Arc spraying is employed in rapid tooling to create durable and wear-resistant molds, dies, and other tooling components quickly and cost-effectively.
Arc spraying can quickly build up coatings, significantly reducing the time needed to produce molds or dies compared to traditional methods; It is often more economical, especially for short-run production or prototyping, as it reduces material waste and machining time; Allows for the creation of complex geometries and fine details that might be difficult or expensive to machine from solid materials.
Other Language: Fr
Wire-arc spraying for rapid tooling presents a transformative approach in manufacturing, combining speed, flexibility, and cost-efficiency. This technique involves spraying molten metal onto a prepared surface to quickly build up durable, wear-resistant coatings, making it particularly advantageous for creating molds, dies, and other tooling components. The ability to rapidly produce and finish tools with complex geometries and tailored material properties significantly reduces lead times and costs associated with traditional machining processes.
Furthermore, wire-arc spraying facilitates the repair and modification of existing tools, extending their service life and optimizing resource utilization. As a result, this method is increasingly becoming a go-to solution in industries requiring swift and reliable tooling solutions, such as injection molding, die casting, and metal stamping.
Arc spraying technology and its application in rapid mold making
1. Principles and characteristics of arc spraying technology
Arc spraying technology is a thermal spraying method. Its principle is to use two mutually insulated metal wires as consumable electrode wires, and use a wire feed roller to continuously and evenly feed them into the two conductive nozzles of the arc spray gun connected to the positive and negative poles of the power supply respectively.
When the two ends of the wires are short-circuited due to feeding, an arc is generated between them, causing the ends of the wires to melt instantly. At the same time, the molten metal is atomized into micro droplets by compressed air flow, which are sprayed onto the surface of the workpiece at a very high speed. After collision, flat deformation occurs, and arc spray coating is formed after stacking [1]. Compared with other thermal spraying methods, arc spraying technology has the following characteristics [2,3]:
① High production efficiency.
The weight of metal sprayed per unit time in arc spraying is proportional to the spraying current. When the spraying current is 300A, 30Kg of zinc wire, 10Kg of aluminum, and 15Kg of stainless steel can be sprayed per hour, which is more than 3 times that of flame wire spraying.
②High coating bonding strength.
Arc spraying particles have large kinetic energy, and can obtain higher bonding strength without increasing the temperature of the workpiece or using expensive substrates. When spraying aluminum bronze, the self-bonding properties of the coating are presented, which further improves the bonding strength. Generally, the bonding strength of arc spraying layers can reach 20MPa, which is 2.5 times that of flame spraying layers.
③High thermal efficiency.
Arc spraying directly converts electrical energy into thermal energy to melt metal, and the thermal energy utilization rate can be as high as 60%~70%, which is the most fully utilized energy among all thermal spraying methods.
④Low production cost, safe operation, and simple maintenance.
2.Application of arc spraying technology in mold manufacturing
The basic principle of arc spraying molding technology is to spray a certain thickness of metal coating on the surface of the prototype, and then separate the coated metal shell from the prototype to obtain a mold cavity that is completely consistent with the shape of the prototype.
After the cavity is backed and reinforced, it can be used for reaction injection molding (RIM), vacuum forming, thermoforming and most polyurethane product molding production processes [4,5]. Because of the high efficiency and economy of arc spraying itself, arc spraying molding technology has low cost and short cycle. Compared with the traditional method of manufacturing plastic molds, arc spraying molding technology has the following advantages:
① The prototype does not need to be conductive, and its surface temperature generally does not exceed 60℃ during spraying, so the material is basically not restricted;
② The obtained mold cavity has a clear contour, unchanged external dimensions, and small thermal stress deformation;
③ High molding efficiency, greatly shortening the molding cycle;
④ The prototype size is not limited, and can be as small as a coin or as large as a vacuum forming mold for manufacturing a car roof;
⑤ Small equipment investment and good economic benefits.
3.Development of arc spraying technology
In the past, arc spraying technology was once neglected due to the rough surface of arc spraying coatings. However, due to the transformation of arc spraying equipment in recent years, especially the great improvement of arc spraying guns by TAFA Company in the United States, high-pressure gas is accelerated through a specially designed nozzle as the supersonic atomizing gas flow for arc spraying, which is used to atomize and accelerate molten metal particles to form a dense arc spraying layer.
This type of spray gun sprays tubular wires containing ceramic powders, which can achieve the performance of plasma coatings[6]. The use of supersonic hot gas flow formed by the combustion of ethanol and air as atomizing gas increases the speed and thermal energy of the molten droplet particles and reduces the oxidation of the metal droplets, thereby improving the quality of arc spraying coatings.
New spraying materials are also constantly emerging, especially the development and application of low shrinkage, high hardness alloy wires and tubular wires. Arc spraying can already obtain smooth, dense, low-porosity high-quality coatings. In addition, it has the advantages of high production efficiency, high coating bonding strength and simple process, so this technology has been rapidly developed and applied.
In China, the research and real application of arc spraying technology began in the early 1980s. Beijing Longyuan Company used AFS-300 equipment to carry out rapid mold making applications such as metal cold spray molds and EDM electrodes, and provided services to enterprises.
Abroad, Francois Peres and Arthur Mofakhami of the Rapid Prototyping Center of the Central University of Paris, France, have experimented with arc spraying technology for injection mold manufacturing and conducted in-depth research on the arc spraying molding process [7]. The Technical University of Denmark tried to use the spraying method to manufacture EDM electrodes and found that the produced electrodes had a very high loss rate during the processing and could not be used in actual EDM [8].
Research on arc spraying molding technology
1.Arc spraying molding process based on rapid prototyping
Combining the high efficiency and economy of arc spraying with the rapid and intuitive characteristics of rapid prototyping can realize the rapid and economical manufacturing of injection molds. Arc spraying molding generally includes the following process flow: prototype design – prototype manufacturing – spraying – backing reinforcement – demolding – finishing – assembly – trial mold.
For FDM and LOM rapid prototyping, optimization in terms of material properties, control accuracy and process parameters can produce prototypes with high precision and low roughness[9]; because the material is generally ABS plastic or paper, after spraying, chemical dissolution can be used to release the mold to avoid damage to the spray layer.
Therefore, for arc spraying molding of FDM and LOM rapid prototyping, the key lies in the manufacture of the metal shell, which depends on the selection of spray wire and the optimization of spray process parameters[10].
2.Determination of the spray wire material for arc spraying mold
(1) Main process parameters of arc spraying and their influence on coating performance
The coating performance of arc spraying usually includes coating microstructure, bonding strength, porosity, corrosion resistance, etc. Different spray wire materials have different coating performances. The same material can also obtain different coating performances by using different spray parameters.
① Working voltage
Spraying the same material at different working voltages will produce coatings with different performances. If the working voltage is too low, part of the spray wire material cannot be completely melted and directly flies to the workpiece surface, which will cause irregular coarse particles in the coating.
If the working voltage is too low, the arc cannot be started. If the working voltage is too high, the burning loss of carbon and alloy elements will be aggravated, the oxide content will increase, and the coating surface will become rough. Usually, in order to reduce the burning loss of carbon and alloy elements, a lower working voltage is used as much as possible while ensuring normal spraying [1].
② Spraying current
As the spraying current increases, the coating hardness increases. This is because as the current increases, the oxide content in the coating increases significantly. Although the carbon and alloying elements in the alloy are burned off, the rapid increase in the oxide content plays a more important role, resulting in increased hardness.
Spraying production efficiency is almost proportional to the spraying current, because the spraying current is directly dependent on the wire feeding speed. In addition, the spraying current has a certain influence on the surface morphology and bonding strength of the coating, but the influence is relatively small [1].
③ Compressed air
When arc spraying is performed with unpurified compressed air, the oil and water in the compressed air not only take away a large amount of heat energy, but also increase the oxidation opportunity of the sprayed particles, polluting the surface of the workpiece to be sprayed and the coating itself.
Therefore, the oxide content of the obtained coating increases significantly. In humid weather, untreated compressed air makes spraying impossible. Therefore, the compressed air must be purified. The air pressure also affects the coating performance.
When the air pressure is too low, the particle flight speed is low and the particle stays in the air for a long time, resulting in coarse and loose coating particles and increased oxide content. As the air pressure increases, the atomization effect improves and the coating becomes dense and smooth[5].
④ Spraying distance
The spraying distance has a significant impact on both the metal deposition rate and the coating hardness. As the spraying distance increases, the metal deposition rate decreases. This is because some of the sprayed particles disperse and fly out, while some of the sprayed particles cannot adhere to the substrate due to the decrease in temperature and kinetic energy.
The increase in the spraying distance has three effects on the coating hardness: the temperature of the sprayed particles decreases, the flight speed decreases, resulting in a decrease in the density of the coating; the sprayed particles fly longer in the air, increasing the burnout of carbon and alloy elements; and the oxide content in the coating increases.
The first two factors lead to a decrease in the coating hardness. Although the increase in the oxide content can increase the coating hardness, its effect on the coating hardness is far less than the first two factors. Therefore, the coating hardness decreases with the increase in the spraying distance, and the coating density also decreases.
If the spraying distance is too short, the arc will directly heat the workpiece and the coating, and the compressed air will recoil to form a plain flow area, affecting the atomization effect and coating quality, and bringing difficulties to the operation[5].
⑤ Pretreatment
Like other thermal spraying methods, the quality of substrate surface pretreatment directly affects the bonding strength of the coating. The better the roughening effect, the larger the bonding area between the coating and the substrate, and the higher the bonding strength.
Taking into account the influence of the above factors on coating quality and production efficiency, the D-AS1620 arc sprayer of Beijing Jiangyuan Company was used to spray Zn, Cu, Al and other metal wires. The test results show that arc spraying of Zn, Cu, Al and other metal wires using the process parameters shown in Table 4-1 can obtain coatings with better performance and higher spraying efficiency.
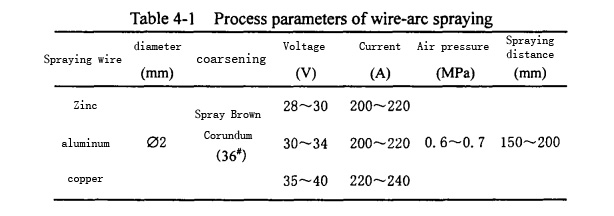
(2) Experimental study on the performance of arc spraying mold coating
① Experimental method and purpose
Using common wire materials such as Zn, Al, and Cu as arc spray materials, spraying mold testing was carried out on the surface of ABS plastic rapid prototypes. To ensure good bonding between the coating and the prototype, the prototype surface was sandblasted with brown corundum (36#) before spraying. When spraying Zn, Al, and Cu coatings, two identical metal wires were fed into the two conductive nozzles of the spray gun, while when spraying Zn-A1 pseudo-alloy coatings, one Zn wire and one Al wire were fed into the two conductive nozzles respectively.
The arc spraying process parameters selected for the test are shown in Table 4-2. After spraying, the strength and hardness of different coatings were tested, and their spraying process performance was observed and compared. Finally, a relatively good coating was selected as the material for arc spraying mold.
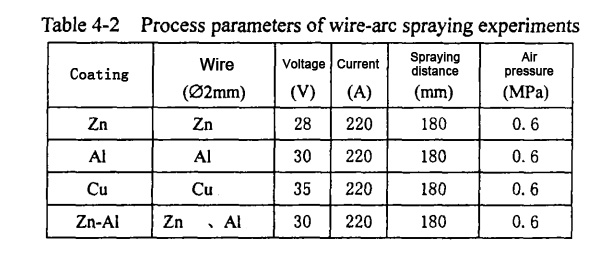
② Experimental results and analysis
A. Coating stress analysis
The key to arc spraying mold making is to form a metal shell with high replication accuracy, certain strength and hardness on the surface of the model. During the spraying process, the metal shell cannot be separated from the model too early, and the shell and the model cannot be greatly deformed, otherwise the metal shell cannot reflect the true shape of the model and the mold will lose accuracy. If the shear stress between the metal coating and the model surface exceeds the shear strength between the interfaces, the metal shell will separate from the model.
The factors that affect the shear stress between the metal shell and the model mainly include the mechanical properties and thermophysical properties of the metal shell material itself, the temperature of the model surface during spraying, and the difference in thermal expansion coefficient between the metal coating and the model material[10]. According to materials science knowledge[11~13], the relevant material parameters of Zn, A1, Cu wire and ABS plastic are shown in Table 4-3.
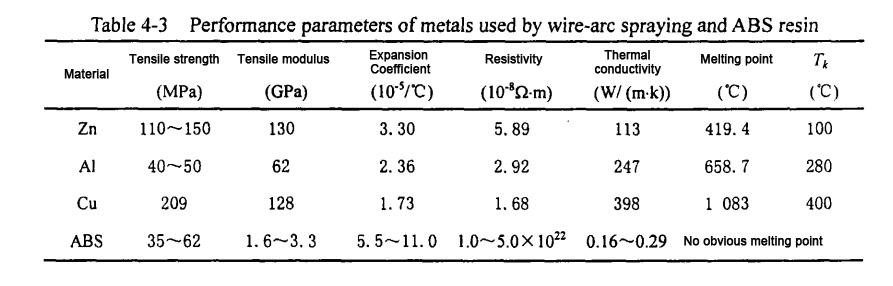
In the early stage of spraying, the molten metal droplets are sprayed at high speed by compressed air onto the model surface with a lower temperature, flattened by impact to form a coating, and rapidly solidified and cooled at a cooling rate of 105℃/s~106℃/s[10]. During the solidification and cooling process, the cooling shrinkage of the metal coating is fixed by the model surface, and thus it is subjected to a large tensile stress.
As the temperature decreases, the deformation of the metal coating changes from mainly plastic deformation to mainly elastic deformation, and the residual stress of the coating is mainly caused by elastic deformation. The elastic-plastic transition temperature range is represented by Tk[14]. At this time, the shrinkage strain and stress of the metal coating are:

Where: ΔT – temperature difference from melting point to room temperature of metal
Α – expansion coefficient of metal coating;
E – elastic modulus;
T0 – model surface temperature.
The model surface temperature increases as the spraying progresses. Assuming that the temperature of the model surface is maintained at 60℃ during the subsequent spraying process, the calculation results of strain and stress of different metal coatings are shown in Table 4-4.
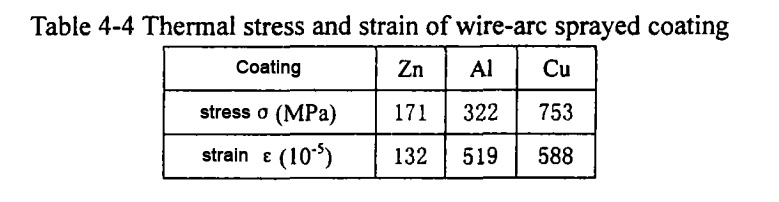
From the table above, it can be seen that as the melting point of the material increases, the thermal stress and thermal strain generated by the metal coating during the deposition process increase. In general, the elastic modulus of the metal decreases as the temperature increases[15], and the actual internal stress of the metal coating is less than the calculated value. At high temperatures, the creep of the metal offsets part of the elastic deformation.
At the same time, the calculated thermal stress results of materials such as n, Al, Cu (especially Al and Cu) are greater than the tensile strength of the material, which will cause a large number of microcracks in the coating[16] to release most of the internal stress.
After stopping spraying, during the process of the metal coating and the model naturally cooling to room temperature (20°C), since the thermal expansion coefficient of the metal coating is smaller than the thermal expansion coefficient of the ABS plastic model, the internal stress of the metal coating will be partially offset by the shrinkage of the model. The internal stress of the coating when cooled to room temperature can be calculated using the following formula:

Where: ER- elastic modulus of ABS plastic:
αR- thermal expansion coefficient of ABS plastic:
K- stress release coefficient.
Then the residual strain of the coating is:
ε= σ/E (4-4)
Assuming that 90% of the internal stress of the metal spray coating is released at 60°C, the average value of the thermal expansion coefficient and elastic modulus of ABS plastic is taken for calculation. The residual internal stress and strain calculation results of each metal spray coating at room temperature are shown in Table 4-5.
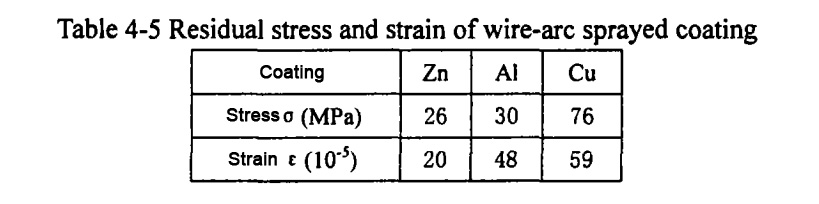
From the results in Table 4-5, it can be seen that when cooled to room temperature, even if 90% of the internal stress of the metal coating is released through creep and microcracks, and partially offset by the shrinkage of the model, the high melting point metal coating still has a large residual internal stress.
With the continuous deposition of metal, the coatings deposited successively constrain each other, making it more difficult for the coating to release internal stress by generating microcracks, and the residual internal stress is greater at this time. The residual internal stress acts between the metal coating and the model to form shear stress. If this shear stress exceeds the shear strength between the interfaces, the coating will peel and warp.
In summary, during the spraying process, due to the effect of thermal shrinkage, there is a large shear stress between the metal coating and the model interface, which causes plastic deformation of the model and the metal coating on the one hand, and separation of the metal coating and the model due to elastic deformation on the other hand, affecting the accuracy of the arc spraying mold.
Moreover, the higher the melting point of the spraying material, the greater the shear stress, and the greater the impact on the accuracy of the mold. The use of high melting point materials is also easy to burn the surface of the model, affecting the surface finish of the mold.
Therefore, from the perspective of stress, the material of the arc spraying mold should be selected from low melting point metals such as Zn and A1, so that a coating with lower internal stress can be obtained. However, because the mechanical properties of low melting point metals are generally not high, arc spraying molds are mainly used in product trial production.
B. Experimental analysis of mechanical properties of coatings.
It is difficult to achieve excellent mechanical properties and internal stress of the obtained coating by arc spraying molds with Zn, A1, Cu and other metal materials alone. In order to improve the mechanical properties of the mold, if Zn and AI wires are considered to be fed simultaneously for arc spraying, the obtained coating must be different from the pure Zn or AI coating.
Therefore, Zn, A1, Cu and Zn-AI wires were arc sprayed with the process parameters shown in Table 4-2, and their tensile strength, hardness, density and spraying processability were investigated and compared. The experimental results are shown in Table 4-6.
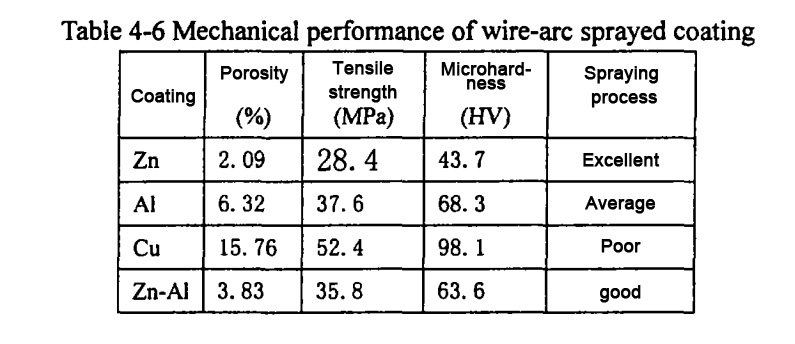
From the above table, we can see that the Zn coating has the densest structure and the best spraying processability, but the lowest strength and hardness; the Cu coating has the highest strength and hardness, but the loosest structure and the worst spraying processability; in comparison, the density of the Zn-A1 pseudo-alloy coating is significantly higher than that of the A1 coating, its hardness is higher than that of the n coating and close to that of the A1 coating, and its spraying processability is good.
Since no new phase appears after arc spraying, the strength and hardness of the metal spray coating depend on the mechanical properties of the metal material itself and the organizational structure of the coating. Zn has a low melting point.
During the spraying process, the metallization effect is good, and the metal droplets are evenly and finely deposited on the model surface, so the resulting coating has a high density. A1 has a high melting point. During spraying, the larger droplets are not easy to flatten when deposited on the model surface, and it is easy to form splashes.
The bonding between the coatings is not tight, and the coating is relatively loose. The Zn-AI pseudo-alloy coating is a mechanical mixture of Zn and A1 phases. Since the wires are fed simultaneously and the wire diameters are the same, the volume ratio of Zn and A1 in the coating is 1:1, and the weight ratio is close to 3:1. The fine Zn droplets with a high degree of atomization can fill the larger gaps formed by AI splashes. Therefore, the organization of the Zn-A1 pseudo-alloy coating is dense, close to that of the Zn coating.
It was also found during the spraying process that if the process operation is not proper, the A1 coating, especially the Cu coating, is prone to warping and cracking, as well as separation from the model. If copper is arc sprayed on the LOM paper rapid prototype, the coating cannot be deposited at all, and the prototype surface will be burned or even scrapped due to heat debonding.
The spraying process of Zn and Zn-A1 pseudo alloy is very good. The Zn-A1 pseudo alloy coating has a dense structure, and its strength and hardness are close to those of the A1 coating. It is an arc spraying molding material with good comprehensive mechanical properties.
4. Example of arc spraying mold preparation
After the material of the arc spraying mold is determined, Zn-AI pseudo alloy is arc sprayed on the FDM and LOM prototypes respectively. After the metal shell is deposited to a certain thickness, it is reinforced with a ring resin backing on the back, and then the prototype is removed by dissolving.
The mold obtained is shown in Figure 4-1. It can be seen that the obtained Zn-A1 pseudo alloy coating is dense, has high replication accuracy, has certain strength and hardness, and the entire molding process is fast and low-cost, which is suitable for the development and trial production of new products.
Summary of this chapter
By analyzing the influence of the main process parameters of arc spraying on the coating performance, combined with experiments, the optimized process parameters suitable for Zn, A1,
Cu wire spraying are found.
The Zn, Al, Cu single metal and Zn-Al pseudo alloy spraying tests were carried out with optimized process parameters, and the mechanical properties of each coating were tested and compared: the internal stress of the coating caused by the thermal shrinkage of the metal coating during arc spraying was analyzed, the internal stress of different coatings was calculated and compared, and combined with the mechanical properties of each coating, it was concluded that the Zn-A1 pseudo alloy coating is suitable for arc spraying molding.
Zn-Al pseudo alloy arc spraying was carried out on FDM and LOM rapid prototypes, and molds with dense coatings, high replication accuracy, certain strength and hardness were obtained, but still could not meet the requirements of mass production, proving that arc spraying molding is an efficient and low-cost rapid molding method suitable for new product development and trial production.
Reference
- [1] Zeng Guiyu, Yan Shuqun. Research on arc wire spraying technology. Hunan Metallurgy, 2000, (1): 3~8(43)
- [2] Du Xiaohong. Development and application of arc spraying technology in China. Surface Technology, 2000, 29(5): 21~24
- [3] Wang Hangong. Supersonic arc spraying technology. Beijing: National Defense Industry Press, 1999. 4~5
- [4] Liu Xianjun, Xu Binshi, Ma Shining, etc., Application of arc spraying technology to manufacture plastic molds. Mold Technology,1996,(6):25~30
- [5] Song Baotong, Yu Linqi, Wei Shuling, Research and application of arc spraying mold making technology, Electrical machining and mold,2000,(1):39~41
- [6] Wen J.Supersonic arc spraying process.Proc.of the ITSc(J).Kobe, 1995.317~320
- [7] Francois Peres,Arthur Mofakhami.Rapid Tooling from Prototypes:the Cool Spray Moldmaking Method,SPIE,1998,Vo13517:79~90
- [8] Qian Bibo, Pan Xiaohong, Cheng Yaodong, etc., Rapid prototyping technology and its application in mold manufacturing. Mechanical Research and Application,1998,11
- [9] Zou Guolin, Research on fused deposition modeling precision and rapid mold manufacturing technology (doctoral dissertation). Dalian: Dalian University of Technology, 2002
- [10] Wang Yiqing, Zhao Wenzhen, et al. Research on the performance of arc spraying mold materials, Mechanical Engineering of China,2000,11(10):1112~1115
- [11] Zeng Zhengming. Practical Engineering Materials Technology Handbook, Beijing: Machinery Industry Press,2001.3
- [12] Dong Junguo. Practical Materials Handbook. Beijing: Metallurgical Industry Press, 2000
- [13] An Jiru, Handbook of Common Metal Materials in China and Abroad. Xi’an: Xi’an Jiaotong University Press, 1990.7
- [14] Chen Guozhen, Xiao Keze, Jiang Buju. Handbook of Casting Defects and Countermeasures. Beijing: Machinery Industry Press, 1996.177
- [15] Chinese Society for Metals, Chinese Society for Nonferrous Metals, Handbook of Physical Properties of Metal Materials. Beijing: Metallurgical Industry Press, 1987.58
- [16] Tobe S. Macro- and micro- stress in plasma a spray coating and its stress versus strainbehavior.Proceeding of the 7th National Thermal Spray Conference, 1994, BostonMassachusetts:693~697