Table of Contents
As a critical technology in the modern manufacturing industry, High-Speed Machining (HSM) or High-Speed Cutting (HSC) has achieved remarkable results in many industries.
High-speed cutting technology has evolved through extensive research and development to widespread industrial use.
HSM technology, driven by advances in materials, computers, tooling, and machines, boosts efficiency and quality.
This article covers the concept, advantages, challenges, applications, bottlenecks, and future trends of high-speed machining.
High-speed cutting drives productivity in precision industries like aerospace, automotive, and medical.
This article aims to help readers understand high-speed cutting technology, its applications, and industrial impact.
Overview of high-speed cutting machining
High-speed cutting processing, since the 1930s, experienced more than half a century of theoretical research and practical exploration.
Recent advancements in material science, computer technology, and machining have made high-speed cutting essential in advanced manufacturing, particularly in developed countries like Germany, the U.S., and Japan.
High-speed cutting offers high productivity, accuracy, surface quality, and cost savings, benefiting aviation, automotive, and mold industries.
Its core technologies include high-speed soft, hard, dry, and high-feed rate cutting, revolutionizing manufacturing.
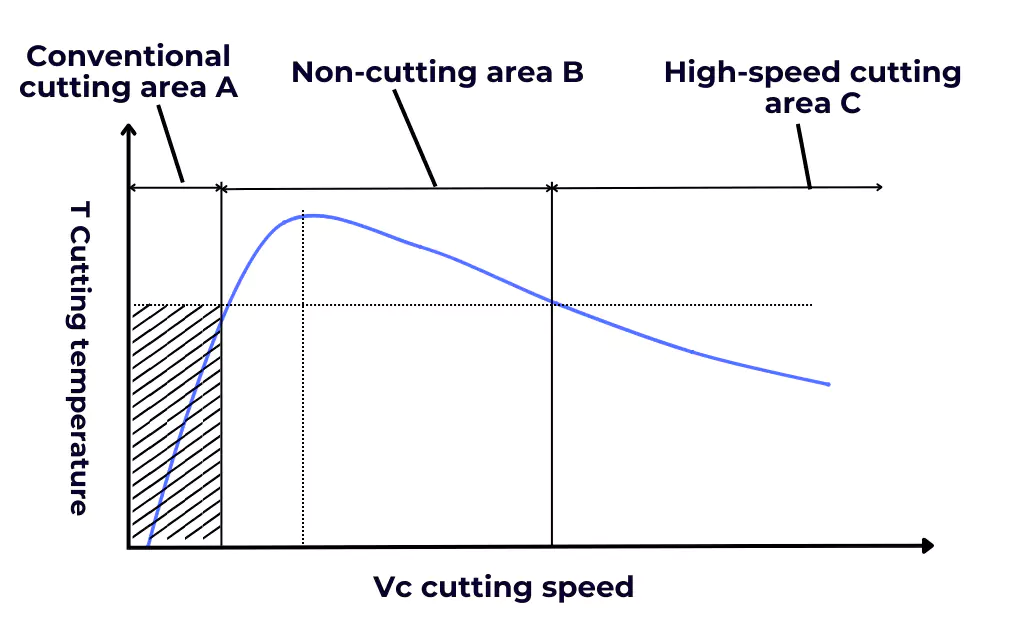
Figure 1 shows the emergence of the concept of high-speed cutting
High-speed cutting machining superiority
Due to its unique advantages, high-speed cutting (HSC) is rapidly becoming a key technology for improving productivity and part quality in modern manufacturing.
It not only significantly increases machining speed but also optimizes tool use and reduces production costs.
With precision machining capabilities and lower energy consumption, high-speed cutting has become the ideal choice for meeting high precision and quality requirements.
The following are the main advantages of high-speed cutting machining:
1. Improve machining efficiency and reduce costs
With the increased cutting speed, the material removal efficiency per unit time is dramatically increased, and the machining time is drastically reduced.
This not only significantly improves productivity but also effectively reduces processing costs.
2. Reduce cutting force, adapt to complex parts processing
Under high-speed cutting conditions, the cutting force can be reduced by more than 30% on average.
This feature reduces the high-speed spindle’s power consumption, making it especially suitable for processing low-rigidity and thin-walled parts and improving the stability of machining.
3. Reduced heat transfer and improved machining accuracy
In high-speed cutting, chips are discharged at a very high speed and remove most of the cutting heat (up to 90% or more), so the heat transferred to the workpiece is greatly reduced.
Workpiece heating is reduced, reducing thermal deformation and processing residual stress, thus significantly improving machining accuracy.
4. Improve surface quality and reduce vibration
From a kinetic point of view, high-speed cutting can effectively reduce the cutting force, thereby reducing vibration.
At the same time, high speed moves the cutting system’s operating frequency away from the machine’s low-order intrinsic frequency, which significantly reduces the roughness of the workpiece’s surface, improving the surface quality.
5. Alternative to grinding for hardened materials
High-speed cutting can significantly increase the efficiency of grinding for roughing and semi-finishing of hardened materials.
Since cutting fluid is not needed, the method is more environmentally friendly, which is important for environmental protection.
Disadvantages of High-Speed Machining
Despite its advantages, high-speed cutting (HSC) faces challenges and limitations in practical use.
The following are the main drawbacks of high-speed cutting machining technology in practical application:
1. High tool cost
High-speed cutting requires very high performance of tool materials, such as heat resistance, wear resistance, and strength, which significantly increases their cost.
2. High requirements for machine tools and CNC systems
High-speed cutting requires special high-speed machine tools and high-performance CNC systems. The purchase and maintenance costs of this equipment are high, increasing the initial investment costs.
3. Stringent requirements for tool balance performance
High-speed operation and tool balance are critical to the quality of processing and equipment stability.
If tool balance performance is slightly inadequate, it may lead to machining errors or even equipment damage.
4. Short spindle life
In high-speed cutting conditions, the machine tool spindle’s high-frequency operation leads to increased wear and tear, and its service life is usually shorter than that of the spindle under traditional machining conditions.
High-speed cutting mechanism
High-speed cutting mechanism research helps understand chip formation, cutting force, heat, tool wear, and surface quality.
These studies promote the development of high-speed machine and cutting tools and provide theoretical guidance for production.
The following are several significant aspects of high-speed cutting mechanism research:
1. Chip formation mechanism and cutting process
The chip formation process in high-speed cutting is the core of understanding the cutting principle. In high-speed cutting, chips experience complex deformation under the action of cutting force.
By studying the chip formation mechanism, cutting force, and dynamic modeling, we can better predict the changes in the cutting process.
2. Basic laws in high-speed cutting
During high-speed cutting, cutting force, cutting temperature, tool wear, and other factors affect machining quality.
The study of these phenomena and their relationship with machining parameters helps propose mathematical models and optimize cutting parameters.
Through experimental design and data processing methods, multi-objective optimization can be achieved to improve productivity and machining quality.
3. High-speed cutting mechanism of various materials
The behavior of different materials in high-speed cutting varies greatly, so it is crucial to study their high-speed cutting mechanism.
The relevant high-speed cutting database can be established through experiments and data analysis to provide theoretical support for processing different materials.
4. High-speed cutting virtual technology
In the cutting process, three deformation zones are formed between the tool and the workpiece: the primary deformation zone, the second deformation zone, and the friction zone, as shown in Fig. 2.
Chips first shear in the primary deformation zone, then deform in the second zone, and finally experience friction with the tool’s rear surface.
The interaction of these deformation zones determines the efficiency of the cutting process and tool life.
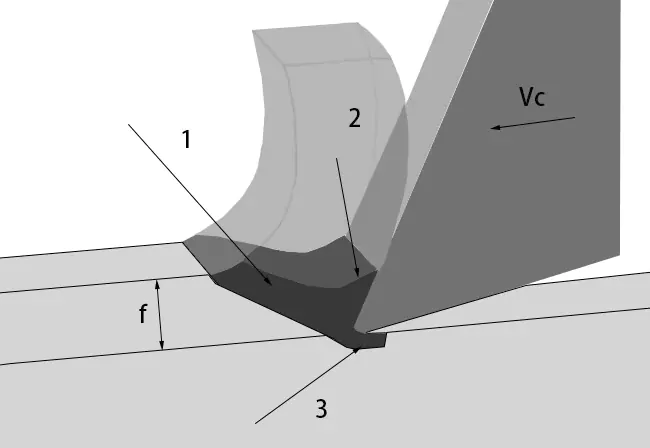
Fig. 2 Definition of shear region
5. Robetl.King’s high-speed cutting mechanism theory
In the 1970s, Robetl.King and McDonald proposed a more complete high-speed cutting mechanism model.
Their research found that thermal softening and strain hardening in high-speed cutting alter cutting force.
In conventional cutting, the deformation process is relatively smooth, and the cutting force increases with the accumulation of deformation.
High-speed cutting causes rapid deformation, preventing material hardening and reducing cutting force.
High-speed cutting increases local temperature, causing material slip and reducing cutting force.
Mutational slip and adiabatic shear explain the reduced cutting force at high speeds.
Conventional Milling and High-Speed Machining
There are significant differences between conventional milling and high-speed machining (HSM) in several aspects, mainly in machining efficiency, workpiece quality, tool life, machining accuracy, machining cost, and process flexibility.
As manufacturing technology evolves, high-speed machining is becoming the preferred choice for many high-precision, high-efficiency production tasks, while conventional milling still has advantages in specific areas.
The following is a detailed comparison and analysis of the two:
1. Tool-workpiece contact time
Conventional milling: In traditional machining, the contact time between the tool and the workpiece is long, and the cutting process is slow. Longer contact time means more friction between the tool and the workpiece, generating more heat.
High-speed machining (HSM): High-speed machining reduces tool-workpiece contact, friction, and heat, improving efficiency and surface quality.
2. Cutting force and cutting parameters
Conventional milling: In conventional machining, the tool faces large cutting forces and stresses at the contact point.
As a result, the tool burden needs to be reduced by decreasing the depth of cut, rotational speed, and feed rate, which usually affects the machining efficiency.
High-speed machining (HSM): High-speed machining utilizes high cutting speeds and feed rates to remove more material while reducing tool burden quickly.
The cutting forces during high-speed cutting are relatively low, resulting in less stress and strain on the tool.
3. Machining accuracy and surface quality
Conventional milling: Conventional machining often causes poor surface quality, thermal deformation, and accuracy issues.
In addition, due to the slower machining process, accuracy control is more difficult, especially in more complex shapes and details.
High-speed machining (HSM): High-speed machining improves the surface finish and machining accuracy of the workpiece through higher feed rates and precise control.
Higher material removal rates also reduce heat buildup and distortion, ensuring higher dimensional stability.
4. Material removal rate
Conventional Milling: Conventional milling has a lower material removal rate, especially if deep cutting is required. The cutting process is slower and less efficient.
High-Speed Machining (HSM): HSM has a higher material removal rate. High cutting speed and feed rate enable rapid material removal, enhancing productivity for complex parts.
5. Tool life and wear
Conventional milling: During conventional milling, due to the larger cutting force and friction, tool wear is faster, and tool life is shorter.
The tool is subject to severe wear and damage due to frequent cutting contact and heat accumulation.
High-speed machining (HSM): Technology can significantly extend tool life. Although the feed rate of high-speed cutting is higher, the tool is subjected to less stress and less wear due to shorter contact time and lower cutting forces.
6. Cooling and Lubrication Requirements
Conventional Milling: Conventional milling usually requires a large amount of coolant to reduce the cutting temperature due to high friction, tool wear, and workpiece deformation caused by friction.
High-speed machining (HSM): Due to the fast cutting speed and short contact time, the demand for coolant during high-speed machining is relatively small.
However, in certain high-temperature materials machining, coolant is still needed to help with temperature control.
Applications of High-Speed Machining
High-speed machining (HSM) is used in a wide range of industries, especially in production environments where high accuracy and efficiency are required.
HSM technology significantly increases productivity and reduces production costs by increasing cutting speeds and feed rates while shortening lead times, thus enhancing overall competitiveness.
Below are a few of the major industries in which high-speed machining is used:
1. Aerospace industry
The aerospace industry has extremely demanding material requirements, especially in manufacturing aircraft components requiring extreme durability and reliability.
Adopting HSM technology in the aerospace industry can significantly increase production efficiency while ensuring quality.
Major applications include machining complex materials such as high-strength aluminum and titanium alloys. The main reasons for choosing HSM technology include
Deep Cutting Levels: The ability to perform deep cutting improves machining efficiency.
High-speed cutting: High-speed machining can greatly reduce machining time.
High precision: HSM technology can achieve very high machining precision, meeting the aerospace industry’s strict requirements on part size and surface quality.
Optimized Cutting Parameters: By choosing cutting speeds and feed rates appropriately, productivity can be maximized while maintaining tool life.
These advantages make high-speed machining an integral part of the aerospace industry, especially in manufacturing high-precision components.
2. Medical Industry
The medical industry has exceptionally high requirements for precision and reliability, especially in manufacturing medical devices, orthopedic implants, joint implants, surgical instruments, and other critical components.
High-speed CNC machining can provide high-precision and high-quality machining results to meet the high standards of the medical industry. HSM applications in the medical sector include:
Precision parts machining: These include orthopedic implants, dental tools, and other items that require smooth surfaces and precise dimensions.
Customized production: Flexible response to small batch production and customized requirements.
High material adaptability: It can process a variety of high-strength materials, such as titanium alloy and stainless steel, to meet the material requirements of different medical devices.
As medical device manufacturers demand higher quality while improving production efficiency, HSM technology undoubtedly supports the medical industry.
3. Automotive industry
High-speed machining in automotive reduces part weight, improves efficiency, and cuts costs.
High-speed machining of aluminum alloy and other lightweight materials has grown due to rising demand.
HSM applications in the automotive industry include:
Small-lot production and complex parts processing: High-speed machining can quickly produce complex shapes of parts, such as engine parts and body parts.
Mold Manufacturing: High-speed machining technology in mold manufacturing applications can improve the accuracy of the mold, increase production efficiency, and shorten the delivery cycle.
Mass production: For mass production of parts, high-speed machining can improve efficiency and reduce costs, meeting the automotive industry’s rapid production and production costs.
The automotive industry increasingly relies on high-speed machining technology to increase productivity and reduce production costs while maintaining high-quality standards.
Many CNC service companies offer reliable high-speed machining solutions for automotive components.
High-speed machining key technologies and development trends
High-speed cutting technology, especially ultra-high-speed, has become a core technology in modern manufacturing.
It relies on high-precision machine tools and advanced tool materials and supports advanced machining processes, measurement technology, and cutting mechanisms.
The following are the critical technologies of high-speed cutting machining and its development trend:
1. Key technology components
High-speed cutting machining is a highly integrated system engineering, covering several key technical elements, including:
Machine structure and materials: High-speed cutting demands high rigidity, stability, and thermal control, requiring advanced materials and design.
High-speed spindle system: Spindle speed and accuracy directly affect cutting performance; therefore, the development of a high-speed, high-stability spindle system is critical.
Rapid feed system: Increase feed speed and accuracy to improve machining efficiency and reduce machining time.
High-performance CNC control system: Precision control systems can ensure accurate positioning and stable machining under high cutting speed.
High-performance tool clamping system: To ensure tool stability, the tool clamping system should be able to adapt to the high load and high-frequency operation of high-speed cutting.
Tool materials and design: High-speed cutting requires tools with high wear resistance, high thermal stability, and sufficient strength. Therefore, new high-performance tool materials and optimized design are needed.
High-efficiency and high-precision measurement technology: Accurate measurement and inspection ensure real-time feedback and precision control.
High-speed cutting mechanism and process: Study of cutting process mechanics, thermal behavior, and parameter optimization to improve efficiency and quality.
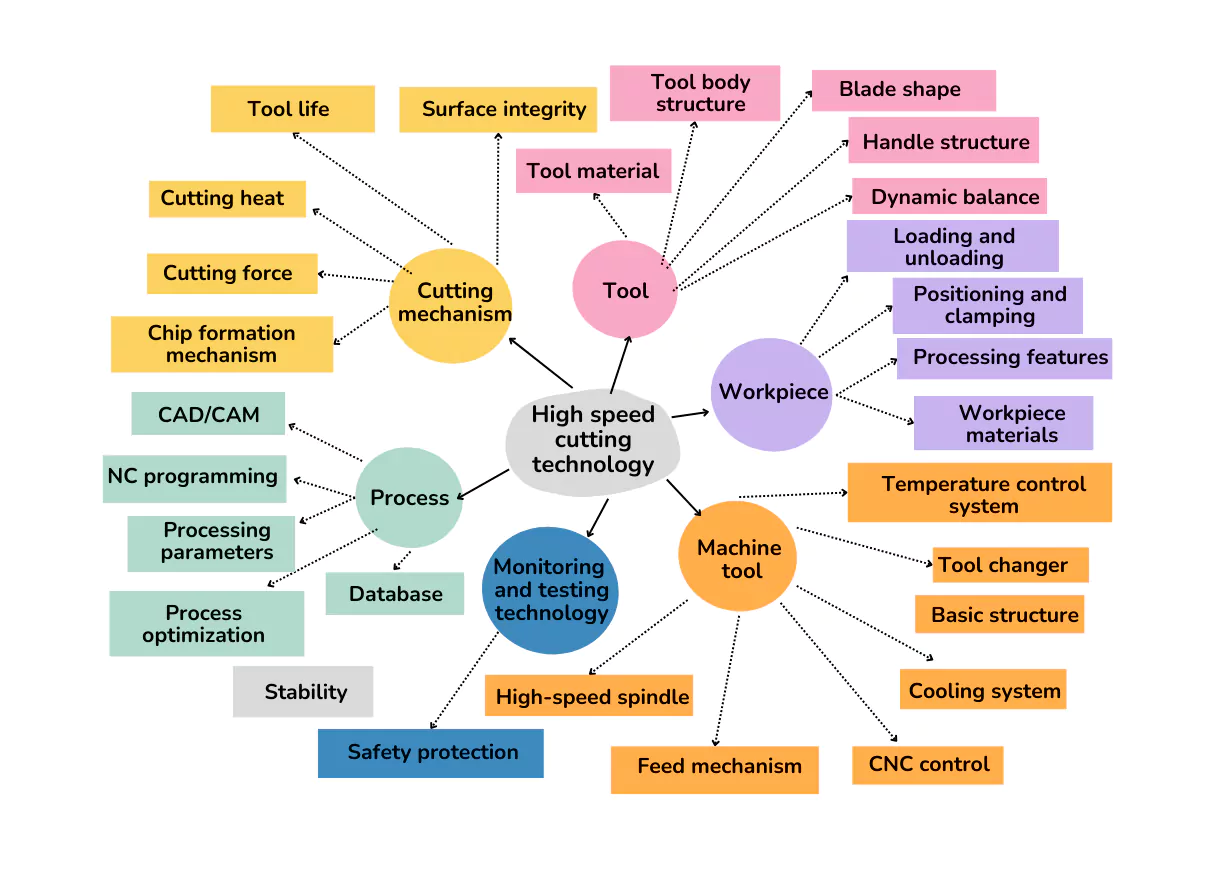
Figure 3 High-speed cutting machining research system
2. Development trend
With the continuous progress of manufacturing technology and processes, ultra-high-speed cutting will usher in new developments in the following aspects:
(1) Green ultra-high-speed cutting
In the future, high-speed cutting technology will pay more attention to environmental protection and energy saving.
Realizing a dry cutting or quasi-dry cutting state to avoid the use of large amounts of cutting fluid not only reduces environmental pollution but also reduces production costs.
Optimizing the tool material and cutting process can still maintain a good cutting effect and stability under the condition that there is no coolant.
(2) heavy cutting process in the ultra-high speed cutting
The application of high-speed cutting technology will no longer be limited to light cutting and finishing and will be gradually promoted to the heavy cutting process in the future.
By increasing the cutting force and cutting speed, the processing efficiency will be improved, and the processing time and cost will be effectively reduced.
(3) The development and improvement of ultra-high-speed cutting process methods
As technology advances, new ultra-high-speed cutting methods like multi-axis linkage and ultra-precision cutting will drive improvements in precision, efficiency, and applications.
(4) ultra-high-speed cutting of difficult-to-machine materials
(5) Machining status monitoring system based on new detection technology
As intelligent manufacturing advances, sensor-based monitoring and big data analysis will become core technologies for future high-speed cutting.
Conclusion
High-speed cutting technology is revolutionary in modern manufacturing. It boosts production efficiency and reduces processing costs.
It also advances precision machining, significantly expanding manufacturing applications.
From aerospace to medical, automotive, and other industries, high-speed cutting has become an indispensable part of the production process in many fields.
High-speed cutting technology has achieved impressive results. However, equipment and tool materials can be further optimized.
Additionally, improvements in machining processes and other areas are possible.
Continuous theoretical research and practical exploration drive high-speed cutting technology forward.
This approach fosters manufacturing upgrades and industry progress.