment process, so there is a market and demand to drive the development of this industry. In the future, people will also pursue a more advanced way of life, and a variety of advanced processing methods will also appear.
We often see digital products processed with a CD pattern, such as the CD grain knob, which polishes the mobile phone shell to a shine. While some may think the surface treatment process of the CD pattern is simple or effective after seeing a workpiece with the pattern, it is actually difficult to execute well in practice.After many times of sample making, it can’t succeed.

CD pattern
So why CD pattern treatment is difficult?
Because there are technical skills in this, that is to say, to do a good job in the CD surface treatment process is the need for a certain technical content.
1. High Precision Requirements:
CD pattern treatment often demands extremely tight tolerances, sometimes in the micrometer or even nanometer range. Achieving such precision requires advanced machinery, careful control, and skilled technicians to minimize errors.
2. Complex Design Specifications:
Many CD patterns have intricate or detailed designs, which can be difficult to reproduce accurately. Complex geometries or patterns increase the chances of deviations, making it challenging to maintain consistent quality.
3. Environmental Sensitivity:
CD pattern treatment is highly sensitive to environmental conditions like temperature, humidity, and dust. Even minor fluctuations can lead to material expansion or contraction, causing distortions or misalignments in the pattern.
4. Material Constraints:
Different materials have different responses to treatment processes. For instance, metals, plastics, and silicon wafers react differently to temperature and stress, which can complicate treatment, especially for applications requiring high durability or stability.
5. Equipment Limitations:
High-precision equipment is costly and may require frequent calibration and maintenance. Even with advanced machinery, limitations in the tool’s resolution, speed, or capability can impact the quality of the treatment.
6. Wear and Tear on Tools:
Processing delicate or high-precision patterns can lead to rapid tool wear, affecting the pattern quality. Frequent tool changes and maintenance can also increase downtime and costs.
7. Data Integrity and Complexity:
Errors in the coordinate data can lead to misaligned or flawed patterns. Furthermore, converting complex CAD data into executable commands for machinery requires advanced software and can introduce errors if not carefully managed.
8. Real-Time Monitoring Needs:
Maintaining quality often requires real-time monitoring and adjustments. Detecting deviations and correcting them during processing is difficult, requiring sophisticated systems that can quickly and accurately respond to changes.
9. Skilled Labor Requirements:
Due to the complexity and precision required, CD pattern treatment demands skilled operators with expertise in both the equipment and process. A lack of skilled personnel can make it challenging to achieve consistent, high-quality results.
10. Quality Control Complexity:
Verifying the quality of each pattern can be time-consuming and difficult, particularly at a microscopic level. You often need expensive inspection tools, such as coordinate measuring machines (CMM) or electron microscopes, which also require specialized knowledge.
Features of CD pattern processing
Let’s talk about the features of CD pattern processing.
1. Precision and Accuracy:
CD pattern processing ensures high precision by using coordinate data for exact pattern creation, which is crucial for intricate designs and tight tolerances.
2. Consistency in Reproduction:
It enables consistent reproduction of patterns across multiple units, making it ideal for mass production with uniform quality.
3. Compatibility with CAD/CAM:
This method works well with CAD/CAM software, enabling designers to easily generate, modify, and transfer designs to machines for production.
4. Versatile Material Application:
You can apply CD pattern processing to a range of materials, including metals, plastics, and silicon wafers, depending on the specific manufacturing requirements.
5. High-Speed Processing:
With the right setup, CD pattern processing can quickly translate digital designs into physical products, boosting efficiency for high-demand production.
6. Enhanced Quality Control:
It allows for real-time quality checks and adjustments, ensuring patterns adhere to strict specifications.
This process is especially useful in applications where precision is key, such as microfabrication, electronics, and specialized prototyping.
High-quality CD pattern processing must have the following ten elements:
1. Advanced Equipment:
Precision tools, such as high-resolution CNC machines, lasers, or lithography systems, are essential for accurately translating digital patterns into physical parts. The equipment must be capable of working with tight tolerances and high-speed processing.
2. Accurate Coordinate Data:
The quality of the coordinate data directly impacts the accuracy of the pattern. The team must define the data clearly, ensuring precise measurements and clear instructions to guide the processing equipment effectively.
3. Robust CAD/CAM Software:
Sophisticated CAD (Computer-Aided Design) and CAM (Computer-Aided Manufacturing) software allow designers to create intricate patterns and simulate the production process, ensuring accuracy before manufacturing begins.
4. Quality Control Systems:
Real-time quality monitoring and inspection systems are crucial. These systems can detect and correct deviations or errors immediately, helping maintain consistent quality across all units.
5. Temperature and Environmental Control:
High-quality CD pattern processing is sensitive to temperature and environmental changes. Proper control helps prevent material deformation, especially in high-precision applications like microfabrication.
6. Skilled Technicians:
Experienced operators or technicians who understand both the equipment and the process are essential. They can make fine adjustments and troubleshoot issues quickly, which is important for maintaining high standards.
7. Calibration and Maintenance:
Regular calibration of equipment ensures that it operates accurately. Routine maintenance also prevents unexpected breakdowns, which can compromise quality and delay production.
8. Material Quality:
Using high-grade materials suited for the intended application ensures that the final product meets durability and performance standards. Low-quality materials may introduce defects or irregularities.
9. Consistent Process Parameters:
You must carefully control and standardize parameters such as speed, feed rate, pressure, and tool settings across runs to produce consistent results.
10. Documented Procedures:
Standardized procedures and best practices guide the entire process, reducing variability and ensuring that every step meets quality requirements.
These elements help maintain the high standards required for applications in industries such as electronics, medical devices, aerospace, and precision manufacturing.
Summarize
CD grain processing is widely used in electronics, medical, aerospace, and other fields for its precision and unique texture, making it a high-end metal surface process.With the help of advanced equipment, precise data, and strict quality control, CD grain processing enhances product texture and market competitiveness. With the increased demand for high-quality products, CD texturing will continue to drive development and innovation in the manufacturing industry.
What is CD Pattern Processing, and how does it work?
CD (Circular Diamond) pattern processing is a precision machining technique that creates intricate, circular, or textured patterns on a material's surface. These patterns enhance aesthetics and functionality, achieved using advanced CNC machining, engraving tools, or diamond cutters.
What materials can be processed with CD pattern technology?
Our CD pattern processing services can be applied to a wide range of materials, including metals (aluminum, stainless steel, brass), plastics, and even some composite materials. Let us know your material, and we’ll confirm compatibility.
What industries benefit from CD pattern processing?
Industries such as consumer electronics, automotive, luxury goods (watches, jewelry), aerospace, medical devices, and premium packaging often use CD patterns to enhance product aesthetics, functionality, and brand value.
What are the benefits of CD pattern processing for my product?
CD patterns add a premium, high-quality appearance, improve grip and usability, and offer wear resistance. They also help products stand out with unique textures or finishes.
Can you customize CD patterns for specific designs?
Yes! We provide fully customizable CD patterns based on your design requirements. Simply provide your design files, specifications, or a concept, and we will tailor the patterns to match your vision.
How long does it take to complete an order?
Lead times depend on the project size, material, and complexity. Typically, small to medium-sized projects are completed within 5–10 business days. For urgent orders, we offer expedited processing options.