Table of Contents
With the rapid advancement of technology, the mechanical mold manufacturing industry faces both new challenges and opportunities. Traditional methods struggle to meet high-precision demands. CNC machining technology, however, uses computer-controlled equipment to convert design data into machine instructions, improving precision, quality, and speed in mold production.
The widespread use of CNC technology has driven the rapid growth of the mold manufacturing industry. It has created more business opportunities and profits for companies, injecting new vitality into the entire sector. This technology has enabled the industry to better meet market demands and fueled its overall prosperity.
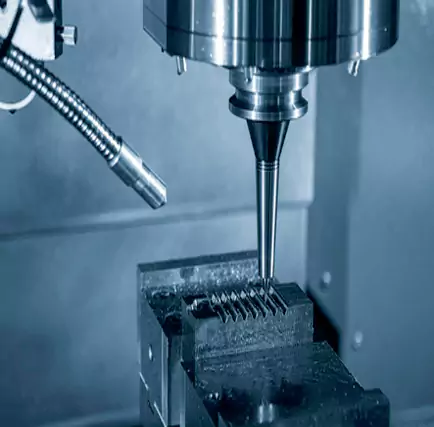
Basic concepts
CNC machining technology uses CNC machine tools to control the machining process through digital information. Compared to traditional machine tools, CNC machines offer higher precision and complexity.
For example, CNC machining is used to manufacture fine gears in watches. These gears have complex shapes and require high precision. Traditional machines cannot meet these demands, but CNC machines can process them accurately according to design specifications.
CNC machining is also widely used in the automotive industry. It enables efficient processing of complex parts, improving production efficiency. A mechanical mold is a tool used to shape objects.
It consists of various parts, and each mold has a unique design and structure. For example, car engines are made using mechanical molds.
Parts like crankshafts and pistons are processed through molds to achieve precise shapes and dimensions.
Similarly, mobile phone shells, buttons, and other components are also made using mechanical molds. Even in the military industry, complex weapons and equipment rely on mechanical molds.
Modern life depends heavily on mechanical mold manufacturing and CNC machining technology. They not only produce a wide variety of products but also drive the growth of the manufacturing industry.
A renowned scientist once said, “Mechanical mold manufacturing and CNC machining are the backbone of modern industry, creating countless miracles for mankind.”
Application value
When a mold processing company receives an order, production often starts quickly. The process involves many steps that must be done within a specific time frame. Delays could affect delivery times.
For example, a car manufacturer may need precision car part molds. The mold company must meet a strict deadline to keep the car production on track. Each step must be precise.
Any errors can ruin the mold or make it substandard, causing significant losses and delays.
1. Efficiency Gains with CNC Technology
(1) Automation Streamlines Production
CNC (Computer Numerical Control) technology has greatly improved efficiency. Operators can input programming instructions, and CNC machines will automatically process materials.
This automation saves human resources and reduces errors from human factors.
(2) Reducing Human Error
In the past, workers had to measure and cut materials by hand. This often led to errors. CNC machines, however, follow preset programs to cut and engrave with precision.
This ensures mold accuracy and quality. Production efficiency increases, costs decrease, and mold output becomes more consistent.
2. Enhanced Mold Performance through CNC Machining
(1) Improved Quality Control
CNC technology improves mold performance. Digital processing allows molds to be cut precisely, avoiding human error.
Manual operations often caused deviations in tool movement, leading to rough surfaces and inaccurate mold dimensions.
CNC machines ensure tool movement is precise, maintaining accuracy and quality.
(2) Increased Mold Longevity and Competitiveness
Precise mold processing extends its lifespan and improves stability. This helps companies maintain high standards, giving them a competitive advantage.
3. Enhancing Efficiency and Quality
In conclusion, CNC machining has transformed the mold manufacturing process. It boosts efficiency and enhances mold performance and quality.
Automated processing minimizes human interference, ensuring consistency and accuracy.
This progress benefits mold companies and provides reliable supplies to the manufacturing industry, driving growth in the sector.
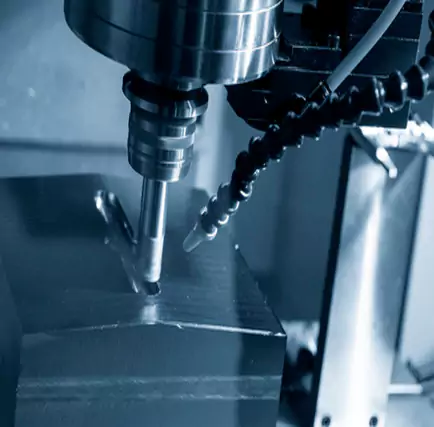
Application advantages and prospects
Therefore, the introduction of CNC machining technology has become an important means to improve and enhance mechanical mold manufacturing.
CNC machining technology is an advanced technology that uses computer-controlled machine tools for processing.It inputs the mold design drawings into the computer.
The machine tool is then automatically controlled based on the set parameters, ensuring high-precision processing.
Compared with traditional manual processing methods, CNC machining technology has the following advantages and prospects.
1. improve the precision of mold manufacturing
In addition, CNC machine tools, with their high speed and high precision, can complete the processing of complex molds in a shorter time, greatly improving efficiency and precision.
Unlike traditional methods that take days or even weeks, CNC technology can complete the same work in a few hours and can handle complex shapes such as curved surfaces and chamfers to ensure machining quality.
In short, CNC machining technology makes mold manufacturing more refined and efficient, bringing revolutionary changes to the industry.
As one expert said: “The introduction of CNC machining technology has transformed mold manufacturing from traditional extensive processing to refined and efficient processing, bringing revolutionary changes to the development of the mold industry.”
2. shorten the mold manufacturing cycle
The widespread use of CNC machining technology has significantly shortened the mold manufacturing cycle. In the past, manual mold processing required skilled craftsmen and was time-consuming, often prone to human errors.
Today, CNC machining allows machines to process molds accurately based on computer programs, improving both efficiency and precision.
For example, in the automotive industry, CNC technology quickly produces complex molds, greatly reducing the manufacturing cycle and enhancing production efficiency.
The automated nature of CNC machining is another key factor in shortening production time. Unlike manual processing, CNC technology minimizes human error and ensures stable mold quality.
In the aerospace industry, for instance, CNC machining produces high-precision aviation molds, which are essential for ensuring the safety and stability of aircraft.
CNC technology is also flexible and fast. With CNC programming, adjustments and modifications can be made at any time according to design needs, further reducing production time.
In electronics manufacturing, CNC technology can quickly produce different shell molds to meet varying consumer demands.
In conclusion, CNC machining technology significantly shortens the mold manufacturing cycle while improving both production efficiency and quality.
Whether in automotive, aerospace, or electronics manufacturing, CNC technology plays a critical role in industrial production.
Its continued advancement injects new vitality and innovation into the manufacturing industry, driving social and economic progress.
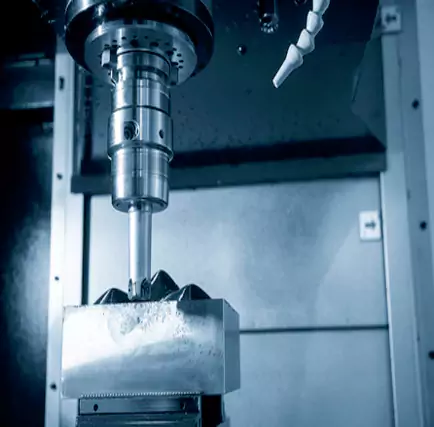
3. reduce the production cost of mold manufacturing
The introduction of CNC machining technology has revolutionized the mold manufacturing industry. Traditional mold manufacturing relies heavily on manual labor and is both time-consuming and costly. CNC technology enables high-precision, high-efficiency mold processing, greatly reducing production costs.
CNC technology eliminates errors caused by human factors in traditional processes. In manual mold machining, workers’ skills and experience are often influenced by subjective factors, leading to mistakes. CNC machines use precise computer control, ensuring accuracy and consistency in every step.
CNC machining also boosts efficiency. Machines can follow pre-programmed instructions to complete tasks automatically, reducing manual labor. This allows for continuous processing and batch production, significantly improving productivity. CNC technology also supports multi-axis simultaneous processing, which is ideal for complex molds.
Additionally, CNC technology reduces material waste. In traditional processing, errors and tool wear often lead to wasted materials. CNC machining optimizes tool paths and minimizes material loss, improving material utilization and lowering costs.
In conclusion, CNC machining lowers production costs in mold manufacturing. It reduces human error, increases efficiency, and cuts material waste. This technology gives companies a competitive edge, enhancing both production and profitability.
4. Application prospects
The application of CNC machining technology in mold manufacturing has vast potential. It enables automated precision cutting, drilling, milling, and other operations.
This technology achieves high-precision, high-efficiency mold production while significantly shortening the manufacturing cycle.
CNC machining makes the process more reliable, eliminates human error, and ensures mold quality and precision.
CNC technology can also handle the production of complex molds. By inputting 3D model data, machines can automatically process molds with intricate shapes.
Additionally, CNC technology supports surface treatments like etching and polishing. This flexibility makes mold design and production more versatile.
In conclusion, CNC machining has broad prospects in mold manufacturing. It enhances accuracy, improves efficiency, and shortens production times.
It also allows for the processing and flexible design of complex molds.
As CNC technology continues to evolve, the mold manufacturing industry will face new opportunities and challenges, leading to a brighter future.
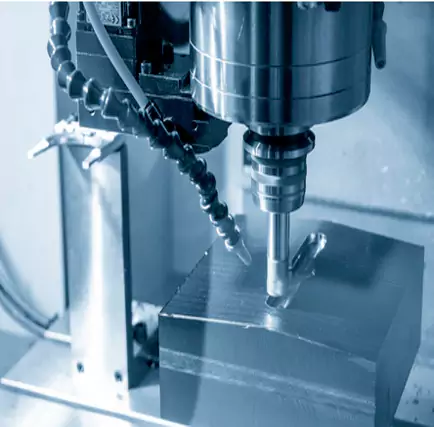
Conclusion
In summary, traditional mechanical mold manufacturing is complex and inefficient. It involves multiple steps like design, processing, and assembly.
Each stage requires experienced workers, making the process time-consuming and prone to errors.
However, CNC machining technology can address these issues. Its application is becoming a major trend in the mold manufacturing industry.
During the design phase, CNC technology can create complex shapes, reducing manual errors. In the processing stage, CNC machines provide precise control and automation, improving both quality and efficiency.
CNC technology also saves on labor, factory construction, and other costs. This aligns with business goals and sustainability needs. It has brought significant changes and opportunities to the mechanical mold industry.
By combining CNC machining with traditional methods, companies can boost production efficiency, lower costs, and improve product quality. This meets market demand and strengthens competitiveness. Therefore, mold manufacturers should adopt CNC technology to stay ahead in the industry.